棉短绒清理机检测的重要性
棉短绒清理机作为棉花加工产业链中的关键设备,其性能直接影响到短绒分离效率、原料损耗率及成品质量。该设备通过机械筛选、气流分离等方式清除棉纤维中的杂质和短绒,需在高速运转、粉尘环境下保持稳定运行。定期检测是确保设备安全性、优化生产效率的核心手段,可有效预防机械故障、降低能耗,并延长设备使用寿命。尤其对于长期处于高负荷工况的清理机,系统化检测能及时发现传动部件磨损、筛网堵塞、气流参数异常等问题,避免因设备失效导致原料浪费或生产停滞。
核心检测项目及方法
1. 设备结构与运行参数检测
通过三维激光扫描仪测量机架变形量,检测标准要求直线度偏差≤2mm/m。使用振动分析仪监测主轴轴承的径向跳动(应<0.08mm)及整机振动烈度(<4.5mm/s)。同步测试刺辊转速与理论值偏差(允许±3%),并验证传动系统温升(轴承温度≤75℃)。通过压力传感器监控除尘风道气流速度(18-22m/s)和静压差(800-1200Pa)。
2. 清理效能专项检测
采用标准化测试棉样(含杂率5%-8%)进行连续8小时负荷试验。使用激光粒度分析仪对比处理前后的杂质粒径分布,要求>500μm硬杂清除率≥98%。通过称重法计算短绒提取效率(目标值92%-95%)及纤维损伤率(<1.2%)。同步检测排杂系统的杂质残留量(单位时间<0.3kg/h)。
3. 安全与耐久性检测
依据GB/T 5226.1标准进行电气安全测试,包括绝缘电阻(≥10MΩ)、接地连续性(≤0.1Ω)。采用X射线探伤检测关键焊接部位的结构完整性。对刺辊钉齿进行维氏硬度检测(HRC58-62)及金相组织分析。模拟粉尘爆炸环境验证防爆装置的响应时间(<50ms)和抑爆效率。
4. 智能化功能验证
对具备自动调节功能的机型,需测试PLC控制系统对喂棉量波动的响应速度(≤2秒),验证筛网堵塞预警准确率(≥95%)。通过模拟电压波动(±15%)和温湿度变化(20-45℃/30-80%RH)检测控制系统的稳定性。采用工业相机捕捉物料运动轨迹,评估分料装置的动态调节精度(误差≤±3mm)。
检测周期与维护建议
常规生产季应每200小时进行参数校准,每季度实施全面性能检测。建议建立振动频谱数据库,通过趋势分析预判轴承寿命。检测后需重点维护除尘管道密封性、刺辊动平衡精度及光电传感器的清洁度,定期更换达到磨损阈值的钉齿(单齿磨损量>1.5mm时强制更换)。
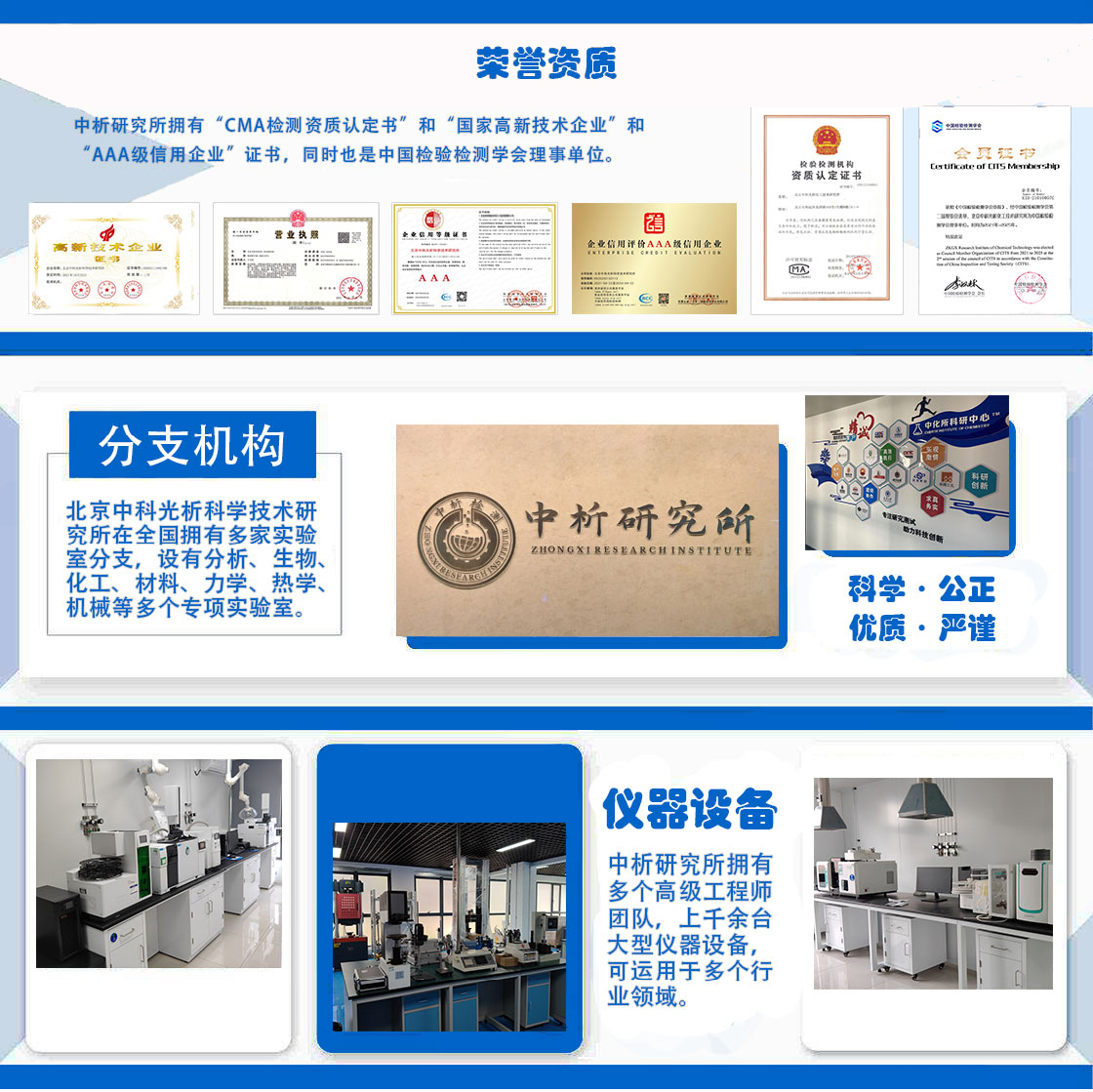
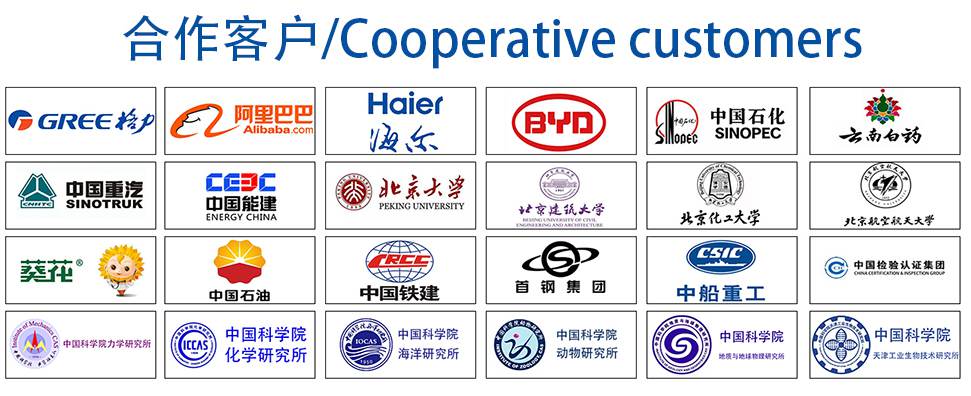