汽车电气/电子部件检测的重要性
随着汽车智能化、电动化技术的快速发展,电气/电子部件在整车系统中的占比已超过40%。从传统ECU到ADAS传感器,从动力电池管理系统到车载信息娱乐设备,这些核心组件的可靠性直接影响车辆安全性和用户体验。据行业统计,车辆故障中约65%与电气系统相关,而通过严格的检测流程可降低80%以上的质量风险。这要求检测技术必须覆盖功能验证、耐久测试、环境适应性评估等全维度指标,确保部件在全生命周期内的稳定运行。
关键检测项目与技术规范
1. 线束与连接器系统测试
采用高精度导通测试仪进行回路阻抗检测,验证电流路径完整性。通过振动台模拟16g加速度的机械冲击,检测连接器插拔寿命。使用IP67标准进行防水防尘测试时,需维持1米水深浸泡30分钟并监测绝缘性能变化。
2. ECU功能验证
基于ISO 26262功能安全标准,搭建HIL(硬件在环)测试平台。通过故障注入技术模拟电压波动(±20%)、短路/开路等异常工况,验证控制单元在极端条件下的容错机制。典型测试包括CAN总线通信稳定性、故障码触发逻辑及系统恢复能力验证。
3. 传感器动态精度检测
对毫米波雷达进行多普勒效应模拟,在-40℃至125℃温箱中测试目标识别率。采用六自由度运动平台,以0.1g分辨率校验加速度传感器的动态响应特性。使用光谱分析仪验证摄像头模组在不同照度(0.1lux至10^5lux)下的色彩还原度。
4. 动力电池系统评估
执行UN38.3认证要求的针刺、挤压、过充/过放测试。通过BMS模拟器验证SOC估算误差±3%以内,均衡电流偏差不超过标称值5%。在温控舱进行-30℃低温启动和55℃高温循环测试,记录电池包内温差≤5℃的热管理表现。
5. 电磁兼容性(EMC)测试
依据CISPR 25标准,在电波暗室进行辐射发射和抗扰度测试。使用瞬态脉冲发生器模拟ISO 7637-2规定的12V/24V抛负载波形,检测部件能否承受100V/μs的电压突变。同时对CAN总线实施BCI大电流注入法,验证通信抗干扰能力。
智能化检测技术发展
新兴的AI检测系统已实现部件缺陷的毫秒级识别,X射线断层扫描可对BGA封装芯片进行三维焊点质量分析。基于数字孪生的虚拟测试技术,能在产品设计阶段预判90%以上的潜在失效模式。随着ISO 21434网络安全标准的推行,车载系统的渗透测试和固件校验将成为必检项目。
通过构建覆盖研发、生产、售后全流程的检测体系,汽车电子部件的平均故障间隔时间(MTBF)已提升至5000小时以上。未来随着800V高压架构和域控制器的普及,检测技术将向着更高精度、更快响应、更智能化的方向持续演进。
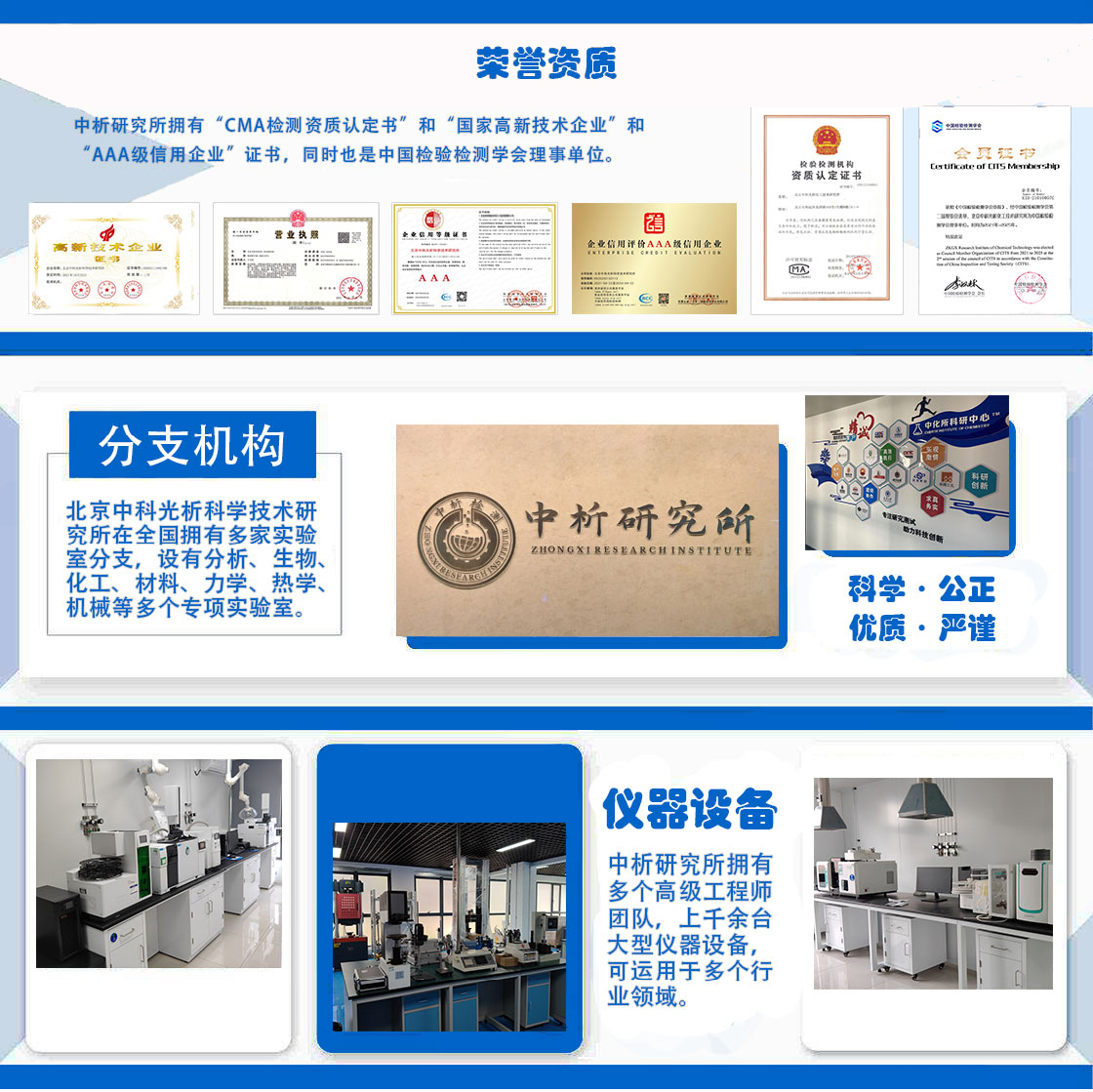
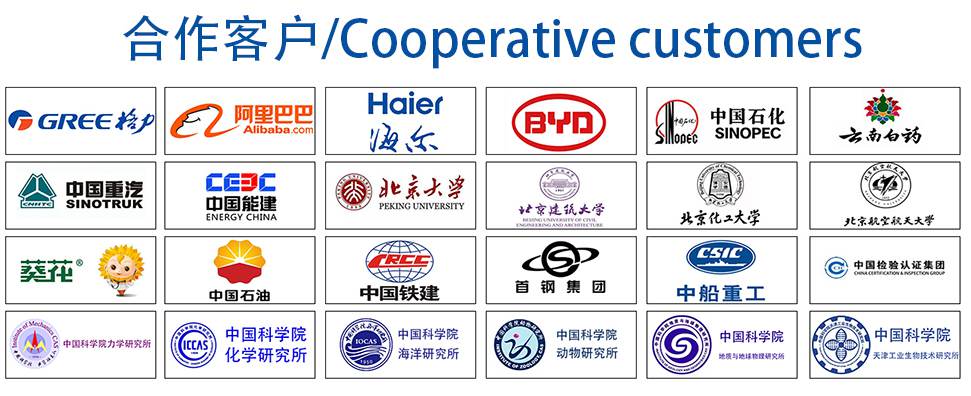