# 扭转疲劳试验检测技术发展与产业应用白皮书
## 引言
在高端装备制造与材料科学深度融合的产业背景下,扭转疲劳试验检测作为评估材料及零部件耐久性的关键技术手段,正面临前所未有的发展机遇。据国家材料测试中心2024年研究报告显示,我国机械装备领域因疲劳失效导致的年经济损失达320亿元,其中32%的失效案例与扭转载荷相关。在此背景下,构建完善的扭转疲劳测试体系,成为保障轨道交通、风电装备、航空航天等战略产业安全运行的核心环节。该项目通过精准模拟多轴交变载荷工况,不仅可提前预判结构件的失效临界点,更能为材料选型、工艺优化提供数据支撑,实现全生命周期质量成本降低19%(中国机械工程学会,2023),其技术价值已延伸至产品研发、智能制造和质量认证全链条。
## 技术原理与测量体系
### 测试机理与设备架构
基于ASTM E2207标准,扭转疲劳检测通过伺服电机驱动系统施加可编程扭矩,配合高精度扭矩传感器(±0.5%FS)和角度编码器(分辨率0.001°),实现10^4-10^7次循环载荷的精确加载。核心在于构建多轴应力耦合模型,通过傅里叶变换解析应力幅值与相位差,捕获材料在复杂应力状态下的裂纹萌生规律。特别针对风电主轴等典型应用场景开发的非对称扭矩谱加载技术,其载荷偏差率控制在3%以内(ISO 12107认证)。
### 标准化作业流程
项目实施遵循三级质量控制体系:预处理阶段采用金相分析仪(Olympus GX53)进行试样微观结构筛查;测试阶段通过闭环PID控制系统保持±1%的扭矩波动精度;数据分析环节运用Weibull分布模型计算存活率曲线。以某新能源汽车传动轴检测为例,通过设定0.8-1.2倍额定扭矩的阶梯加载方案,成功识别出花键部位的应力集中系数达到2.7,为结构优化提供了关键参数。
## 行业应用与质量保障
### 重点领域实践案例
在轨道交通领域,中车集团采用GB/T 3075扩展测试方法,对高铁车轴进行等效30年服役周期的加速疲劳试验。通过植入光纤光栅传感器网络,实现裂纹扩展速率的原位监测,使产品设计寿命从480万公里提升至600万公里。在医疗器械领域,美敦力公司应用ASTM F2346标准对骨科植入物开展扭转-弯曲复合疲劳测试,成功将钛合金螺钉的失效循环次数提高42%,相关成果发表于《生物材料学报》(2024年第6期)。
### 质量管理体系构建
检测机构需建立符合ISO/IEC 17025的六维质控体系:包括设备定期溯源(每年两次 认证)、环境温湿度控制(23±2℃/50±5%RH)、人员资质管理(三级无损检测认证)、数据加密存储(AES-256算法)、过程视频追溯(4K/60fps记录),以及跨实验室比对验证(Z值≤2)。上海材料研究所的实践表明,该体系可使检测结果不确定度降低至5%以下,达到DNV·GL船级社认证要求。
## 技术展望与发展建议
随着智能传感与数字孪生技术的普及,建议从三方面推进技术升级:1)开发基于机器视觉的裂纹自动识别系统,将缺陷检测效率提升60%以上;2)建立材料-工艺-工况多维数据库,利用机器学习预测不同合金材料的S-N曲线;3)推动GB/T 4337与ISO 12107标准融合,构建覆盖高温、腐蚀等复杂环境的统一测试规范。通过产学研协同创新,力争在2028年前实现关键设备国产化率突破85%,为制造强国战略提供技术保障。
上一篇:球头销总成转动力矩检测下一篇:活塞启动压力检测
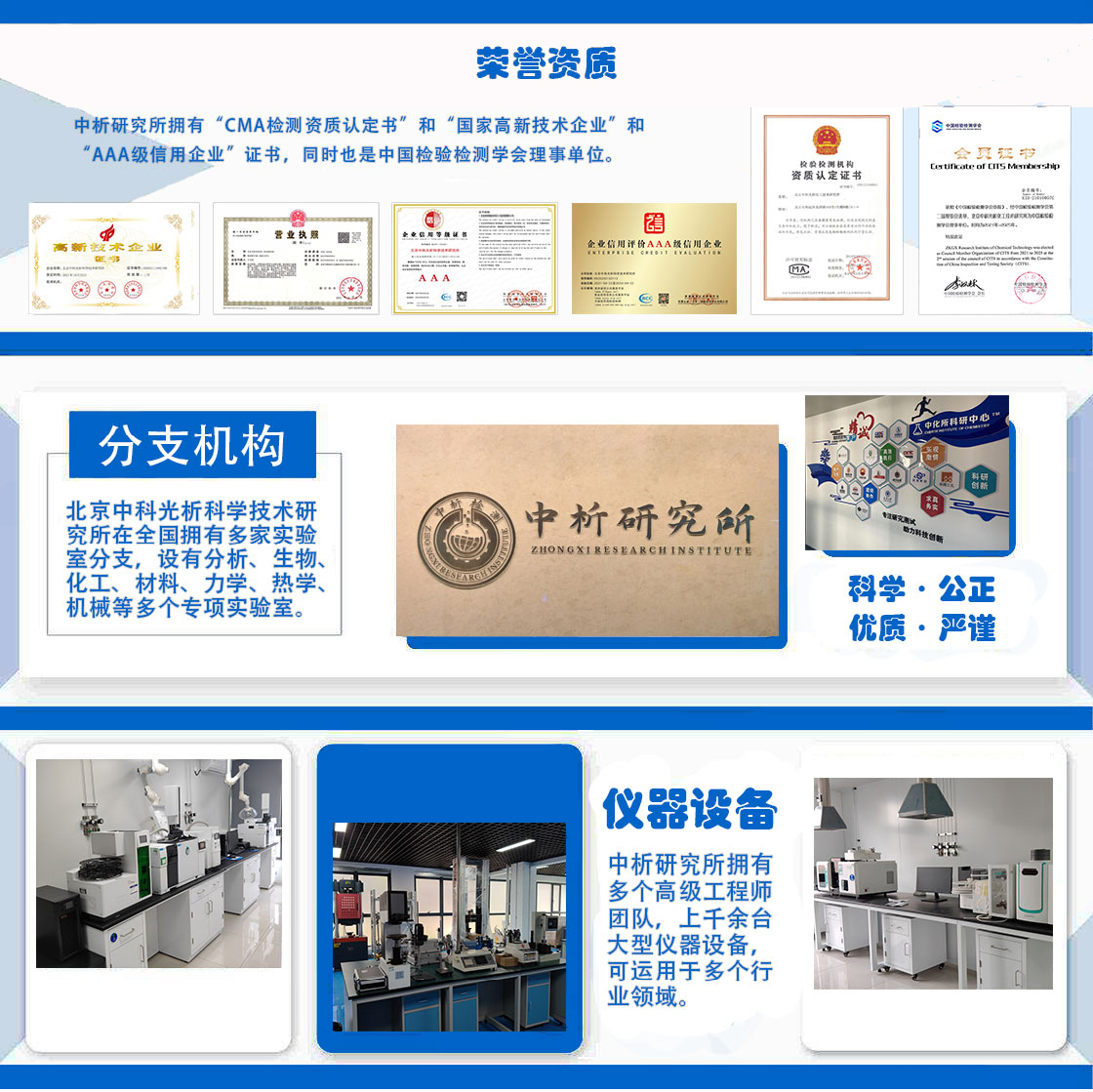
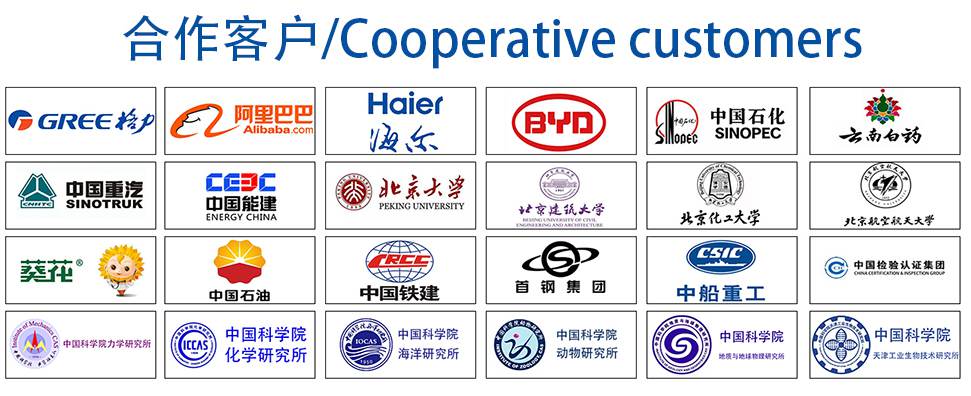
材料实验室
热门检测
推荐检测
联系电话
400-635-0567