电火花小孔高速加工机床检测技术解析
电火花小孔高速加工机床(EDM小孔机)是一种通过放电腐蚀原理实现微小孔加工的特种设备,广泛应用于航空航天、精密模具、医疗器械等领域的高硬度或复杂材料加工中。随着工业对微孔加工精度和效率要求的提升,机床的检测与性能评估成为确保加工质量、延长设备寿命的关键环节。检测项目需覆盖机床的机械精度、放电系统稳定性、加工效率、表面质量以及安全防护等多个维度,以全面评估设备的综合性能。
一、机床几何精度检测
几何精度是电火花小孔机的基础性能指标,直接影响加工孔的位置精度和形状一致性。主要检测项目包括:
1. 主轴垂直度与轴向跳动:使用激光干涉仪或精密水平仪测量主轴在加工方向上的垂直度误差,确保主轴运动轨迹与工件平面垂直;
2. 工作台平面度与重复定位精度:通过高精度平晶或三坐标测量机评估工作台表面平整度,验证重复定位误差是否在±2μm以内;
3. 导向系统间隙检测:检查Z轴导轨的间隙和刚性,避免加工过程中因振动导致的孔径偏差。
二、放电参数与能量稳定性检测
电火花加工的核心在于放电能量的精确控制,需重点检测以下内容:
1. 脉冲电源输出特性:使用示波器监测脉冲宽度、间隔时间和峰值电流的稳定性,确保放电参数与预设值匹配;
2. 放电间隙电压波动:通过动态信号分析仪记录加工过程中间隙电压的波动范围,判断极间绝缘状态是否正常;
3. 能量利用率测试:对比输入电能与材料去除率,评估机床的能效比,优化加工效率。
三、加工性能与表面质量检测
加工效果是机床综合性能的直接体现,需进行多维度验证:
1. 孔径一致性测试:采用非接触式光学测量仪检测同一批次加工孔的直径误差,要求误差≤±0.005mm;
2. 孔壁粗糙度分析:使用表面轮廓仪或激光共聚焦显微镜测量孔内壁Ra值,评估放电参数对表面质量的影响;
3. 锥度与圆度检测:通过截面投影仪分析孔的几何形状,确保锥度误差小于0.5°。
四、安全防护与智能化功能检测
现代电火花小孔机普遍配备智能化系统,需验证其安全性及自动化能力:
1. 液位与温度报警系统测试:模拟工作液泄漏或异常温升场景,确认防护装置触发响应时间≤1秒;
2. 电极自动更换精度验证:检测电极库的定位重复精度是否满足±0.002mm要求;
3. 加工过程监控能力:通过数据采集系统检查机床对短路、电弧等异常状态的识别与处理效率。
通过对上述关键项目的系统性检测,可有效保障电火花小孔高速加工机床的长期稳定运行,并显著提升微小孔加工的合格率与生产效率。建议企业结合ISO 9001质量管理体系要求,建立定期检测规范,最大化发挥设备的技术优势。
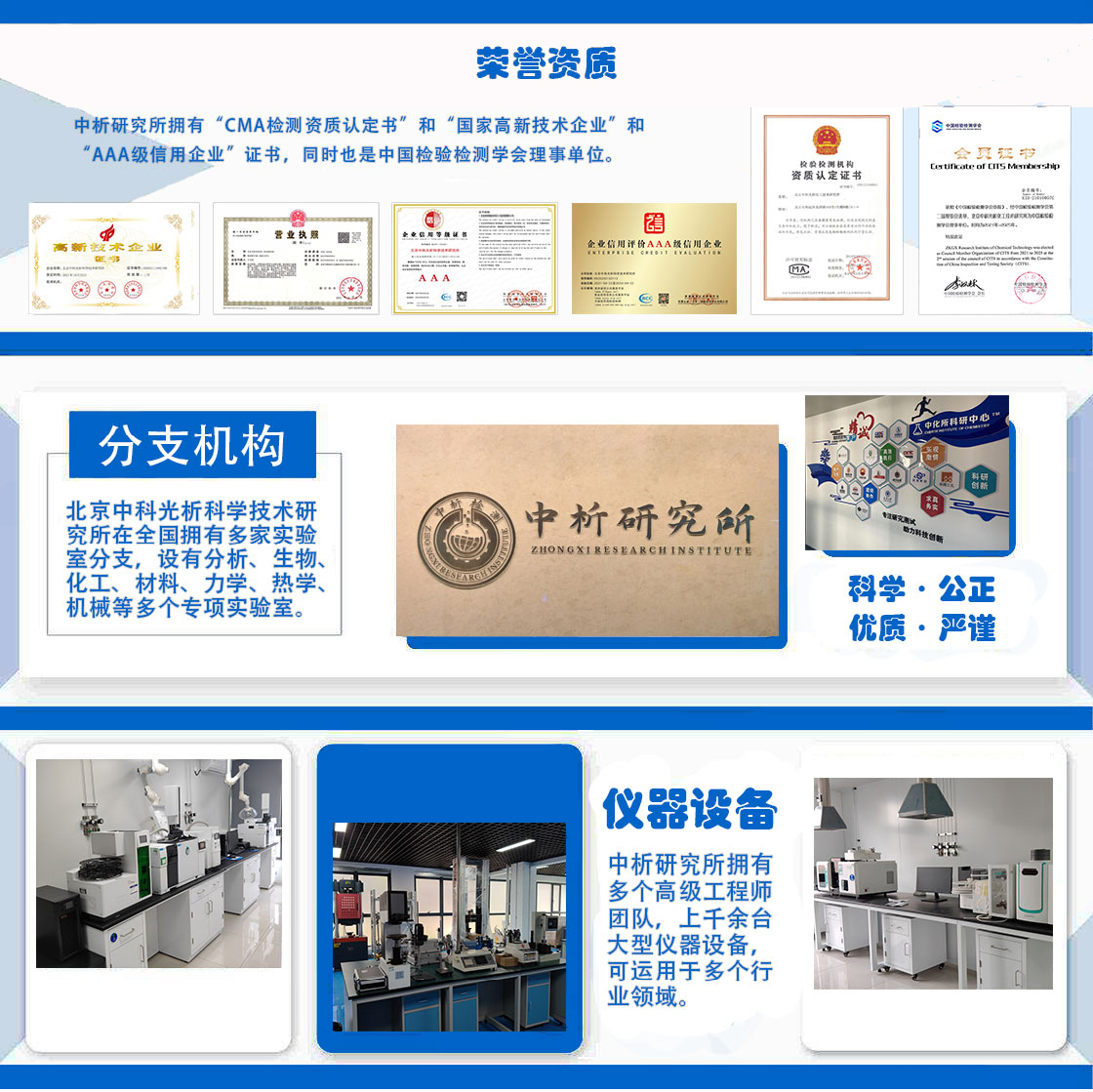
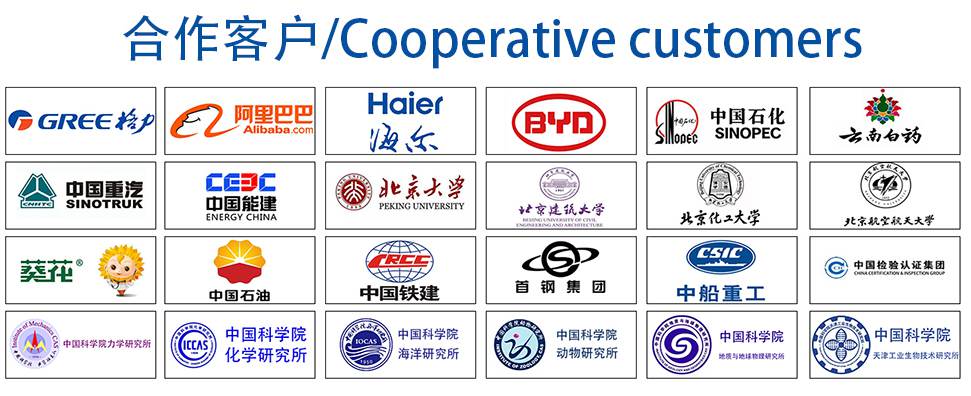