核级铅酸蓄电池检测:守护核设施安全的生命线
在核电站、核燃料处理厂等核设施中,核级铅酸蓄电池作为应急电源系统的核心部件,承担着极端工况下为安全控制系统、紧急停堆装置提供持续电力的重要使命。这类蓄电池需满足IAEA(国际原子能机构)和GB/T 19638.2-2014《固定型阀控式铅酸蓄电池》等严苛标准,其检测工作直接关系到核设施运行的可靠性与人员生命安全。相较于普通工业蓄电池,核级铅酸蓄电池需在抗震性能、辐射耐受性、极端温度适应能力等维度实现技术突破,因此其检测项目呈现出专业化、系统化、多维度化的显著特征。
核心检测项目体系
1. 基础性能检测
包含外观完整性检查(壳体密封性、极柱防护等级)、容量验证测试(采用恒流放电法测定20小时率容量)、内阻测量(交流注入法检测≤0.1%精度要求)等基础指标。特别关注蓄电池在40℃高温和-20℃低温环境下的容量保持率,要求容量衰减不得超过标称值的15%。
2. 电气特性专项检测
通过智能充放电测试系统验证循环寿命(≥1200次@50% DOD)、充电接受能力(2小时恢复≥95%容量)、自放电率(月自放电≤3%)等关键参数。重点执行UL 1973标准要求的过充/过放保护测试,确保电池管理系统在异常工况下的快速响应能力。
3. 安全性能验证
包含耐震动试验(模拟SSE安全停堆地震工况)、阻燃性能测试(UL94 V-0级)、防爆性能验证等特殊项目。针对核环境特点,需额外进行γ射线辐照试验(累计剂量100kGy)和LOCA事故模拟测试(85℃/85%RH持续720小时)。
4. 材料成分分析
采用ICP-OES光谱仪对极板铅膏(铅含量≥99.997%)、隔板玻璃纤维(直径≤3μm)、电解液硫酸(纯度99.999%)等关键材料进行成分检测,严格管控镉、锑等重金属杂质含量(≤0.002%)。
全生命周期质量管控
核级铅酸蓄电池实施"设计-制造-服役"三阶段检测机制:设计阶段需通过FMEA故障模式分析;生产阶段执行100%在线监测与批次抽样破坏性检测;服役期间每季度开展内阻谱分析(EIS)和剩余容量预测(RUL),并建立电池健康状态(SOH)数字化档案。通过X射线断层扫描(CT)等无损检测技术,可精准识别极板硫化、活性物质脱落等潜在缺陷。
检测技术发展趋势
随着数字孪生技术在核电领域的应用,基于大数据分析的智能诊断系统正逐步替代传统检测手段。通过植入式光纤传感器可实时监测电池内部温度场分布,结合AI算法实现故障预警准确率提升至98%以上。未来,满足第四代核反应堆需求的耐高温铅碳电池(工作温度150℃)检测技术将成为研发重点。
在核安全文化理念驱动下,核级铅酸蓄电池检测已从单一的性能验证发展为涵盖材料科学、电力电子、失效分析等多学科交叉的综合性技术体系。只有构建起覆盖全产业链的严格检测网络,才能确保这一"核电生命线"设备在关键时刻的绝对可靠性。
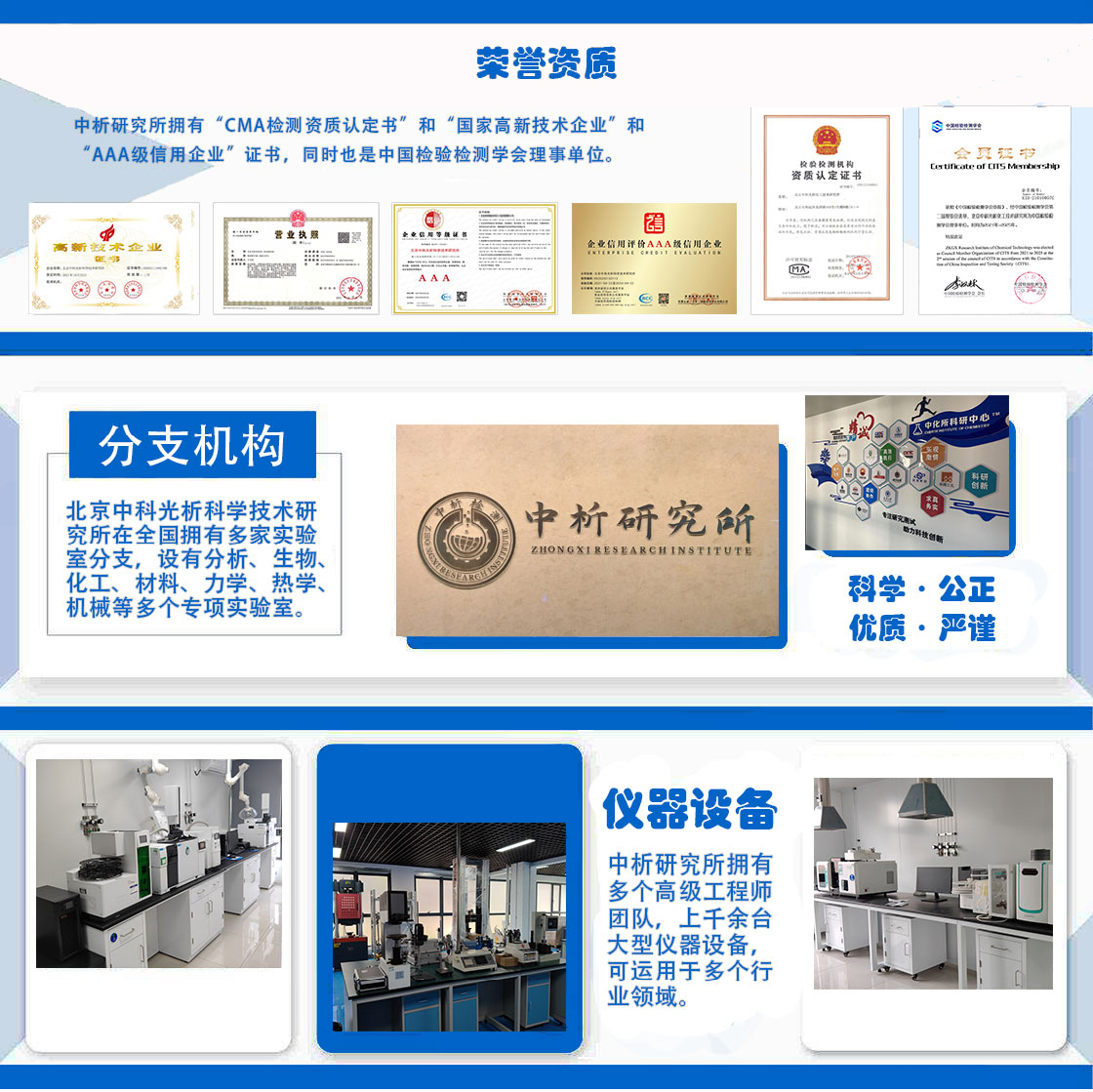
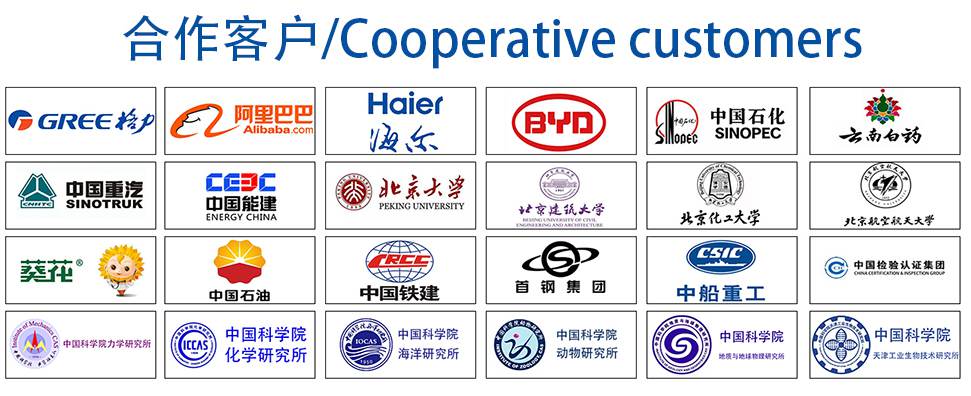