内圆磨床(参数)检测技术要点及方法解析
内圆磨床作为精密加工领域的关键设备,其参数性能直接影响工件内孔加工精度与表面质量。为确保设备运行稳定并满足工艺要求,需对核心参数进行系统性检测。检测项目需涵盖尺寸精度、动态特性、电气性能及机械部件配合度等维度,通过科学手段验证设备是否符合技术标准,从而规避因设备参数偏差导致的产品批量缺陷风险。
一、内圆磨床核心检测项目清单
1. 主轴系统检测:包括主轴径向跳动(≤0.003mm)、轴向窜动(≤0.002mm)及转速稳定性(±1%额定值)测量,使用激光干涉仪与振动传感器进行动态测试。
2. 砂轮架参数验证:检测砂轮轴回转精度(≤0.005mm)、进给重复定位精度(±0.002mm)以及冷却系统流量(10-15L/min)等关键指标。
3. 几何精度检测:包含机床导轨直线度(0.01mm/m)、工作台平面度(0.008mm)与主轴轴线对工作台面的垂直度(0.015mm/300mm)。
4. 数控系统性能测试:验证伺服驱动响应时间(≤50ms)、位置分辨率(0.1μm)和程序执行同步性误差(≤3μs)。
二、典型参数检测方法与工具
1. 圆度检测:采用高精度气浮转台配合电容式测微仪,执行ISO 1101标准下的V型块三点测量法,采样频率≥100Hz。
2. 振动频谱分析:使用三轴加速度传感器采集磨削过程振动信号,通过FFT频谱分析识别主轴轴承(500-2000Hz频段)与齿轮箱(50-500Hz)异常频率成分。
3. 热变形监测:在连续8小时运行工况下,使用红外热像仪检测床身温度场分布,配合激光跟踪仪测量关键部位热位移量(≤0.01mm/℃)。
三、检测数据评估与校正策略
检测数据需通过SPC统计过程控制分析,对CPK值<1.33的关键参数实施三级校正:一级调整机械间隙补偿(0.001mm级)、二级优化伺服增益参数、三级更换超标部件。典型校正案例表明,系统化检测可使内圆磨削圆度精度提升40%,表面粗糙度Ra值稳定在0.2μm以内。
四、检测周期与标准依据
建议执行季度预防性检测(ISO 13041-6标准)与年度全面校准(GB/T 17421.2)。重点参数检测需在(20±1)℃恒温环境下进行,检测前需进行4小时热机运转,确保设备达到热平衡状态。
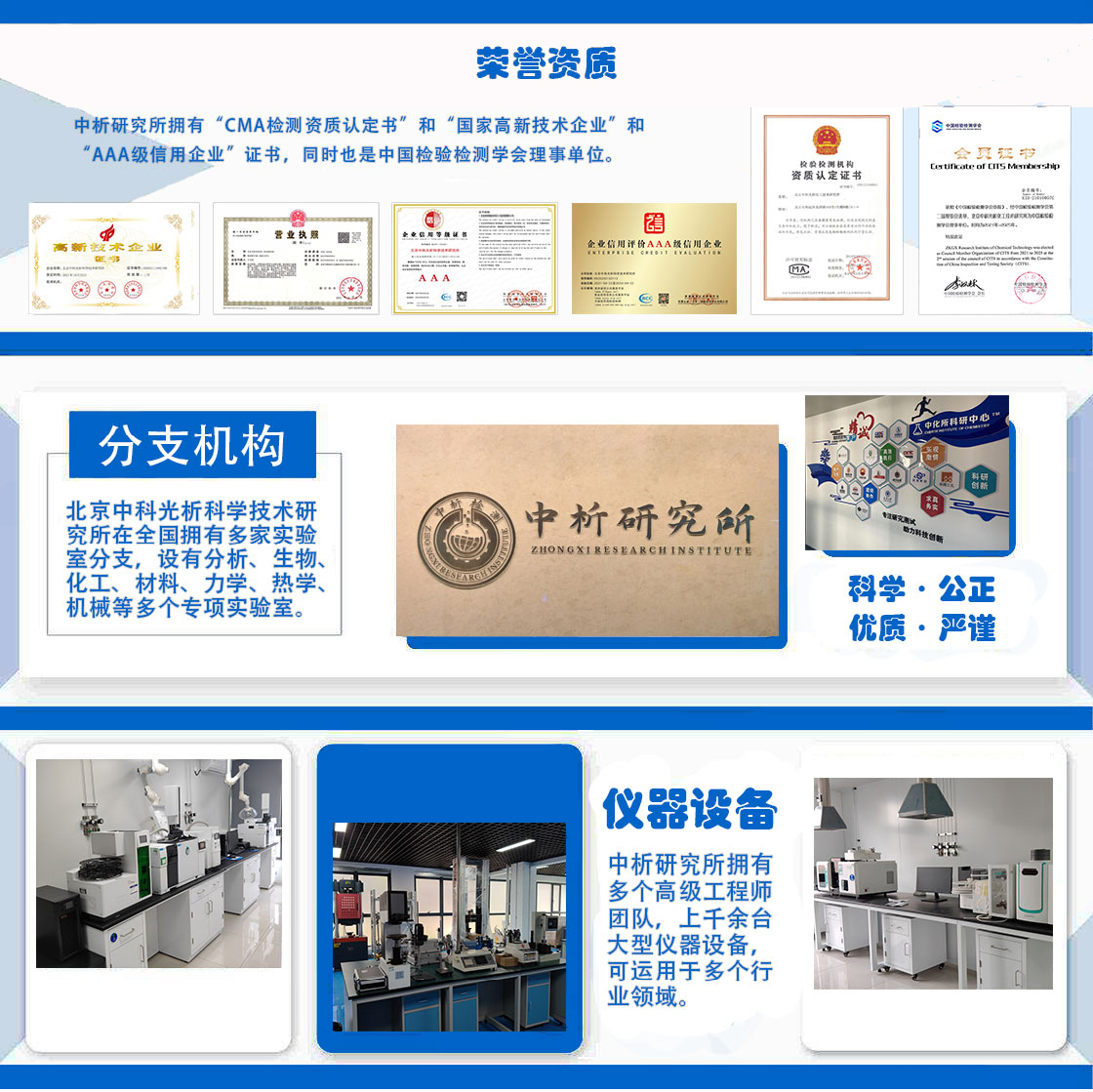
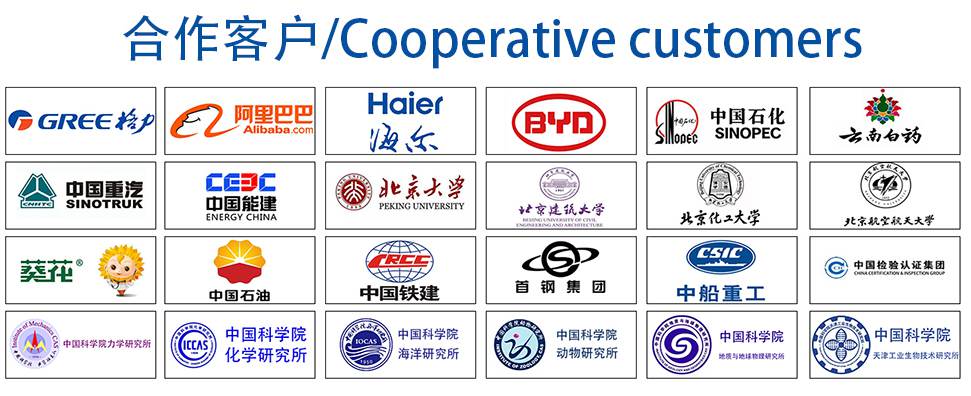