汽车轮毂轴承单元检测的重要性
汽车轮毂轴承单元作为连接车轮与悬挂系统的核心部件,承担着支撑整车重量、传递驱动力及确保行驶稳定性的关键作用。其性能直接影响车辆的操控性、安全性和能耗表现。随着车辆行驶里程增加或极端工况下的使用,轮毂轴承单元可能出现磨损、变形、润滑失效等问题,轻则引发异响和振动,重则导致车轮脱落等严重事故。因此,定期开展系统性检测是保障行车安全、延长部件寿命的重要环节。
核心检测项目及方法
1. 外观与尺寸检测
通过目视检查轴承单元表面是否存在裂纹、锈蚀、变形等缺陷,使用千分尺、游标卡尺等工具测量内外圈直径、滚道宽度等关键尺寸,确保符合制造商公差要求(通常允许偏差±0.02mm)。重点关注密封圈完整性,防止污染物侵入。
2. 轴向游隙测量
采用专业游隙检测仪对轴承单元的轴向间隙进行精确测定。乘用车标准游隙值一般控制在0.05-0.15mm范围内,超出阈值会导致异常振动。测试时需模拟实际负载状态,确保测量结果反映真实工况。
3. 旋转阻力测试
使用扭矩传感器检测轴承单元在额定转速下的旋转阻力矩(通常要求≤2.5N·m)。异常阻力值可能预示润滑脂劣化、滚道损伤或装配不当。同步记录运行平稳性,排除间歇性卡滞现象。
4. 密封性能验证
将轴承单元置于防水试验台,以0.2-0.3MPa压力进行水密性测试,持续30分钟观察渗漏情况。同时检查防尘盖与密封唇的配合紧密度,确保达到IP6K9K防护等级标准。
5. 振动与噪声分析
利用振动频谱仪采集轴承运转时的振动信号,重点监测1-5kHz高频段特征频率。配合声级计进行异响识别,通过时域波形和包络谱分析判断早期损伤类型(如点蚀、剥落等)。
6. 耐久性试验
在模拟工况测试台上进行加速寿命试验,加载1.2-1.5倍额定载荷,连续运转200小时后检测性能衰减程度。评估指标包括温升曲线(标准≤80℃)、扭矩波动值和磨损量变化。
检测设备与技术进展
现代检测已引入智能化解决方案:三维光学扫描仪实现微米级形貌重建,多通道数据采集系统可同步监测20+动态参数,AI算法通过历史数据预测剩余寿命。这些技术将传统检测精度提升40%,故障识别率提高至98%以上。
结语
系统化的轮毂轴承单元检测不仅能预防突发故障,更能通过数据积累优化维护周期。建议每2万公里或12个月进行专业检测,极端使用环境下应缩短至1万公里/6个月。选择具备ISO/IEC17025认证的检测机构,可确保测试结果的权威性和可比性。
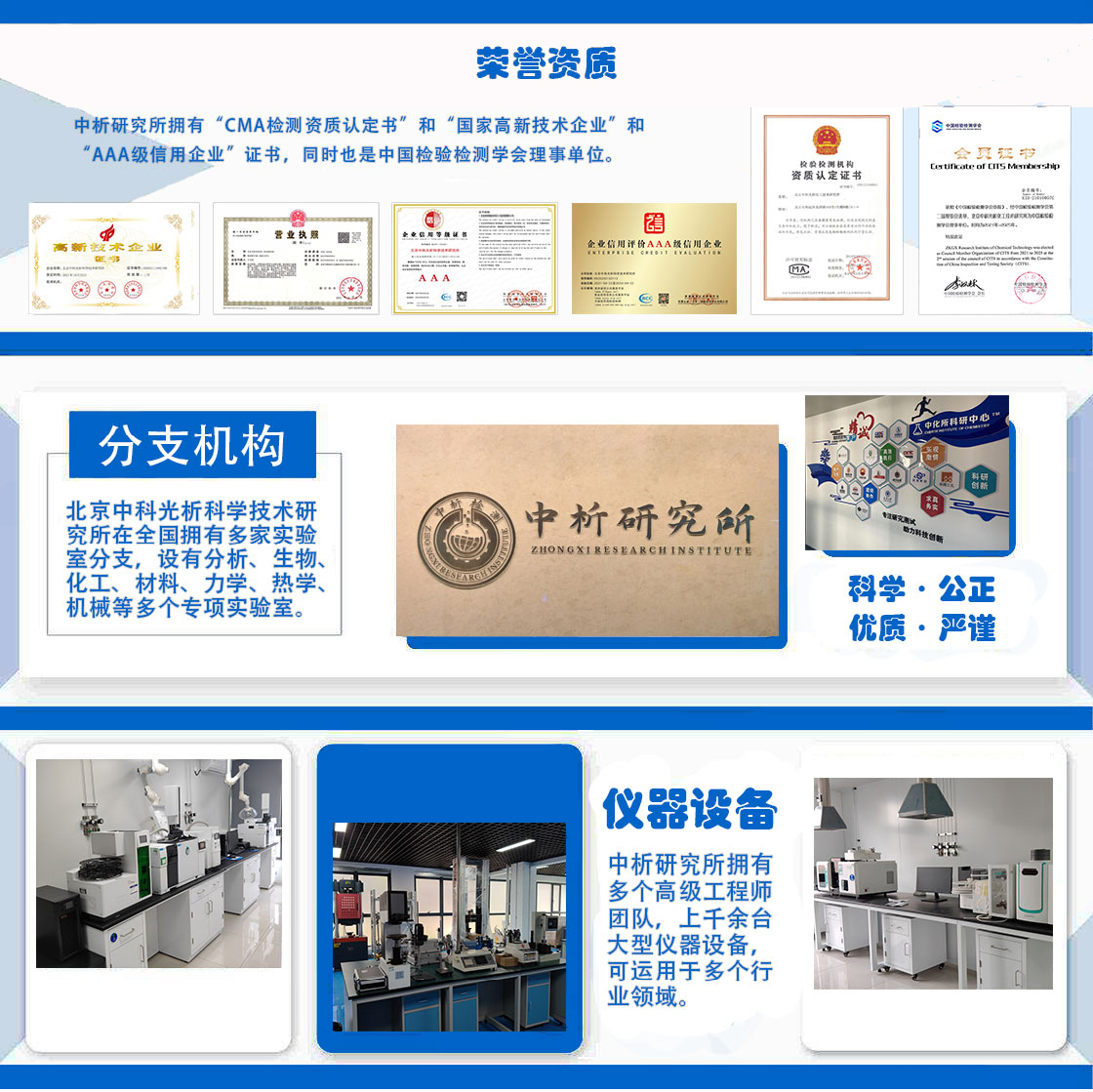
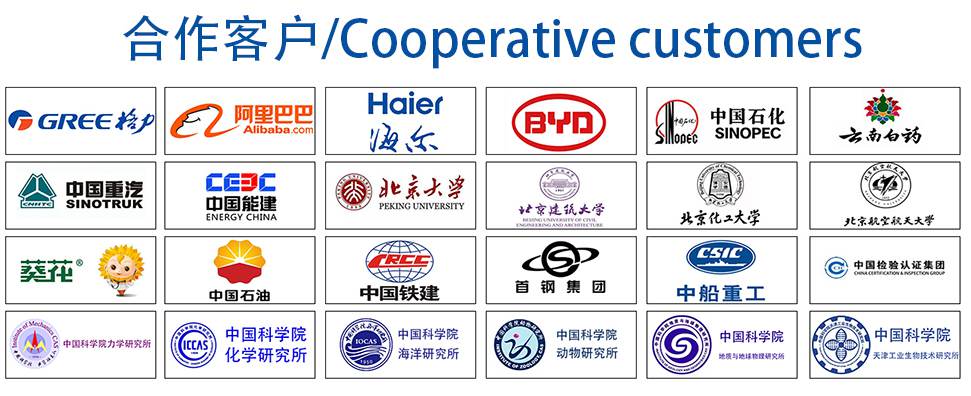