微型球轴承检测关键技术及核心项目解析
在精密机械制造领域,微型球轴承(通常指内径≤10mm的微型滚动轴承)作为关键基础零部件,其性能直接影响精密仪器、医疗器械、无人机舵机等设备的运行精度与使用寿命。随着工业4.0时代的到来,微型轴承的检测技术已从传统人工测量发展到智能检测阶段,检测范围覆盖几何精度、材料性能、动态特性等二十余项关键指标。严格的检测流程可有效避免因轴承失效导致的设备停机,据统计,规范的检测程序可提升产品良率35%以上,延长使用寿命超2000小时。
核心检测项目体系
1. 几何精度检测:使用三坐标测量机(CMM)进行精密尺寸测量,重点检测内径、外径、宽度尺寸公差(通常要求±0.001mm),沟道圆度误差(≤0.3μm),以及内外圈端面平行度。采用激光干涉仪检测旋转精度时,径向跳动需控制在0.5μm以内。
2. 材料性能检测:通过显微硬度计测试套圈硬度(HRC58-62),使用金相显微镜分析GCr15轴承钢的碳化物分布(要求带状组织≤2级)。振动频谱分析可检测材料内部缺陷,异常频谱峰值超过基准线15%即判定为不合格。
3. 动态性能测试:在专用试验机上模拟实际工况,检测启动力矩(通常≤0.3mN·m)、额定转速下的温升(ΔT≤15℃)及振动值(速度型振动≤0.8mm/s)。噪音检测需在消音室内进行,A计权声压级不超过35dB。
齐全检测技术应用
工业CT断层扫描技术可非破坏性检测内部装配质量,准确识别保持架间隙(≤0.02mm)和钢球分布均匀性。智能图像处理系统通过2000帧/秒的高速摄像捕捉润滑脂分布状态,油脂覆盖率需达到95%以上。最新研发的纳米级表面轮廓仪可检测沟道表面粗糙度Ra值(目标≤0.05μm),比传统触针式仪器精度提升10倍。
质量控制关键节点
在量产阶段实施SPC统计过程控制,对关键尺寸进行CPK能力指数监控(要求≥1.67)。每批次抽样进行300小时加速寿命试验,故障率超过0.5%即触发质量追溯程序。出厂前100%进行气密性检测,确保防水轴承在0.2MPa压力下无泄漏。
通过构建涵盖设计验证、过程监控、成品检验的全维度检测体系,配合MES系统实现检测数据实时上传与智能分析,可使微型球轴承的故障返修率降低至0.02%以下,为高端装备制造提供可靠的基础件保障。
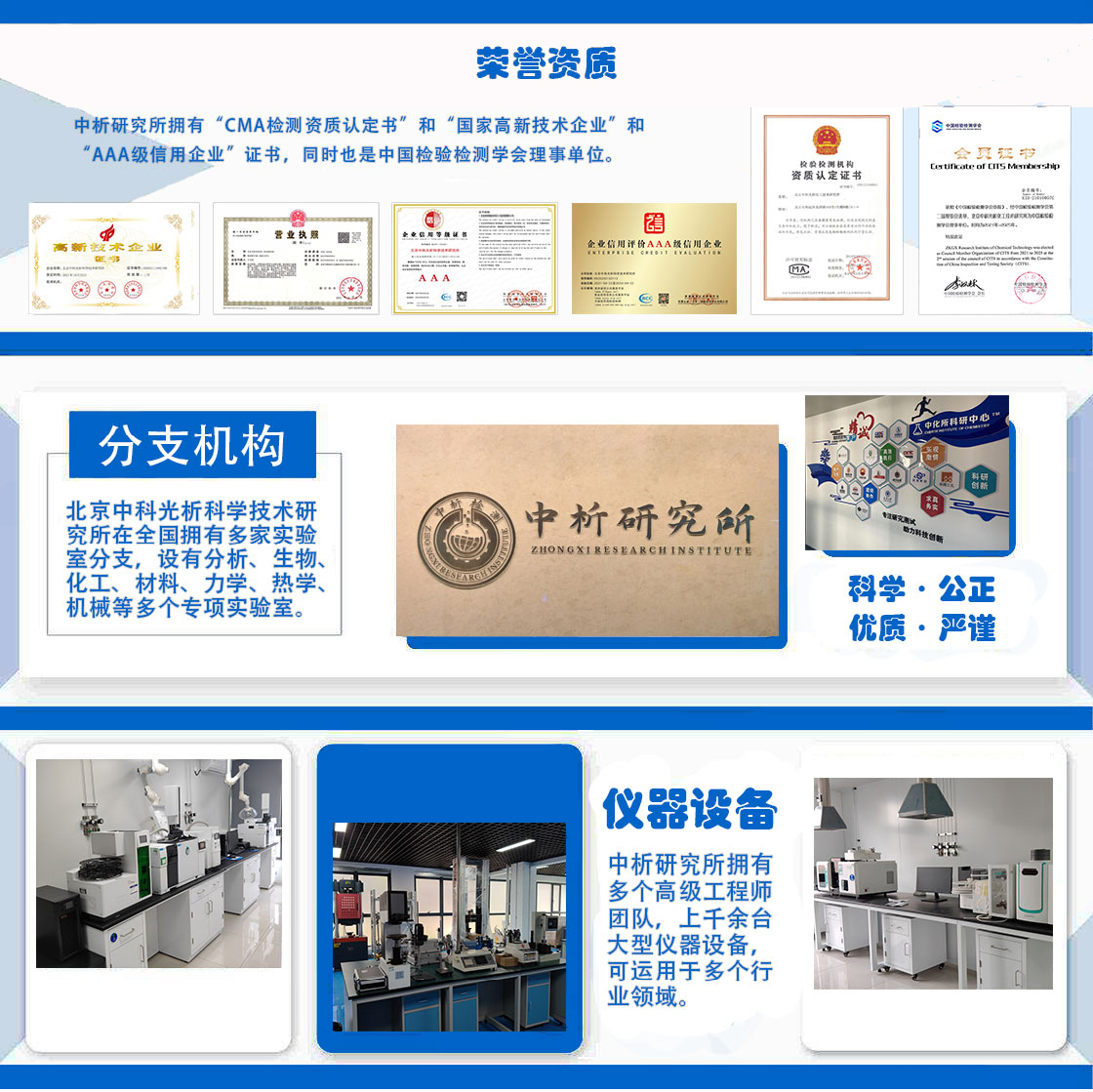
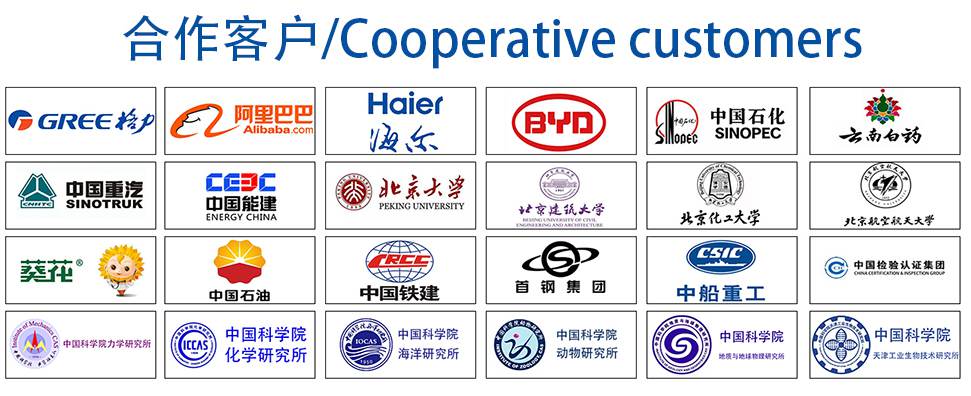