圆柱滚子超精机检测项目的关键内容与流程
圆柱滚子超精机是精密机械制造中用于提升圆柱滚子表面精度和几何形状的关键设备,其性能直接影响轴承、传动系统等核心零部件的质量。为确保设备加工能力和成品符合标准,需对超精机进行系统化检测。检测项目涵盖设备静态精度、动态性能、加工效果评估及环境适应性分析,贯穿设备调试、生产验证和日常维护全周期,是保障加工效率与产品质量的核心环节。
一、设备基础精度检测
1. 主轴回转精度检测:采用激光干涉仪或高精度球杆仪,测量主轴径向跳动和轴向窜动,精度需控制在1μm以内;
2. 导轨直线度检测:使用电子水平仪配合激光跟踪仪,检测X/Y/Z轴导轨的直线度误差,要求全行程误差≤3μm/m;
3. 定位精度验证:通过光栅尺和数控系统联动测试,重复定位精度需达到±0.5μm。
二、加工性能专项检测
1. 表面粗糙度测试:使用触针式轮廓仪或白光干涉仪,检测加工后滚子表面的Ra值(通常要求Ra≤0.05μm);
2. 圆度与圆柱度分析:采用高精度圆度仪配合CMM三坐标测量机,评估滚子截面圆度(目标值≤0.3μm)及全长圆柱度(≤1.5μm);
3. 波纹度检测:通过频谱分析仪识别加工表面周期性缺陷,抑制频率需覆盖50-5000Hz范围。
三、动态工艺参数监控
1. 振动频谱分析:安装加速度传感器监测主轴和砂轮架的振动幅值,主频段振幅应<0.5mm/s;
2. 切削力实时检测:采用动态测力仪记录超精研过程中的法向/切向力,波动范围控制在±5%以内;
3. 温度场监控:红外热像仪监测关键部件温升,确保工作温度稳定在20±1℃范围内。
四、智能化检测技术应用
1. 机器视觉在线检测:集成CCD相机实现滚子表面缺陷的实时识别,检测分辨率达0.1mm²;
2. 数字孪生系统构建:通过传感器网络建立设备数字模型,实现加工误差的预测性补偿;
3. 大数据分析平台:采集历史检测数据建立工艺参数优化模型,降低批量生产中的质量波动。
随着ISO 1101:2017几何公差标准和VDI/VDE 2617检测规范的推行,圆柱滚子超精机的检测正向自动化、智能化方向发展。通过建立涵盖机械精度、加工性能、动态参数的全维度检测体系,可有效提升设备综合加工能力30%以上,同时降低废品率至0.02%以下,为高端装备制造提供可靠保障。
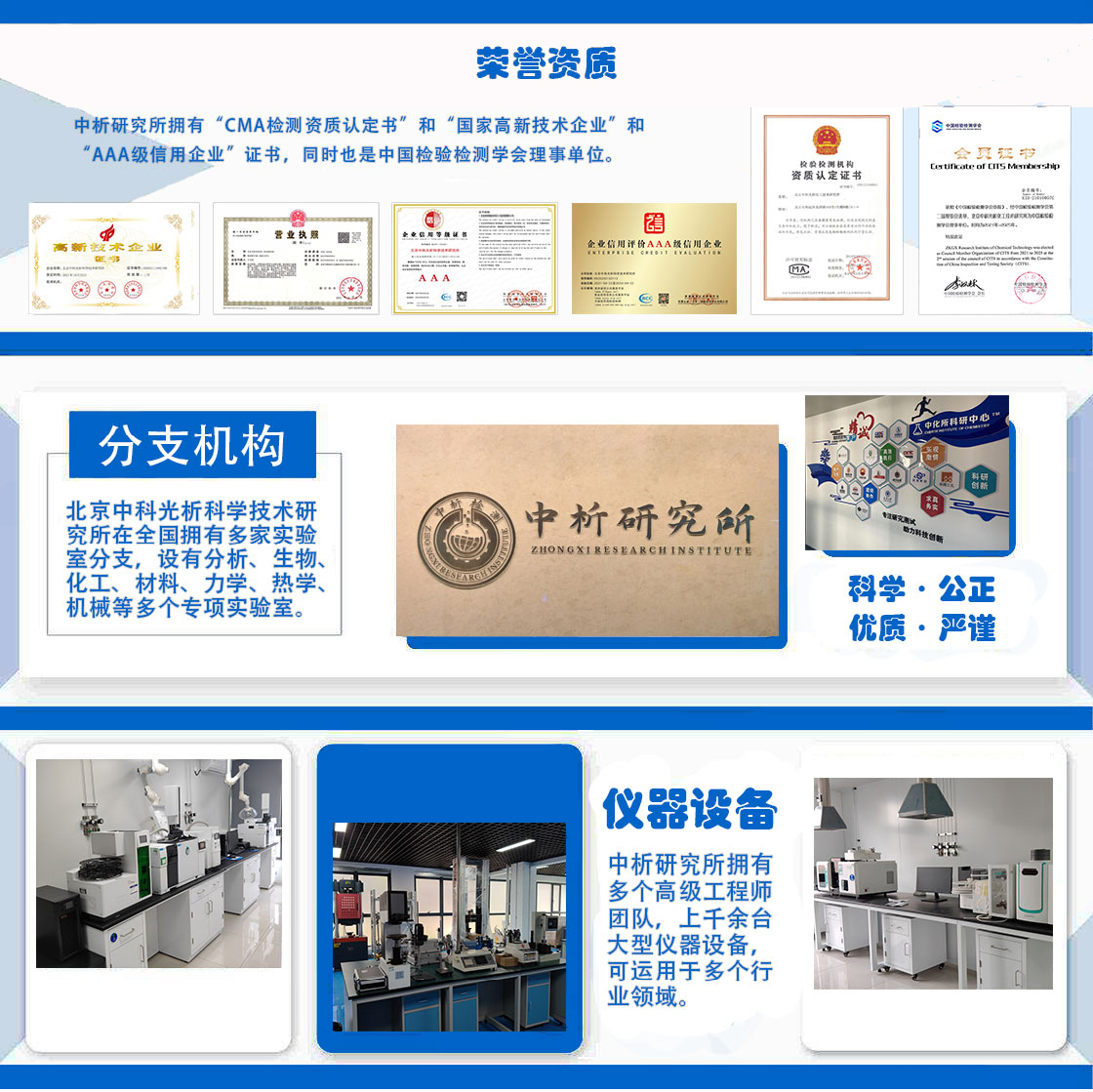
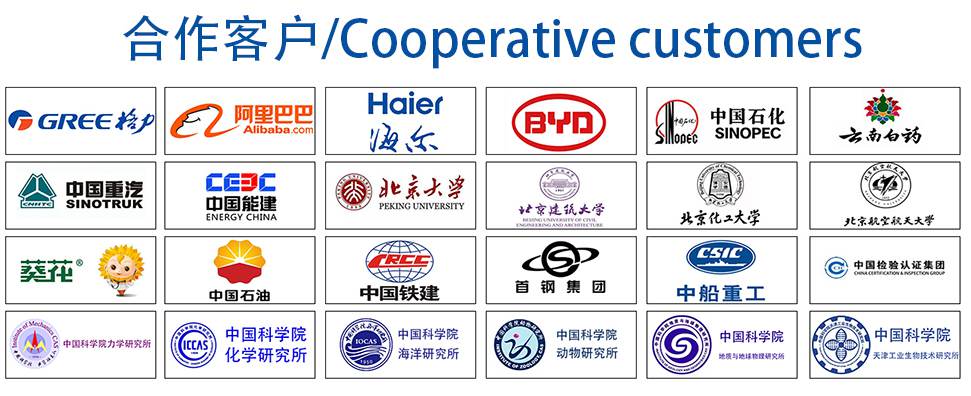