碳钢球检测的重要性及应用领域
碳钢球作为工业领域中的关键零部件,广泛应用于轴承、阀门、机械传动系统及精密仪器中。其性能直接影响到设备的运行效率、使用寿命和安全性。为确保碳钢球在复杂工况下的可靠性,需通过科学严格的检测项目评估其材质、尺寸精度、表面质量和力学性能。随着制造业对精度和耐用性要求的提升,碳钢球检测已成为产品质量控制的核心环节,涉及化学成分分析、硬度测试、尺寸公差验证等多个维度。
碳钢球检测的核心项目
1. 化学成分分析
通过光谱仪或化学滴定法检测碳钢球中碳(C)、硅(Si)、锰(Mn)、硫(S)、磷(P)等元素的含量,确保符合GB/T 699、ASTM A29等标准要求。碳含量直接影响钢球的硬度和韧性,需精确控制在目标范围内。
2. 硬度与力学性能测试
采用洛氏硬度计(HRC)或维氏硬度计(HV)测定表面硬度,并通过拉伸试验评估抗拉强度、屈服强度及延伸率。高硬度可减少磨损,但需与材料的韧性达到平衡,避免脆性断裂。
3. 尺寸精度与几何公差检测
使用精密千分尺、光学投影仪或三坐标测量仪(CMM)测量直径误差、圆度、球面度及表面粗糙度(Ra值)。碳钢球的尺寸公差通常需满足ISO 3290标准中G5-G100级精度要求,具体取决于应用场景。
4. 表面质量与缺陷检查
通过目视检查、磁粉探伤或涡流检测排查裂纹、划痕、锈蚀等表面缺陷。对于高负荷应用场景,需借助金相显微镜观察微观组织是否存在夹杂、气孔等内部缺陷。
5. 耐腐蚀性与环境适应性测试
依据ASTM B117标准进行盐雾试验,评估碳钢球在潮湿或腐蚀性环境中的抗锈蚀能力。若需长期暴露于特殊介质中,还需进行定制化化学耐受性测试。
6. 金相组织分析
通过金相显微镜观察材料的晶粒度、珠光体与铁素体分布,判断热处理工艺是否合理。均匀细密的组织可提升钢球的耐磨性和疲劳寿命。
检测标准与质量控制流程
碳钢球的检测需严格遵循ISO 3290、GB/T 308、DIN 5401等国际或行业标准。制造商通常结合原材料检验、生产过程监控及成品抽检的三阶段控制模式,通过自动化检测设备与人工复检相结合,确保批量化生产质量的稳定性。
结语
随着智能检测技术的普及,碳钢球检测正朝着高精度、高效率方向发展。通过多维度的检测项目与数据化分析,企业能够精准识别潜在质量风险,优化生产工艺,从而在汽车、航空航天、能源装备等领域提供更可靠的解决方案。
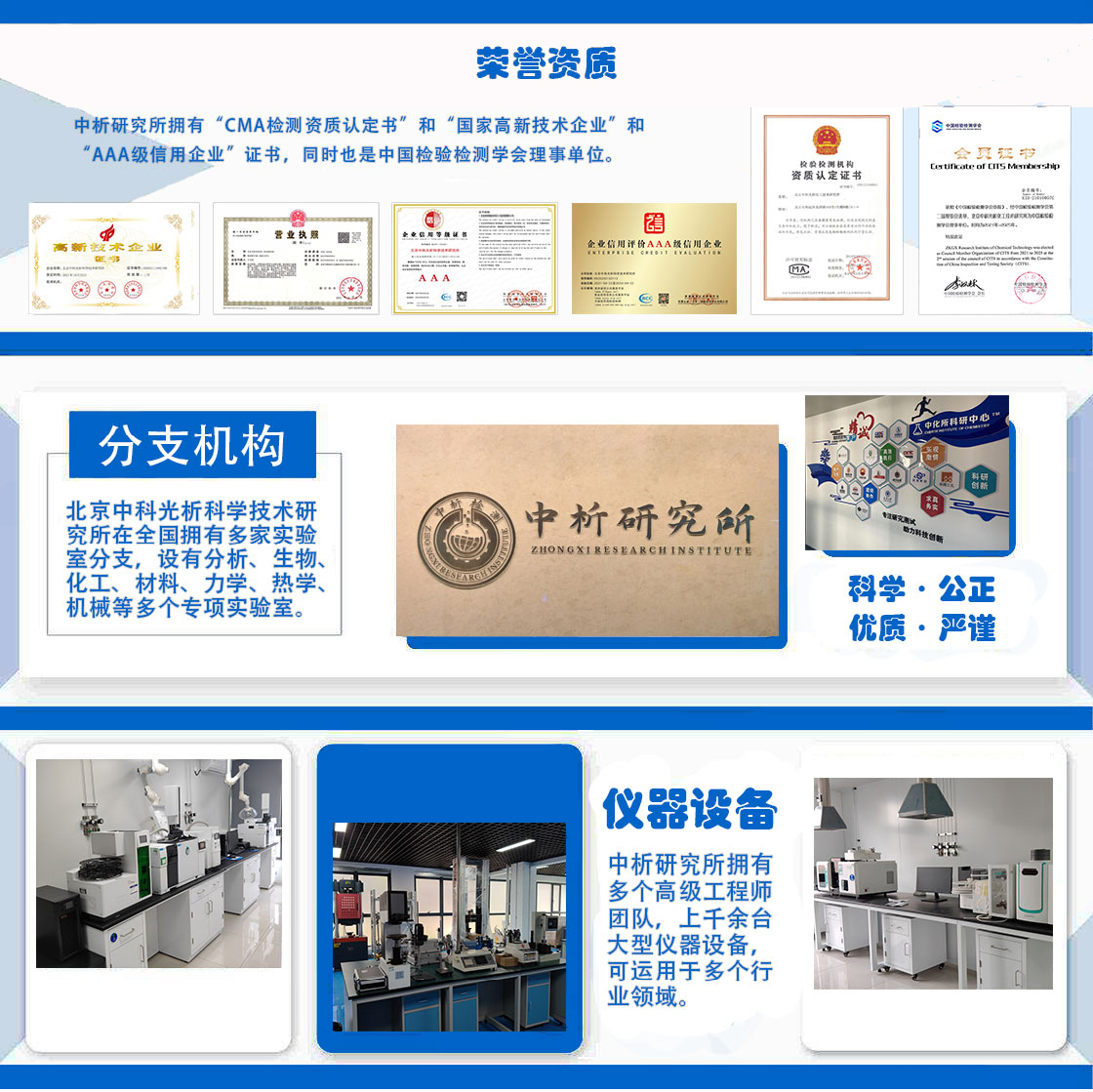
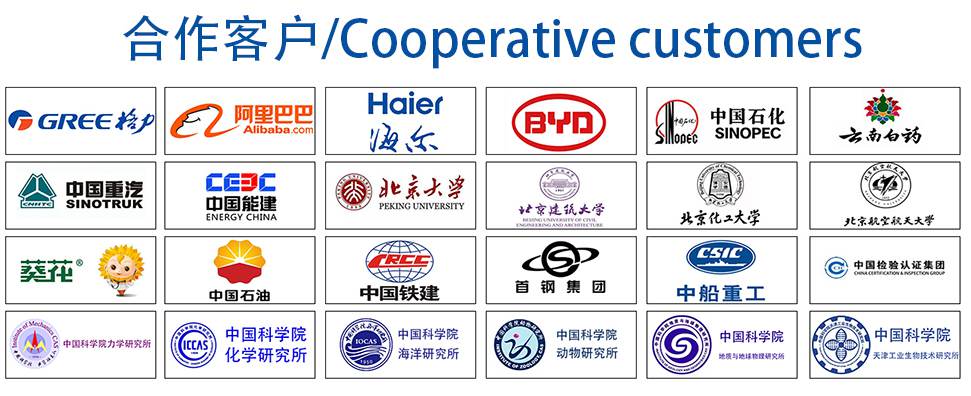