电动汽车用动力蓄电池单体、模块检测的必要性与挑战
随着电动汽车产业的快速发展,动力蓄电池作为整车的核心能源部件,其性能、安全性及可靠性直接决定了车辆的续航能力、使用寿命和用户安全。动力蓄电池单体和模块作为电池系统的基础单元,需经过严格的检测流程以确保其符合国家标准(如GB/T 31484-2015、GB/T 31485-2015等)及国际规范(如UN R100、ISO 12405)。检测内容涵盖电性能、安全性能、环境适应性、循环寿命等多维度指标,旨在从源头把控电池质量,降低因电池故障引发的安全风险,并为整车企业提供可靠的技术支撑。
动力蓄电池单体检测的核心项目
1. 电性能测试
包括容量测试、充放电效率、内阻测试、开路电压测试等,通过模拟实际工况验证电池的能量输出稳定性。例如,容量测试需在特定温度下以恒定电流充放电,确保实际容量与标称值偏差小于5%。
2. 安全性能测试
重点针对过充、过放、短路、针刺、挤压、热失控等极端场景进行验证。例如,针刺测试要求将直径3-8mm的钢针以特定速度刺穿电池单体,观察是否发生起火或爆炸,以评估电池内部短路时的安全性。
3. 环境适应性测试
涵盖高低温循环(-40℃至60℃)、湿热循环、振动冲击等,模拟电池在极端气候和复杂路况下的耐受能力。例如,高温存储测试需将电池置于55℃环境中保持48小时,观察其容量恢复率和外观变化。
4. 循环寿命测试
通过数千次充放电循环,评估电池容量衰减率。通常要求动力电池在标准循环下(如1C充放电)的容量保持率在80%以上,以确保其满足整车8年或15万公里的使用寿命需求。
动力蓄电池模块检测的关键环节
1. 一致性评估
对模块内各单体电池的电压、内阻、容量等参数进行匹配度分析,确保模块整体性能均衡。一致性偏差过大会导致局部过充/过放,加速模块老化。
2. 热管理测试
验证模块在充放电过程中的温度分布及散热效率。通过红外热成像技术监测热点,并结合液冷或风冷系统的有效性分析,避免热失控连锁反应。
3. 机械强度测试
包括振动测试(模拟车辆行驶中的机械应力)、跌落测试(模拟运输或碰撞场景)以及模块固定结构的耐久性评估,确保电池组在动态环境中的结构完整性。
4. 绝缘与耐压测试
检测模块内部绝缘材料的可靠性,防止漏电风险。耐压测试通常要求模块在1.5倍工作电压下保持60秒无击穿现象。
行业标准与未来趋势
当前动力电池检测主要依据国标、欧标及企业自定规范,但随着快充技术、固态电池等新技术的应用,检测项目将更加复杂。未来,结合AI算法的智能检测系统、实时监测大数据平台将进一步提升检测效率与精度,推动动力电池向高安全、长寿命、低成本方向发展。
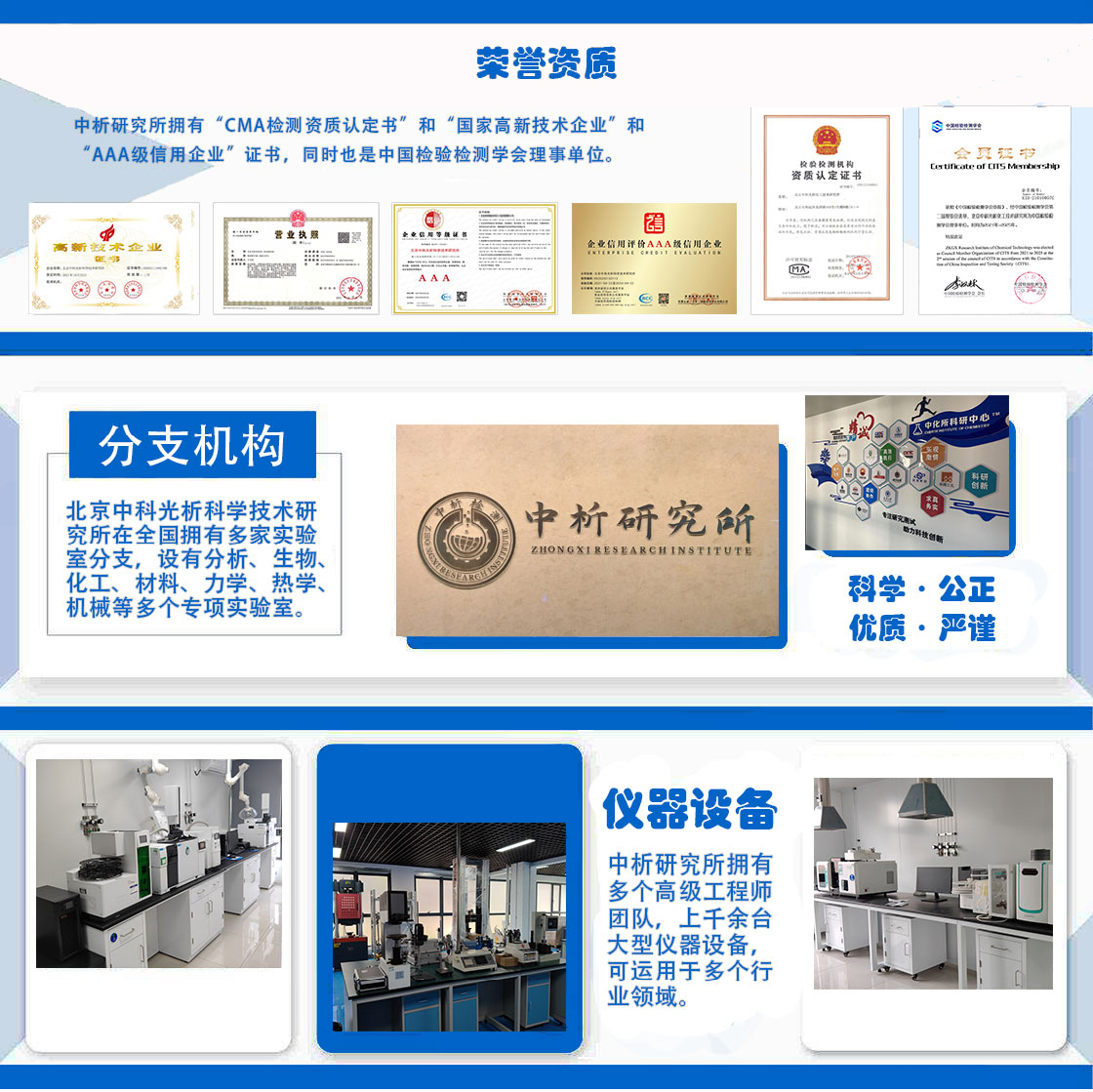
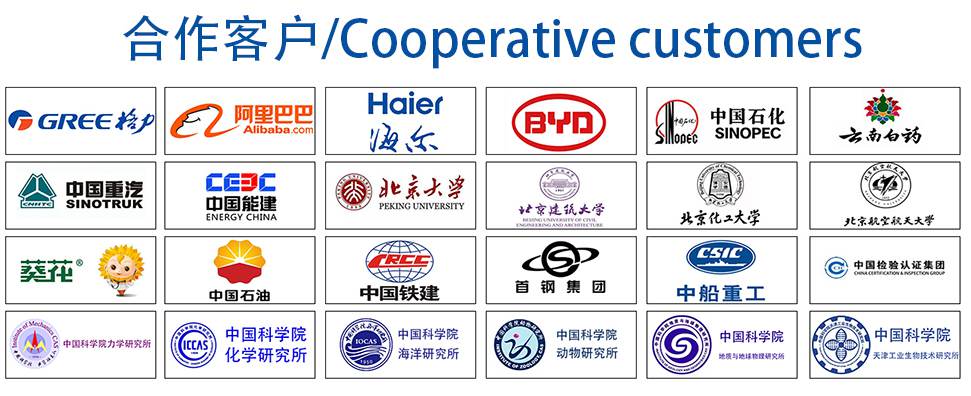