工业环境中设备检测的重要性与核心项目
在工业生产领域,设备的稳定运行是保障生产效率、安全性和成本控制的核心要素。随着自动化、智能化技术的普及,工业设备的复杂性显著提升,其检测需求也从传统的故障排查演变为系统性、多维度的预防性维护。通过科学规范的检测手段,企业能够提前识别潜在风险,延长设备寿命,减少非计划停机时间,同时满足安全生产法规要求。
工业设备检测的核心项目
1. 机电性能检测
包括电机电流、电压、功率因数等参数的实时监测,通过振动分析仪、红外热成像仪等工具评估设备的机械传动效率与电气系统稳定性。例如,轴承异常磨损可通过振动频谱分析提前预警,避免突发性故障。
2. 结构完整性检测
利用超声波探伤、磁粉检测等技术对压力容器、管道焊接部位进行无损检测,识别裂纹、腐蚀或变形。针对高温高压设备,还需进行壁厚测量与应力分布模拟,确保承压部件符合安全标准。
3. 安全防护装置检测
对紧急制动系统、安全光栅、防爆电气设备的响应速度和功能有效性进行验证。需模拟过载、短路等极端工况,确保防护装置在突发情况下能可靠触发并切断危险源。
4. 环境适应性检测
针对湿度、粉尘、腐蚀性气体等特殊工况,评估设备的密封性能与材料耐候性。例如,通过盐雾试验箱模拟海洋环境,检测金属部件的抗腐蚀涂层有效性。
5. 自动化控制系统检测
对PLC、DCS等控制模块的输入/输出信号精度、逻辑程序执行情况进行验证,同时检查传感器与执行器的校准状态。需通过冗余测试确保系统在部分组件失效时仍能维持基础功能。
6. 能耗与排放检测
采用流量计、气体分析仪等设备监测能源消耗效率及废气排放指标,优化设备运行参数以实现绿色生产目标。重点排查空压机、锅炉等能耗大户的热效率损失问题。
7. 数字化管理系统验证
针对配备IoT传感器的智能设备,需检查数据采集的完整性、传输稳定性及云端分析平台的预警功能。确保预测性维护模型与实际运行数据的匹配度,避免误报或漏报。
检测流程的标准化与创新趋势
现代工业检测正逐步向数字化、智能化转型。通过结合AI故障诊断算法、数字孪生技术以及移动端实时监测平台,企业可建立覆盖设备全生命周期的健康管理体系。同时,标准化检测流程的制定与第三方认证的引入,将进一步推动行业检测质量的提升。
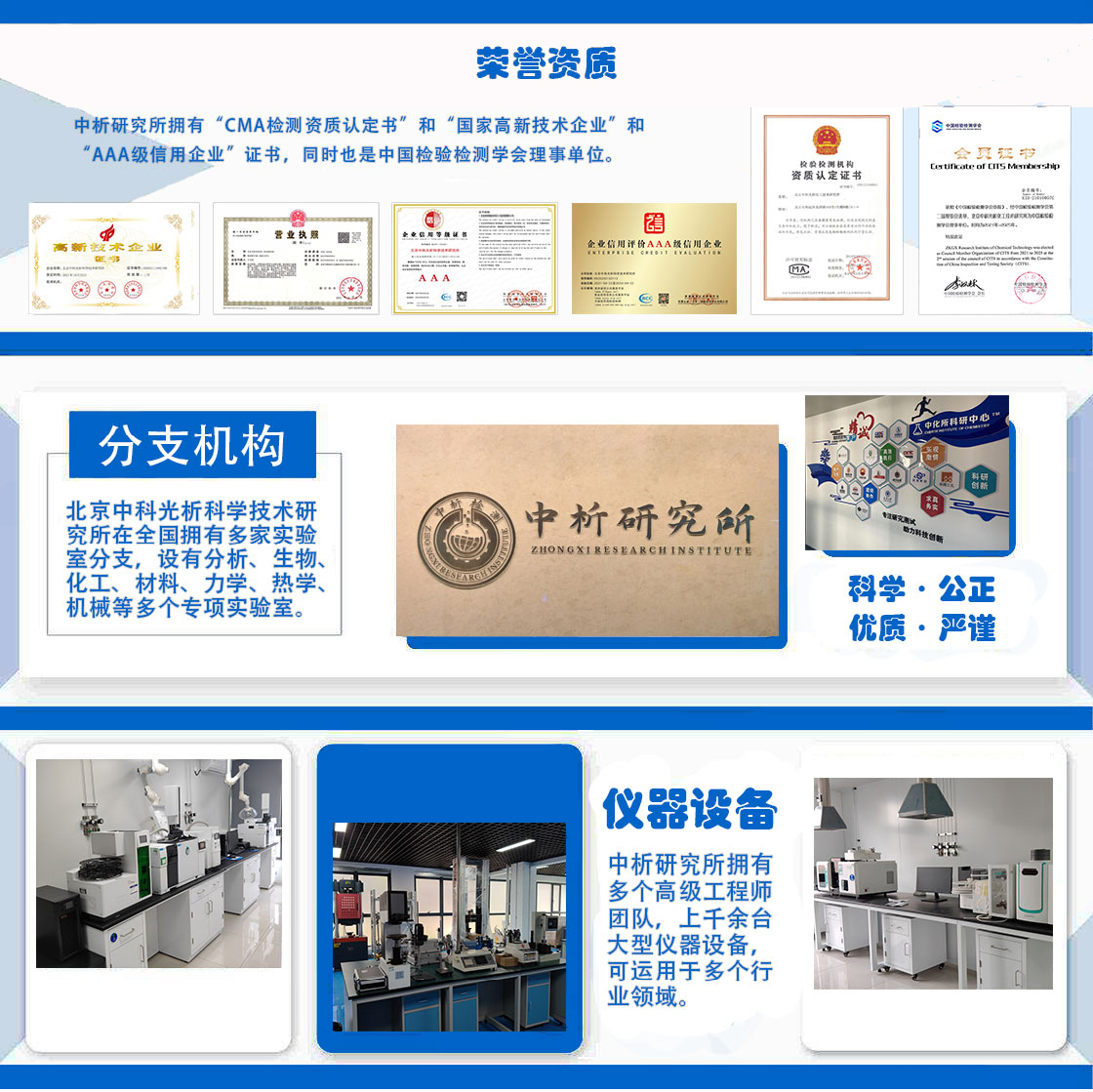
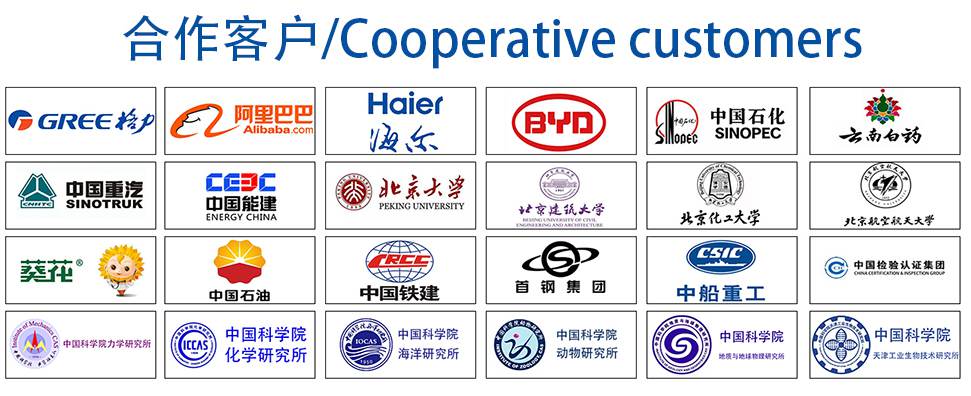