内燃机硼铸铁单体铸造活塞环检测技术解析
在内燃机核心部件中,硼铸铁单体铸造活塞环作为关键摩擦副组件,其性能直接影响发动机的密封性、燃油效率和服役寿命。随着内燃机向高功率密度、低排放方向发展的趋势,对活塞环的材质性能要求日益严苛。硼铸铁材料因其优异的耐磨性、高温稳定性和成本优势被广泛应用,而精确的检测体系是确保产品质量的核心保障。
一、化学成分检测
通过光谱分析仪对硼(B)、碳(C)、硅(Si)等元素进行定量检测,重点控制硼含量在0.02%-0.08%区间。采用电感耦合等离子体原子发射光谱法(ICP-OES)可精确测定微量元素的配比,确保材料具备标准规定的石墨形态和基体组织结构。
二、力学性能检测
使用万能材料试验机进行三点弯曲试验,评估抗弯强度(≥450MPa)和弹性模量指标。配合洛氏硬度计(HRB标尺)测量表面硬度值(90-110HRB),通过金相显微镜观察珠光体含量(≥95%)和石墨形态分布,验证材料在高温工况下的抗蠕变能力。
三、几何精度检测
应用三坐标测量仪对活塞环自由开口间隙、闭口间隙进行三维扫描,公差需控制在±0.05mm内。使用激光轮廓仪检测环体径向厚度波动,配合圆度仪验证环周真圆度(≤0.02mm),确保与缸套的配合密封性。
四、表面质量检测
采用电子显微镜(SEM)观察摩擦表面镀层(如铬基复合镀层)的致密性和厚度均匀性(20-50μm)。通过表面粗糙度仪测量Ra值(0.2-0.4μm),结合超声波探伤仪检测内部缩孔、夹杂等铸造缺陷,保证产品服役可靠性。
五、台架验证测试
在模拟工况试验台上进行500小时耐久测试,监测漏气量(<5L/min)、机油消耗率(<0.3g/kWh)等关键参数。通过振动频谱分析评估环-缸套系统的动态适配性,为产品优化提供数据支撑。
现行检测体系需严格参照GB/T 1149.1-2020《内燃机活塞环》及JB/T 6016《硼铸铁活塞环技术条件》等标准执行。随着智能检测技术的发展,基于机器视觉的在线检测系统和数字孪生仿真技术正逐步应用于活塞环的智能制造体系,推动产品质量控制迈向更高精度层级。
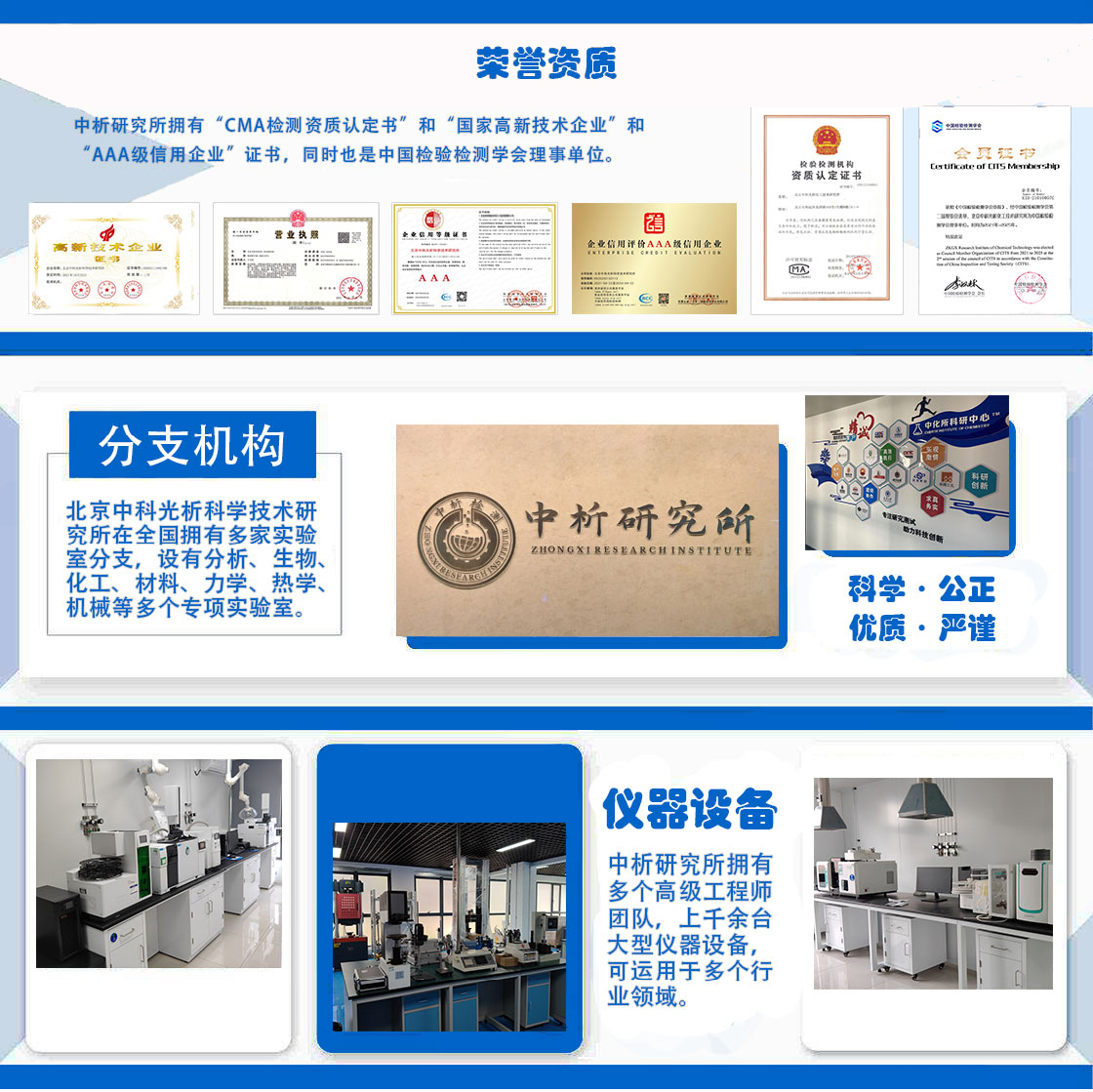
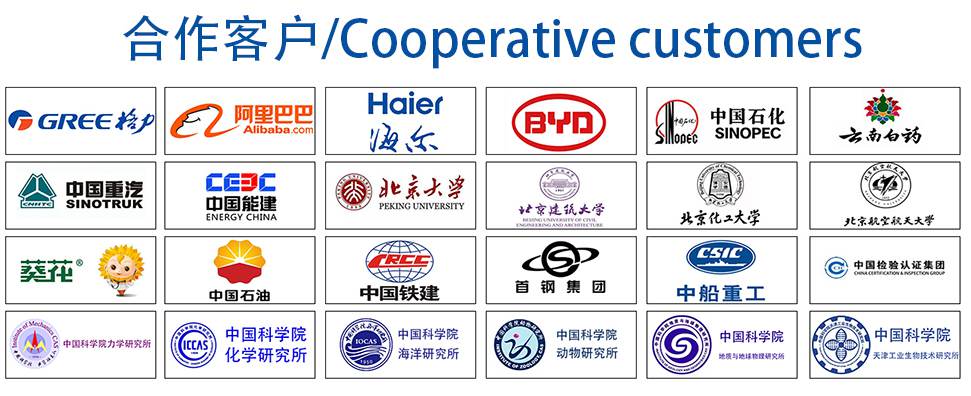