链轮检测项目全解析:保障传动系统稳定运行的关键
链轮作为机械传动系统的核心部件,其质量直接影响设备运转效率和使用寿命。根据《GB/T 15388-2020 传动用精密滚子链和套筒链链轮》标准要求,专业链轮检测需包含尺寸精度、材料性能、表面质量等20余项关键指标。本文将从检测项目、执行标准到行业应用场景,系统解析链轮品质管控的完整流程。
核心检测项目分类
1. 几何尺寸检测
使用三坐标测量仪检测齿顶圆直径、齿根圆直径的尺寸公差(±0.05mm),通过齿轮啮合试验台验证节距累积误差(≤0.1mm/m)。重点检测轮齿渐开线齿形偏差,确保与链条的啮合精度。
2. 材料性能测试
通过光谱分析仪验证材料成分(常用20CrMnTi/45#钢),洛氏硬度计检测齿面硬度(HRC58-62),金相显微镜观察渗碳层深度(0.8-1.2mm)。抗拉强度需≥850MPa,冲击功需≥45J。
3. 表面质量评估
粗糙度仪检测齿面Ra≤1.6μm,磁粉探伤排查表面裂纹缺陷,盐雾试验验证镀层耐腐蚀性(≥96h无红锈)。高精度链轮需进行齿面氮化处理,白亮层厚度控制在0.01-0.03mm。
齐全检测技术应用
采用三维激光扫描技术建立链轮数字孪生模型,通过ANSYS进行接触应力仿真分析。基于机器视觉的在线检测系统可实现每分钟15个链轮的节距自动化测量,测量精度达±3μm。德国KLINGELNBERG齿轮测量中心可同时检测齿向误差、齿廓偏差等12项参数。
行业应用标准差异
农机链轮需满足ISO606-B系列标准,重点检测抗冲击性能;汽车正时链轮执行TS16949体系,侧重尺寸稳定性;矿山机械链轮参照MT/T231标准,强化齿面耐磨指标。出口欧盟产品须通过CE认证的DIN8187标准检测。
质量控制关键点
检测数据应建立SPC统计过程控制图,CPK值需≥1.33。批量生产时实施首件三检制,过程抽检频率不低于5%。建议每500小时运行后进行齿厚磨损量检测,当磨损量超过原始尺寸8%时必须更换。
通过系统化的链轮检测体系,可有效预防断齿、跳链等故障。某变速箱企业实施全项检测后,链轮使用寿命从8000小时提升至12000小时,设备停机率下降37%。专业的检测方案已成为提升传动系统可靠性的重要保障。
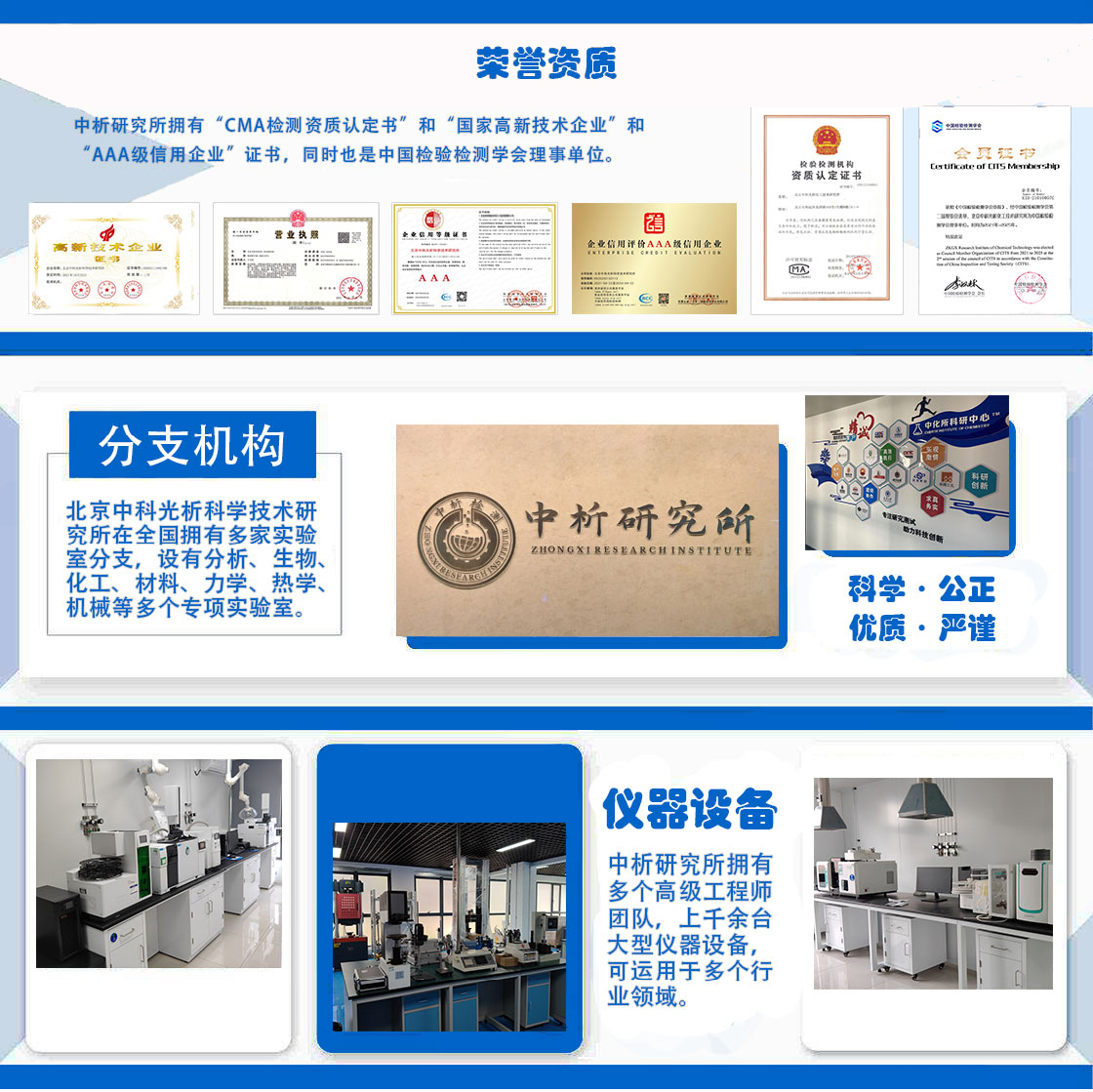
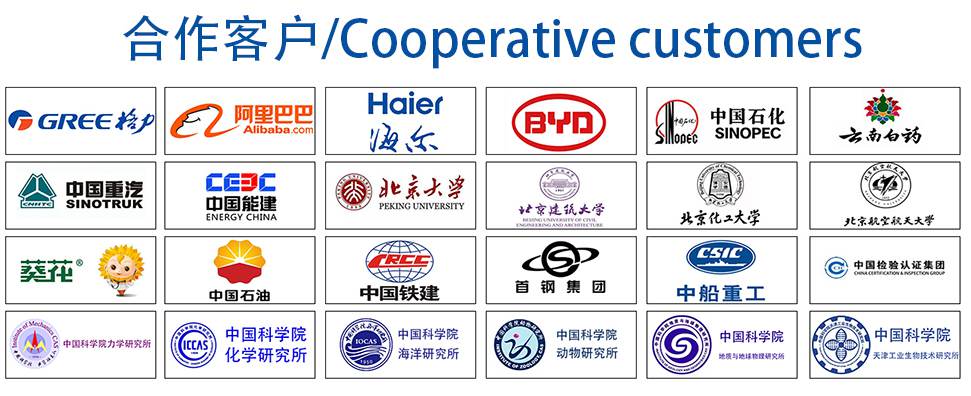