外观品质基本要求检测的重要性
外观品质基本要求检测是产品制造与质量控制的核心环节之一,直接影响消费者对产品的第一印象和使用体验。无论是工业设备、电子消费品,还是家具、纺织品等领域,外观缺陷都可能成为客户退货或投诉的主要原因。通过系统性检测,企业能够确保产品符合设计标准、行业规范及客户需求,同时降低返工率和成本浪费。检测内容通常涵盖颜色一致性、表面光洁度、尺寸精度、材质纹理、装配完整性等多个维度,旨在从视觉和触觉层面保证产品的整体品质。
主要检测项目及标准
1. 颜色与色泽检测
颜色一致性是外观品质的关键指标,需通过色差仪或标准色卡比对进行量化分析。检测内容包括主色偏差、光泽度均匀性及褪色情况,需符合行业标准(如ISO 105-J03)或客户指定色号范围。对于金属、塑料等材质,还需评估表面镀层或喷涂的色牢度。
2. 表面缺陷检测
包括划痕、凹坑、气泡、污渍、毛刺等可视缺陷的识别。采用目视检查结合光学显微镜或自动影像检测系统(AOI),依据GB/T 2828抽样标准判定缺陷等级。例如,电子产品外壳的划痕长度超过0.5mm即视为不合格。
3. 尺寸与形状公差检测
使用卡尺、投影仪或三维测量仪验证产品轮廓是否符合设计图纸要求。重点关注关键部位的尺寸偏差(如孔径、边距)、平面度及圆度误差,公差范围通常需控制在±0.1mm以内。
4. 材质与纹理评估
通过触感测试、显微观察或光谱分析,确认材料类型(如金属、塑料、玻璃)与纹理设计的一致性。例如,木纹贴面的产品需检测纹路清晰度与重复单元匹配度,避免出现接缝错位或图案断层。
5. 装配与结构完整性检测
检验部件间的配合间隙、对齐精度及紧固件安装状态。例如,手机屏幕与边框的间隙需均匀且≤0.2mm,螺丝无松动或漏装现象。振动测试或压力测试可辅助验证结构稳定性。
6. 标识与印刷质量检测
检查产品上的商标、标签、警示文字等印刷内容是否清晰完整。采用高分辨率扫描仪检测字体模糊、断线、错位等问题,确保符合《产品标识标注规定》等法规要求。
检测方法与技术趋势
传统检测依赖人工目视和接触式测量工具,而现代技术则逐步转向智能化。例如,基于机器视觉的自动化检测系统可实时分析产品图像,结合AI算法快速识别缺陷;3D扫描技术能生成高精度模型比对设计数据。此外,多光谱成像技术可同步捕捉颜色、纹理和材质信息,显著提升检测效率与准确性。
结论
外观品质基本要求检测需贯穿产品生产的全流程,结合标准化检测项目和齐全技术手段,企业可有效提升产品合格率与市场竞争力。未来随着物联网和AI技术的普及,实时在线检测与数据驱动的质量优化将成为行业发展趋势。
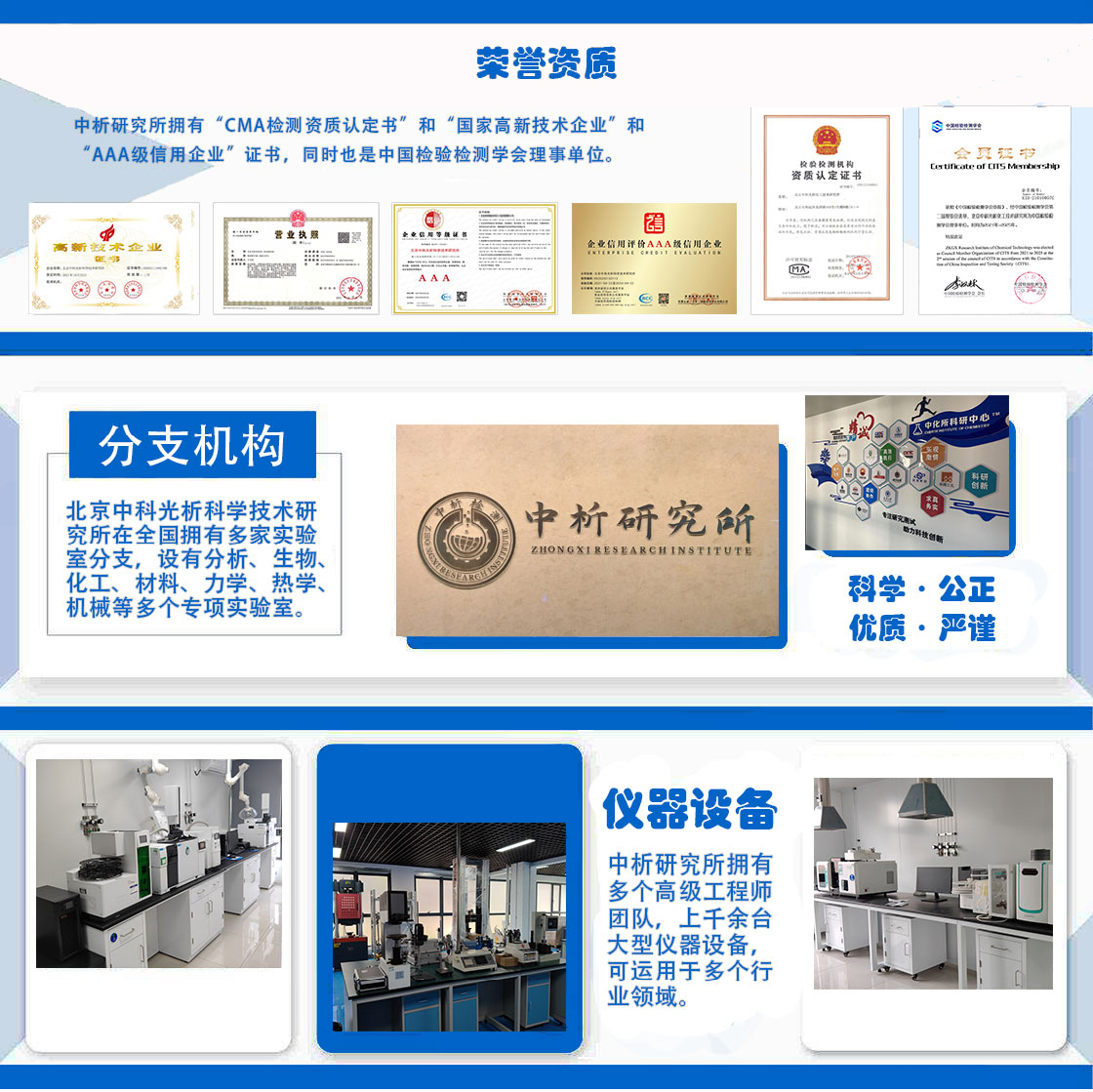
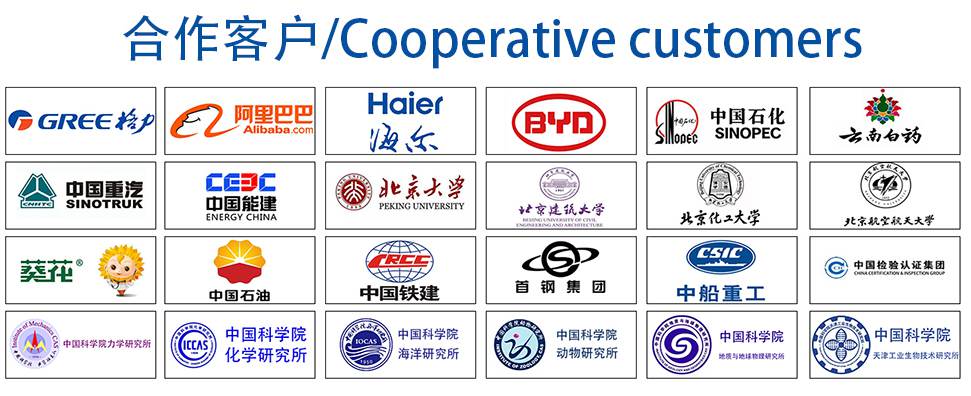