裁切生产线检测:保障效率与质量的核心环节
在现代制造业中,裁切生产线作为板材加工、纺织裁剪、包装材料分切等领域的核心装备,其运行精度与稳定性直接决定了产品合格率与生产成本。随着工业自动化水平的提升,裁切生产线已逐步实现高速化、智能化转型,但设备长期运行中易出现的刀具磨损、定位偏移、传动系统故障等问题,仍需通过系统化的检测流程进行预防性维护。针对裁切生产线的检测项目需覆盖机械结构、控制系统、安全防护及成品质量四大维度,通过多角度数据采集与对比分析,确保设备始终处于最佳工作状态,同时满足ISO 9001质量管理体系和行业安全标准要求。
一、机械部件精度检测
1. 刀具系统检测:使用激光测距仪与轮廓扫描仪对裁切刀具的刃口平整度、角度偏差及磨损量进行量化评估,配合扭矩传感器监测刀轴驱动电机的负载波动。
2. 传动机构校准:通过编码器反馈和光栅尺测量验证送料滚轮同步性,检测导轨直线度误差控制在±0.02mm/m以内,确保材料进给无偏移。
3. 定位系统验证:采用高精度CCD视觉系统对裁切位置的重复定位精度进行测试,要求连续作业100次后定位误差不超过±0.1mm。
二、自动化控制系统检测
1. PLC程序逻辑测试:模拟各类异常工况(如材料卡滞、气压不足)验证急停响应时间≤50ms,确保控制系统的故障自诊断功能正常运作。
2. 伺服电机性能分析:使用示波器采集伺服驱动器的电流波形,检测加减速过程中的过冲现象,优化PID参数以降低5%以上的能耗。
3. 人机界面(HMI)交互检测:检查参数设定权限分级管理、报警记录存储完整性及多语言界面切换功能。
三、安全防护装置专项检测
1. 光电安全栅灵敏度测试:利用标准测试棒验证保护区域触发响应时间≤15ms,确保人体任何部位进入危险区域前设备完全停止。
2. 紧急制动系统验证:通过突发断电实验检测刹车装置能否在0.5秒内使刀轴转速降至安全阈值以下。
3. 气压/液压系统监控:安装压力传感器实时监测执行机构的工作压力,设定动态报警阈值防止系统压力异常波动。
四、成品质量追溯性检测
1. 尺寸公差抽检:每批次随机抽取30件成品,采用三坐标测量机检测裁切长度、角度及切口垂直度是否符合图纸要求。
2. 表面质量评估:通过工业显微镜观察裁切边缘毛刺高度≤0.05mm,使用色差仪检测材料表面无压痕或划伤。
3. 数据追溯系统验证:核对MES系统中记录的设备参数、操作人员及检测结果的时间戳关联准确性。
五、综合效能评估与优化
建立包含OEE(设备综合效率)、MTBF(平均故障间隔时间)、能耗指数等18项指标的评估体系,通过振动分析仪与热成像仪识别潜在故障点。建议每季度执行一次全面检测,并结合历史数据预测刀具更换周期,实现从被动维修向预测性维护的转型。经系统化检测优化的裁切生产线,可提升15%-20%的产能利用率,同时将废品率控制在0.3%以下。
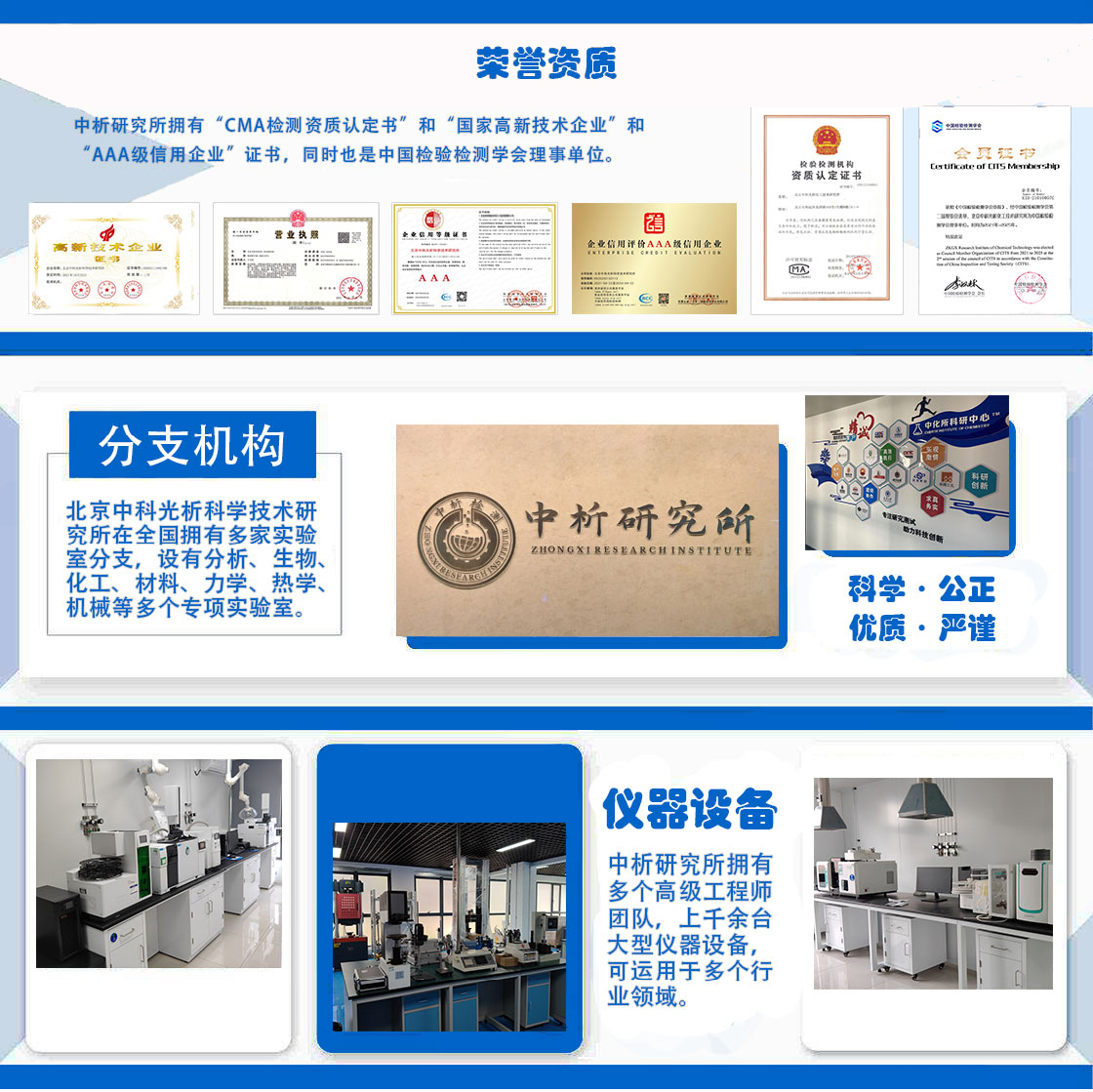
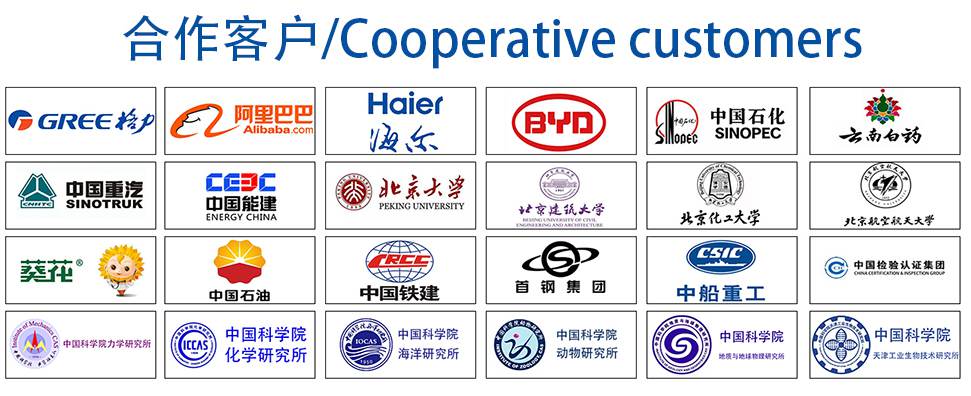