聚酯(PET)瓶装饮料超洁净灌装生产线检测的重要性
随着消费者对食品安全和品质要求的提升,聚酯(PET)瓶装饮料的生产过程逐渐向高洁净、高精度方向升级。超洁净灌装生产线通过齐全的无菌控制技术,确保饮料在灌装环节避免微生物污染和异物混入,从而延长产品保质期并保障消费者健康。然而,生产线的稳定性和洁净度需要通过系统化检测来验证。针对PET瓶装饮料超洁净灌装生产线的检测,需覆盖设备性能、工艺参数、环境控制及成品质量等核心环节,通过多维度数据监控确保生产合规性。
关键检测项目及技术要点
1. 微生物控制效果检测
超洁净灌装的核心在于微生物防控。需定期对灌装区域进行沉降菌检测、浮游菌采样及表面微生物擦拭试验,评估空气净化系统(如HEPA过滤)的效能。同时,通过ATP荧光检测仪对灌装阀、瓶口接触部位进行实时生物膜监控,确保无菌环境符合GB 12695《饮料企业卫生规范》要求。
2. 异物与杂质检测
采用高精度视觉检测系统对空瓶内壁、灌装后液位及瓶盖密封性进行实时筛查,识别粒径≥0.3mm的可见异物。针对金属杂质,需在灌装线前后端配置金属探测仪,灵敏度需达到Fe≥1.0mm、SUS≥1.5mm的标准。此外,定期对生产线润滑系统进行油雾残留检测,防止机械磨损产生的微粒污染。
3. 密封性与耐压性测试
通过负压密封性试验机模拟运输过程中的压力变化,检测瓶盖与瓶口的密封强度,泄漏率需≤0.05%。同时,对PET瓶身进行爆破压力测试(通常≥0.6MPa),验证其在冷链或高温环境下的抗变形能力,避免因瓶体破损导致二次污染。
4. 灌装精度与温度控制
使用质量流量计监测灌装量的波动范围,确保单瓶灌装误差≤±1%。对于热灌装工艺(如茶饮料),需验证灌装温度维持体系(通常85-95℃)的稳定性,通过红外测温仪实时反馈数据,避免温度偏差导致微生物滋生或PET瓶变形。
5. 清洗消毒效果验证
采用化学残留检测(如过氧乙酸、臭氧浓度测试)与微生物挑战试验相结合的方式,评估CIP/SIP系统的清洗消毒效果。重点检测灌装阀、输送链板等关键部位的消毒剂残留量,确保符合GB 5749《生活饮用水卫生标准》限值。
智能化检测技术的应用趋势
现代超洁净灌装线正逐步集成物联网(IoT)和AI算法,例如通过在线浊度传感器实时监测灌装液透明度,或利用机器学习优化异物识别模型。同时,生产数据与MES系统联动,实现检测结果的自动追溯与风险预警,为PET瓶装饮料的“零缺陷”生产提供技术保障。
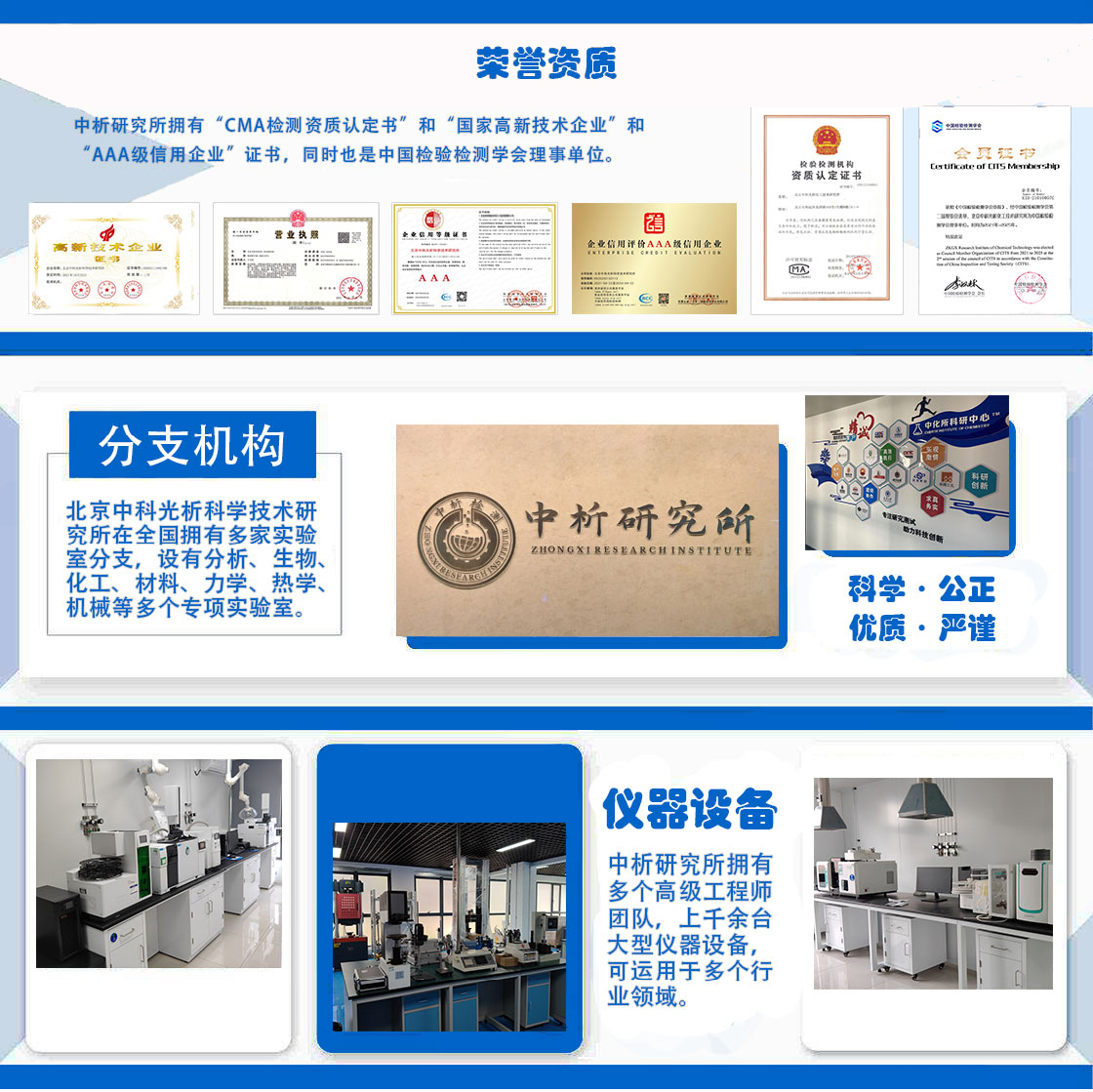
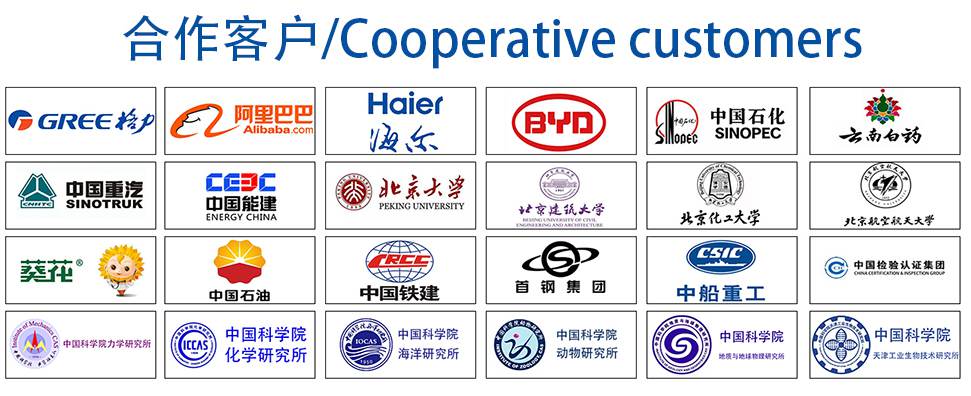