农林拖拉机和机械负载换档传动装置检测的重要性
农林拖拉机和机械作为现代农业生产的核心装备,其传动系统的可靠性直接关系到作业效率与安全性。负载换档传动装置作为动力传递的关键部件,承担着在不同工况下实现动力平顺切换、扭矩稳定输出的重要功能。随着农业机械化程度的提升和作业环境复杂性的增加,传动装置的检测已成为确保设备性能、延长使用寿命及预防故障的核心环节。通过系统化的检测,可精准评估换档机构的密封性、齿轮磨损状态、液压系统响应效率等关键指标,从而避免因传动失效导致的停机损失或安全事故。
负载换档传动装置核心检测项目
1. 变速箱总成性能测试
通过专用试验台模拟实际负载工况,检测输入/输出轴转速匹配性、扭矩传递效率及换档过程中的动力中断时间。需验证各档位切换时冲击值是否≤15m/s²(依据GB/T 1592标准),同时监测变速箱油温升幅是否在允许范围内(通常≤80℃)。
2. 动力换档离合器动态特性检测
采用高频压力传感器和位移传感器,测量离合器接合/分离的响应时间(标准要求≤0.3秒)、摩擦片滑磨功(≤150J)及油压稳定性(波动量需控制在±0.2MPa以内)。重点排查因油液污染导致的卡滞现象。
3. 齿轮啮合精度与磨损分析
使用三坐标测量仪对齿轮副的齿形误差、齿向偏差进行精密检测(精度需达DIN 5级),配合铁谱分析技术监测润滑油中的金属磨粒含量(Fe元素浓度预警值为120ppm)。对累计作业2000小时以上的设备需强制进行齿轮硬度复检。
4. 液压控制系统压力响应检测
在动态负载下验证主油路压力稳定性(目标值±5%)、换档电磁阀的启闭特性(动作滞后≤50ms)及蓄能器补偿能力(压力恢复时间<1.5秒)。同步检测液压油清洁度(NAS 1638 7级标准)。
5. 整机负载耐久性试验
依照ISO 5008标准进行500小时连续变载测试,监测传动装置在交变扭矩(30%-150%额定扭矩)下的振动烈度(RMS值≤4.5mm/s)、异响发生率及密封件渗漏情况。试验后需解体检查行星排轴承游隙变化量(允许值≤0.15mm)。
智能化检测技术的应用趋势
当前检测体系正加速向智能化转型,基于物联网的远程诊断平台可实时采集传动装置的温度、振动、压力等多维度数据,结合机器学习算法实现早期故障预警。例如,通过振动频谱分析可提前200小时预判轴承失效,准确率达92%以上。这种预测性维护模式将检测效率提升了40%,显著降低非计划性停机风险。
结论
完善的负载换档传动装置检测体系是保障农林机械可靠运行的技术基础。建议企业建立全生命周期检测档案,结合定期维护与状态监测,同时关注ISO/TC23国际标准的更新动态,确保检测方法始终与前沿技术发展同步。对于关键传动部件,推荐每500作业小时进行专项检测,及时更换超出磨损限值的零部件。
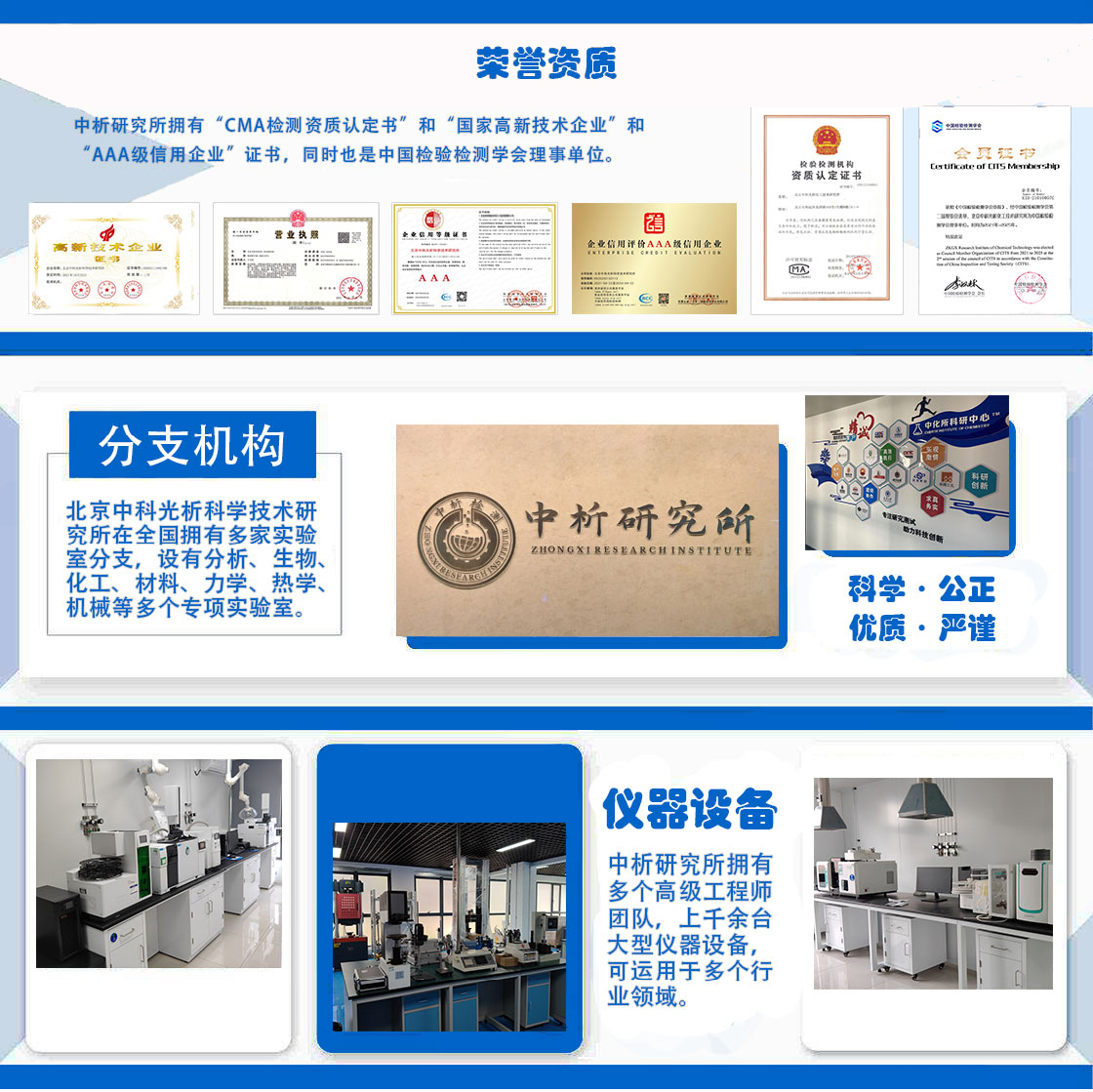
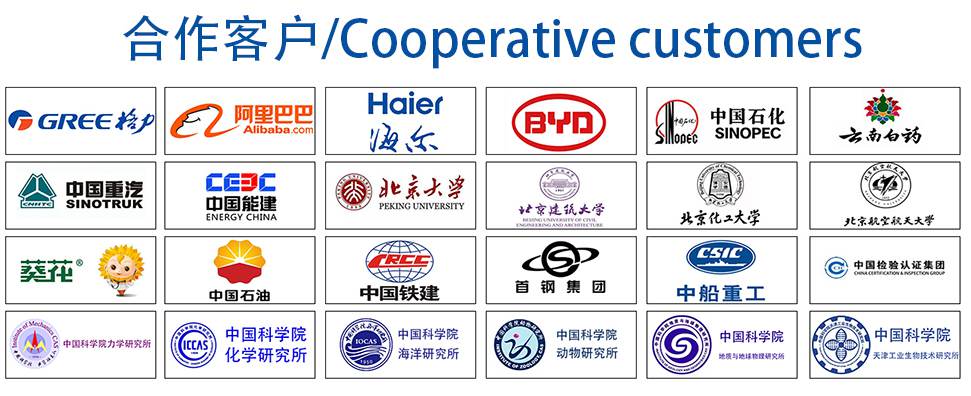