膜片压力表检测的重要性与核心内容
膜片压力表作为一种广泛应用于工业领域的精密测量仪表,主要用于监测气体、液体或蒸汽的压力参数。其核心部件是由弹性材料制成的膜片,通过形变反映压力变化并转换为指针读数。由于长期处于高温、腐蚀、振动等复杂工况中,膜片压力表的准确性、密封性和耐久性会逐渐下降,可能引发数据偏差甚至安全隐患。因此,定期开展专业检测是保障设备安全运行、延长仪表寿命的关键环节。检测项目需覆盖外观、性能、密封性、环境适应性等多维度,并依据国家计量标准(如JJG 52-2013)进行规范化操作。
膜片压力表检测项目详解
1. 外观及功能性检查
检测人员需确认压力表表盘刻度清晰无磨损,指针无变形或卡滞现象,玻璃罩完整无裂痕。同时检查膜片表面是否存在腐蚀、划痕或永久性形变,法兰连接部位是否紧固无松动。需模拟轻敲表壳动作,验证指针摆动是否灵敏且回零稳定,排除机械结构卡顿风险。
2. 示值误差与回程误差测试
使用标准压力源对仪表进行升压、降压循环测试,覆盖量程的0%、25%、50%、75%、100%五个关键点。记录各点示值与标准值的偏差,要求最大允许误差不超过精度等级标称值(如±1.6%)。回程误差需小于示值误差限的绝对值,确保膜片弹性恢复性能达标。
3. 密封性及耐压试验
通过液压试验台施加1.5倍额定压力并保持5分钟,观察膜片焊接处、接头部位是否渗漏。超压测试后需复检零点偏移量,偏移值应小于最大允许误差的50%。对于腐蚀性介质工况,还需额外进行膜片材质耐腐蚀性验证。
4. 环境适应性检测
包括温度循环测试(-20℃~+60℃)、振动试验(频率10-55Hz,振幅0.15mm)和防爆性能验证(针对Ex标志仪表)。测试后需重新校准示值,确保膜片材料热胀冷缩系数与补偿机构匹配性良好。
5. 数据记录与校准周期管理
检测结果需形成包含原始数据、误差曲线、密封测试影像的完整报告,并粘贴校准标签注明下次检测日期。根据使用环境严酷程度,常规工业场景建议每6-12个月进行一次强制检测,高危工况需缩短至3个月。
通过系统化的检测流程,可有效发现膜片疲劳老化、传动机构磨损等隐患,避免因压力表失效导致的工艺失控或安全事故。企业应建立检测档案数字化管理系统,实现仪表全生命周期质量追溯。
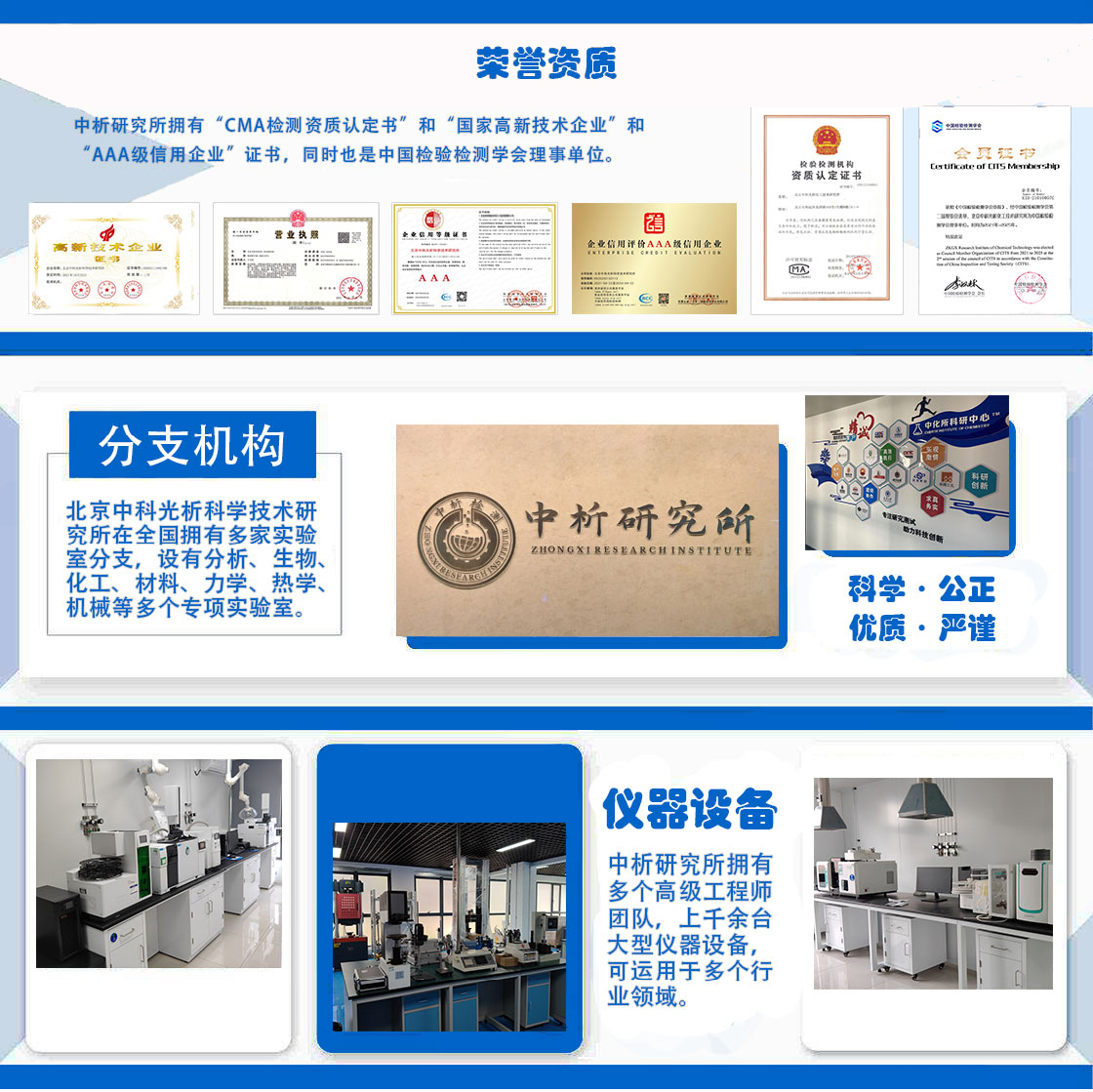
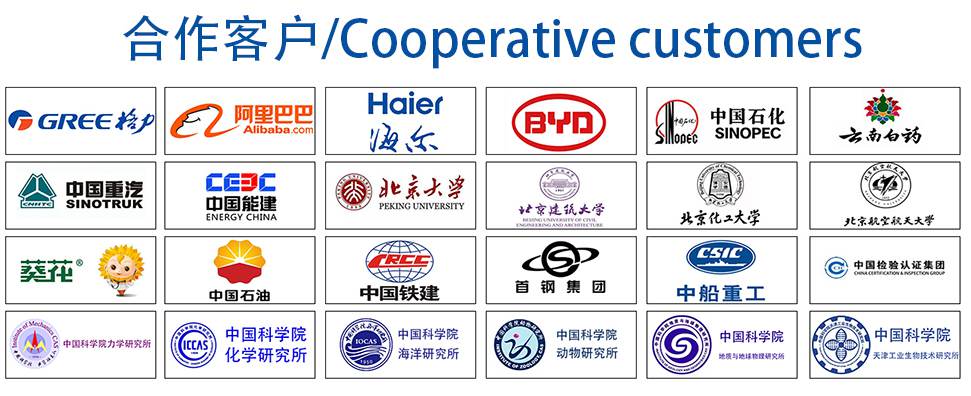