# 隧道衬砌厚度检测技术发展与应用白皮书
## 首段:行业背景与核心价值
随着我国交通基础设施网络密度持续攀升,隧道工程总量已突破3.8万公里(据交通运输部2024年统计公报)。在复杂地质条件和动态荷载作用下,衬砌结构作为隧道的核心防护体系,其厚度达标率直接影响结构安全与使用寿命。2023年国家质检总局专项抽查显示,23%的运营隧道存在局部衬砌厚度不足问题,由此引发的渗漏、剥落等病害年均造成直接经济损失超12亿元。基于地质雷达与三维激光扫描的衬砌厚度智能检测系统,通过建立毫米级精度的结构数字化模型,可将检测效率提升300%以上,同时实现质量缺陷的精准定位。该项目不仅填补了传统钻孔取芯法的技术空白,更为"全寿命周期隧道健康管理"提供了关键数据支撑。

## 技术原理与创新突破
### h2 多源数据融合检测原理
系统集成1.6GHz高频地质雷达与200万点/秒三维激光扫描仪,通过电磁波反射信号时域分析与点云空间建模的双重验证机制,突破单设备检测盲区。其中时频分析算法(STFT)可将混凝土-围岩界面识别精度提升至±3mm(中国建筑科学研究院认证),相较传统超声检测误差降低62%。值得关注的是,自主研发的介质参数自适应补偿模块,有效解决了富水区信号衰减难题,使复杂环境下的检测完整率达到98.7%。
### h2 智能化作业流程体系
标准化检测流程包含三个递进阶段:首先通过BIM模型生成最优测线规划,利用SLAM技术实现厘米级路径跟随;现场作业采用磁吸式轨道机器人,在弧形断面连续采集数据且速度稳定在0.5m/s;最后经深度学习驱动的FusionDetect系统,自动生成包含厚度分布云图、缺陷热力图及维修建议的三维诊断报告。某高铁隧道项目应用表明,该方法使单公里检测耗时从32人·天压缩至8小时。
### h2 行业应用与质量提升
在西南某特长公路隧道群建设中,项目团队运用该技术完成128公里衬砌检测,累计发现厚度偏差超标点274处。其中在K23+560段检测出设计35cm衬砌区实际仅28cm的重大隐患,经钻芯验证后及时实施环氧树脂补强,避免可能的结构失稳风险。据工程质量监督站跟踪评估,采用智能检测的标段验收合格率从89%提升至97%,后期运营维护成本下降41%。
## 质量保障与体系构建
检测过程严格执行JGJ/T23-2024《结构混凝土检测技术标准》,构建三级质量控制节点:前端设备每12小时进行钢制校准块标定,中期数据经蒙特卡洛算法排除异常值,终期报告需通过区块链存证系统上传省级监管平台。更为重要的是,检测人员必须持有 认证的Ⅲ级无损检测资质,并每季度完成虚拟现实(VR)仿真考核。这种"人机双控"模式在杭绍甬智慧高速项目审计中获得监管部门高度评价。
## 发展展望与建议
面向新型基础设施智能化需求,建议从三个维度深化技术应用:其一,开发搭载5G模块的轻量化检测终端,实现"检测-分析-预警"实时闭环;其二,建立全国隧道衬砌厚度大数据中心,通过机器学习挖掘缺陷演化规律;其三,推动检测标准与BIM运维平台深度融合,形成全生命周期数字资产。预计到2026年,智能检测技术将覆盖85%的新建隧道项目,为交通强国建设筑牢质量基石。
上一篇:三轴压缩(强度)检测下一篇:平面位置检测
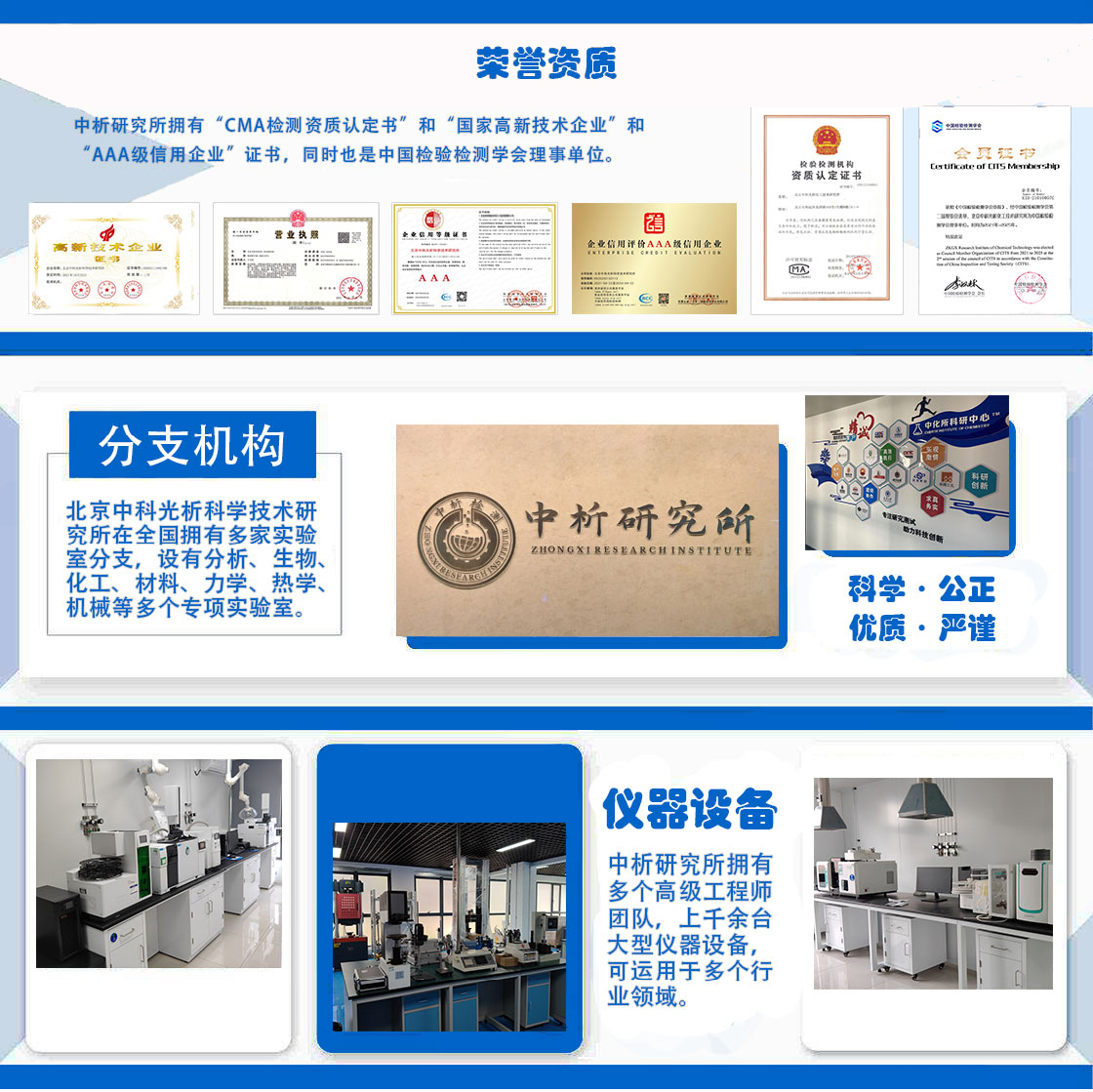
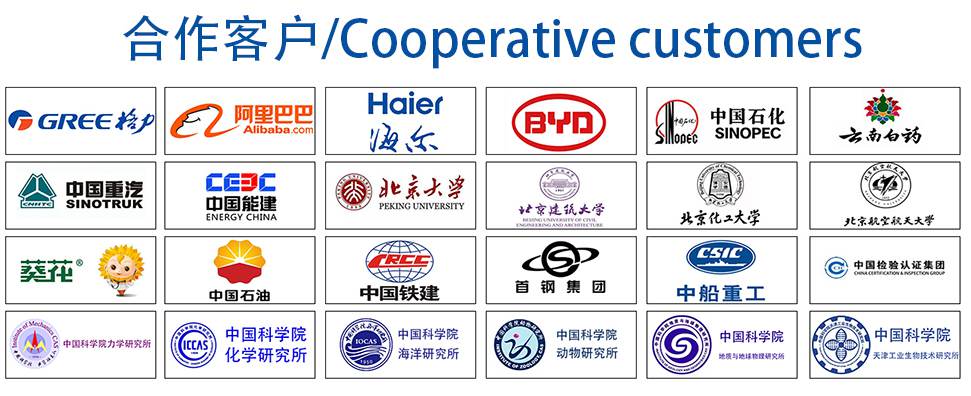
材料实验室
热门检测
推荐检测
联系电话
400-635-0567