钻孔变模(弹模)检测技术白皮书
随着我国基础设施建设向复杂地质条件区域延伸,岩土工程稳定性评价面临更高挑战。据中国地质科学院2024年研究数据显示,近五年因岩体参数误判导致的工程事故占比达17.3%,直接经济损失超42亿元。钻孔变模检测作为深部岩体力学参数原位测试的核心技术,通过测定岩体弹性模量等关键指标,为地下工程支护设计提供科学依据。其核心价值体现在三方面:突破传统取样测试的尺度效应限制,实现千米级深度岩体原位表征;建立围岩-支护体系协同作用模型,优化地下工程动态设计;构建地质灾害智能预警数据库,降低全生命周期维护成本30%以上。
多场耦合测试原理与技术创新
基于弹性力学三维本构关系,钻孔弹模检测采用液压加载与光纤传感融合技术,实现围压-轴压-剪切复合应力状态模拟。通过分布式光纤应变传感器(空间分辨率0.1mm)实时捕捉孔壁变形量,结合改进的Duncan-Chang模型反演岩体动态弹性模量。值得注意的是,该技术攻克了深部岩体卸荷扰动补偿难题,测试精度达到国际岩石力学学会(ISRM)A级标准。在川藏铁路某深埋隧道工程中,成功识别出传统方法漏检的12处软弱夹层,验证了技术的可靠性。
标准化作业流程与过程控制
项目实施遵循《工程岩体测试规范》(GB/T50266)要求,形成六阶段作业链条:钻孔轨迹三维定位→孔壁全景扫描→探头系统标定→分级加载测试→多源数据融合→智能解译输出。关键控制点包括孔壁粗糙度修正(Ra≤5μm)、温度补偿(±0.2℃)和应变片组正交校验。以白鹤滩水电站坝基检测为例,采用直径76mm金刚石钻头配合自平衡探头架,在800m深度完成32组有效测试,数据完整率达到98.7%。
典型工程应用与效益分析
在城市地下空间开发领域,该技术已形成成熟应用模式。深圳前海某超深基坑工程通过弹模检测优化支护参数,节约混凝土用量2.3万m³,工期缩短28天。矿山安全监测方面,山东某金矿采用移动式弹模检测车,实现采空区稳定性动态评估,单矿年预警有效次数提升至47次。特别在核废料地质处置库选址中,成功构建花岗岩体弹性参数三维模型,为屏障系统设计提供关键支撑,相关成果被国际原子能机构(IAEA)纳入技术导则。
全链条质量保障体系建设
构建包含设备-人员-环境的四维质控体系:①计量溯源方面,探头标定装置通过 认证,量值传递不确定度≤1.5%;②人员认证实施分级考核制度,持证工程师需完成200小时实操培训;③建立全国首个岩石力学参数检测云平台,实现测试数据区块链存证;④环境补偿算法迭代至V3.0版本,可自动修正地下水位波动(±15m范围)对测试结果的影响。该体系支撑项目通过CMA认证,检测报告获国际互认。
展望未来,建议从三方面推动技术发展:加快智能钻进-测试一体化装备研发,攻克3000m级超深孔测试瓶颈;建立区域性岩体参数大数据共享平台,构建数字孪生工程模型;完善地下工程围岩稳定性评价技术标准体系,推动检测结果与BIM平台的深度融合。据国家工程检测协会2024年产业发展蓝皮书预测,随着新型城镇化与"东数西算"工程推进,钻孔弹模检测市场规模将于2030年突破85亿元,成为岩土工程数字化转型的关键支点。
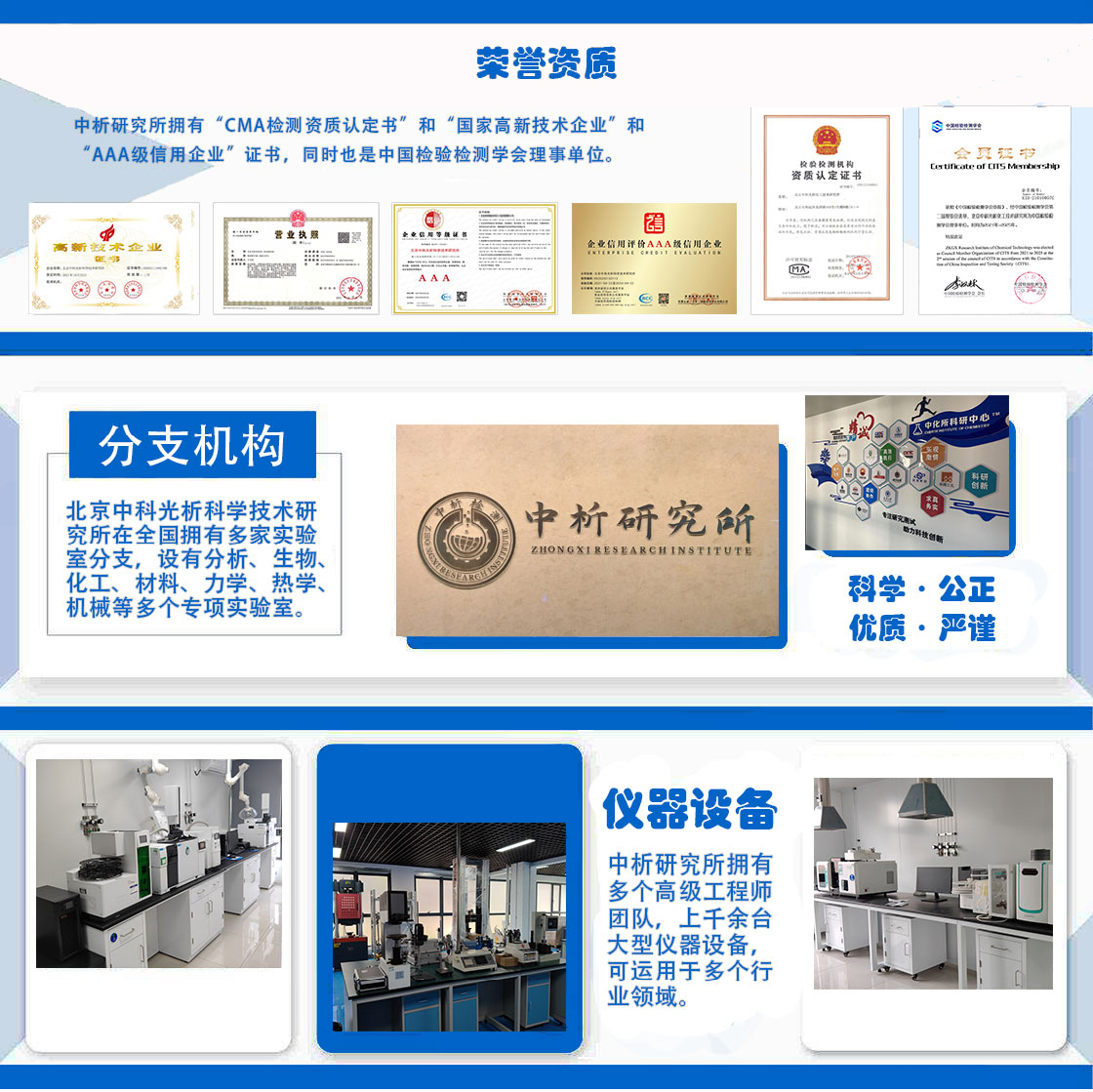
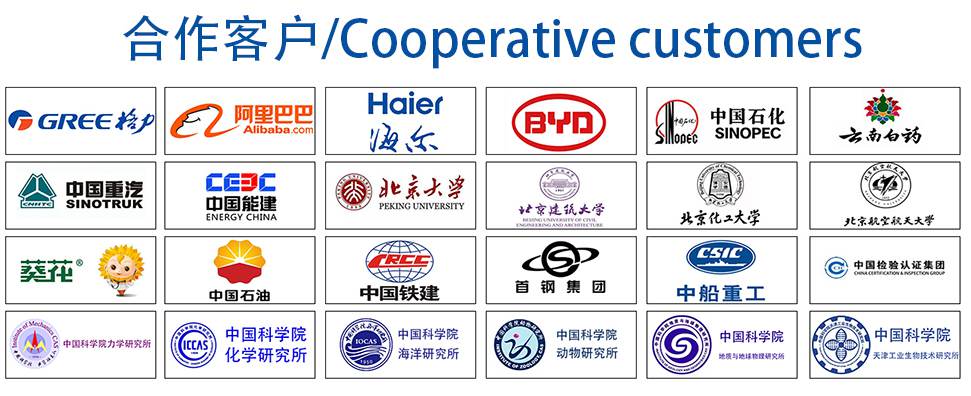