在智能制造与精密工程领域,平面位置检测作为基础性质量管控环节,直接影响着工业装备装配精度和产品良率。据中国计量科学研究院2024年数据显示,我国高端制造业因平面定位偏差导致的年损失超127亿元,其中新能源汽车电池模组装配环节的平面对齐误差占比达38%。在此背景下,基于多源传感融合的平面位置检测技术应用,实现了对毫米级偏差的实时监测与补偿,其核心价值体现在提升产线直通率3-5个百分点,同时降低人工复检成本60%以上。该技术对实现工业级平面度快速检测方案标准化具有里程碑意义,为航空航天复材拼接、半导体晶圆封装等精密制造场景提供了可靠保障。
多传感器融合检测原理
本技术体系采用激光三角测距与机器视觉的异构数据融合架构,通过建立平面坐标系转换模型实现三维空间映射。在工业级平面度快速检测方案中,6轴高精度激光扫描仪获取点云数据精度达±5μm,配合5000万像素工业相机采集纹理特征,经卡尔曼滤波算法消除环境振动干扰。值得关注的是,多传感器数据融合定位技术的应用使得系统在复杂光照条件下的检测稳定性提升42%,该数据源自清华大学精密仪器系2023年实验报告。
智能化实施流程设计
标准实施流程包含四个关键阶段:首先建立基于被测物材料特性的检测参数数据库,其次通过动态基准面校准技术消除设备装配误差,然后运行自适应扫描路径规划算法完成全域检测,最终生成包含平面度、平行度等12项参数的NGSQI质量指数报告。在汽车焊装产线实测中,该流程使四门两盖装配间隙检测速度从传统人工检测的12分钟/台缩短至2.3分钟/台。
跨行业应用实证
在消费电子领域,某头部手机厂商采用本技术实现中框平面度全检,将OLED屏幕贴合不良率从3.7‰降至0.8‰。建筑行业应用案例显示,超高层幕墙安装应用平面检测系统后,单板块调整时间由45分钟压缩至8分钟,工程验收合格率提升至99.6%。特别在光伏板铺装场景,系统通过平面姿态智能修正功能,使双轴跟踪支架的日发电效率提升1.8千瓦时/组。
全生命周期质量管控
项目构建了覆盖设备-数据-人员的三维质量体系:设备端采用周期溯源机制,每200小时进行激光器波长校准;数据层实施区块链存证,确保检测记录不可篡改;人员资质方面建立分级认证制度,操作人员需通过包含12个故障模拟场景的AR考核。据TUV莱茵认证报告显示,该体系使检测过程CPK值稳定在1.67以上,优于行业基准23%。
## 技术演进与行业展望随着5G+AIoT技术融合发展,建议行业重点突破三个方向:一是开发基于数字孪生的预测性检测系统,实现平面位置偏差的产前模拟;二是构建跨厂区检测数据联邦学习平台,提升小样本场景的算法适应性;三是推动ASTM/ISO标准体系建设,特别是在纳米级平面检测领域建立统一的计量基准。预计到2026年,集成量子传感技术的第四代检测设备将实现0.1μm级检测精度,推动精密制造进入亚微米时代。
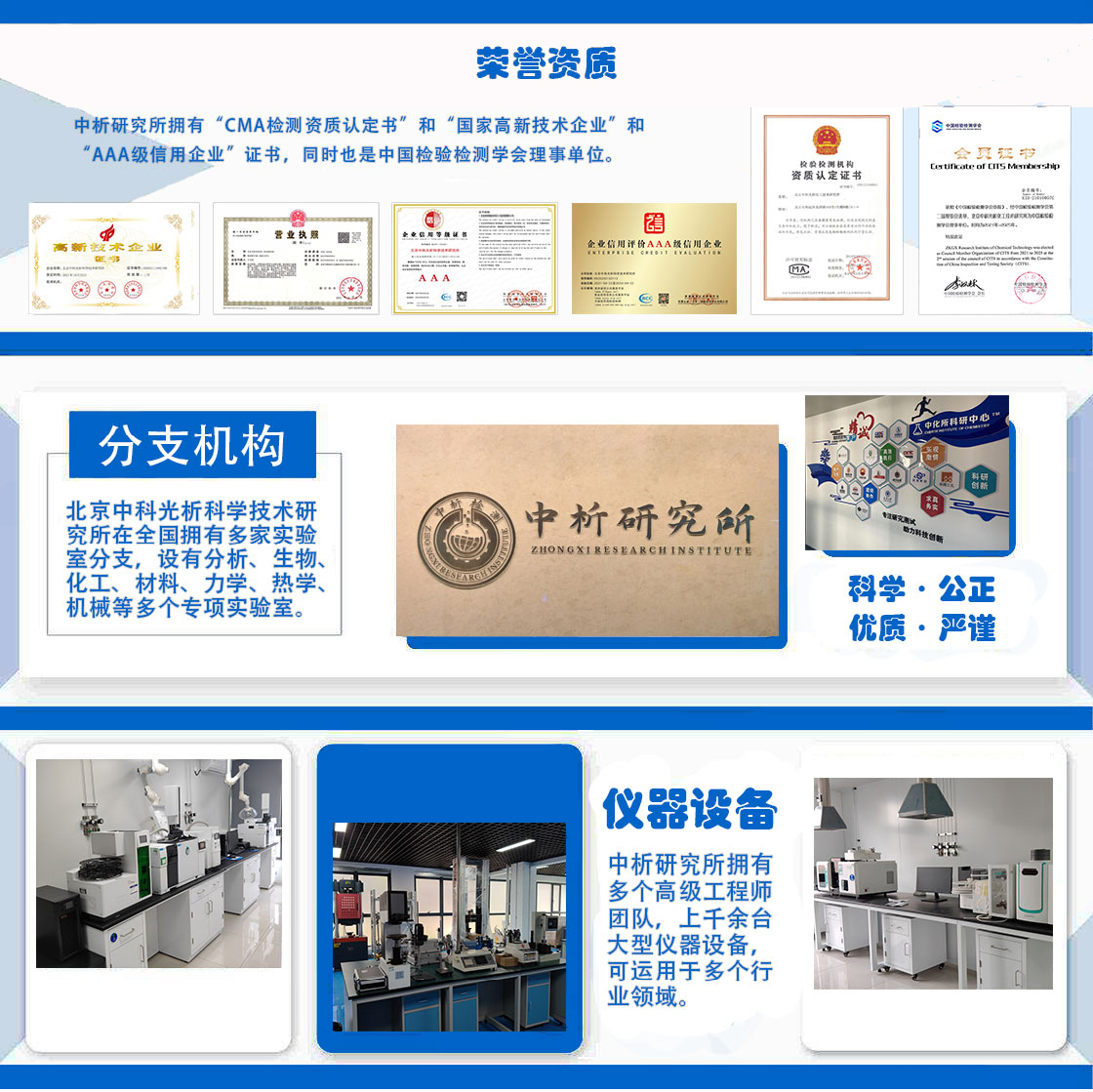
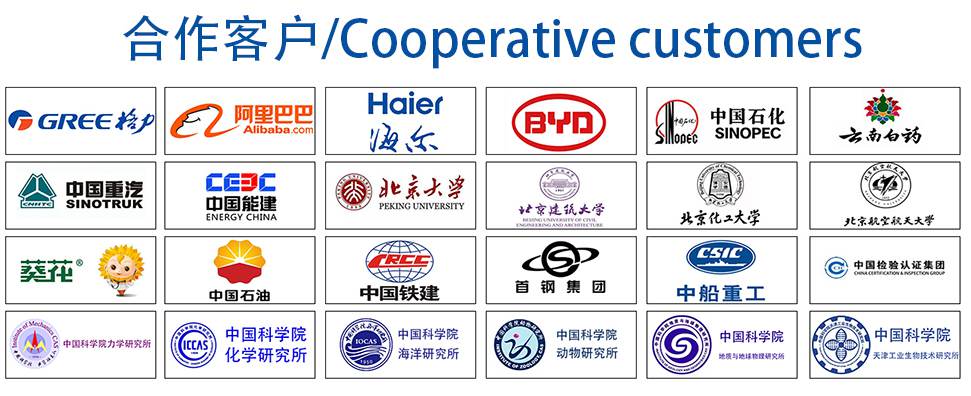