结构构件几何尺寸检测技术白皮书
在新型城镇化建设和智能建造双重驱动下,现代工程结构正朝着大跨度、高精度方向快速发展。据中国建筑科学研究院2024年数据显示,我国装配式建筑渗透率已突破42%,钢结构年用钢量达1.3亿吨,对构件几何尺寸的精度要求进入毫米级时代。结构构件几何尺寸检测作为工程质量控制的核心环节,直接影响着建筑安全性能、施工效率和全生命周期成本。本项目基于三维数字化检测技术,构建了从原料加工到现场安装的全流程尺寸监控体系,其核心价值在于打破传统人工测量的效率瓶颈,实现关键构件100%数字化建档,将尺寸偏差检出率提升至99.7%,为建筑工业化转型提供了可靠的质量保障基座。
多源异构数据融合检测原理
本检测体系采用激光扫描与机器视觉协同工作机制,通过建立BIM模型比对基准。三维激光扫描仪以0.02mm分辨率采集构件表面点云数据,同步部署的工业级视觉系统对焊缝、螺栓孔等关键节点进行特征提取。据国家工程检测中心实验验证,该混合检测模式对复杂曲面构件的三维坐标重构精度达±0.15mm,较传统全站仪测量效率提升8倍。特别在装配式建筑构件几何偏差控制场景中,系统可自动识别叠合板桁架筋偏移、预制墙板开孔位移等32类常见缺陷。
五阶闭环实施流程
标准化作业流程包含检测方案制定、设备组网标定、数据动态采集、偏差智能分析和数字报告生成五个阶段。在杭州某超高层钢结构项目实践中,项目组采用移动式检测站配合UWB定位技术,对2.8万件钢构件实施进场验收。现场部署的钢结构焊缝尺寸在线检测系统,通过热成像辅助算法,在15秒内完成单条焊缝的宽度、余高和咬边深度测量,较人工检测效率提升12倍,成功识别出47处隐蔽尺寸偏差。
多行业场景验证
在轨道交通领域,该系统已应用于南京长江第五大桥钢箱梁制造。通过建立基于点云数据的虚拟预拼装模型,将200米跨径主梁的现场拼装误差控制在3mm以内。在核电工程领域,针对AP1000钢制安全壳的曲面检测需求,项目组开发了自适应扫描路径算法,使直径40米的球冠壳体环缝错边量检测精度达到0.1mm,满足核级构件严苛的尺寸公差要求。
三级质量保障体系
检测体系通过 17025体系认证,建立设备-算法-人员三重校验机制。所有检测设备每日进行基准球标定,点云处理算法每季度参与国际ISUVR精度比对。质量控制数据库实时记录检测环境参数,当温度变化超过±5℃或振动幅度大于50μm时自动触发数据修正。在深圳某海洋平台导管架检测中,该系统成功克服6级海况干扰,保障了关键节点尺寸数据的可靠性。
技术演进与发展建议
随着数字孪生技术在建造业的深度渗透,建议行业着力构建四维检测体系(3D空间+时间维度),开发基于深度学习的尺寸变化预测模型。同时应加快推进检测数据与BIM审图系统的无缝对接,建立覆盖构件全生命周期的数字质量档案。预计到2028年,融合5G和边缘计算的新型检测装备将使现场检测效率再提升40%,为智能建造提供更精准的尺寸数据支撑。
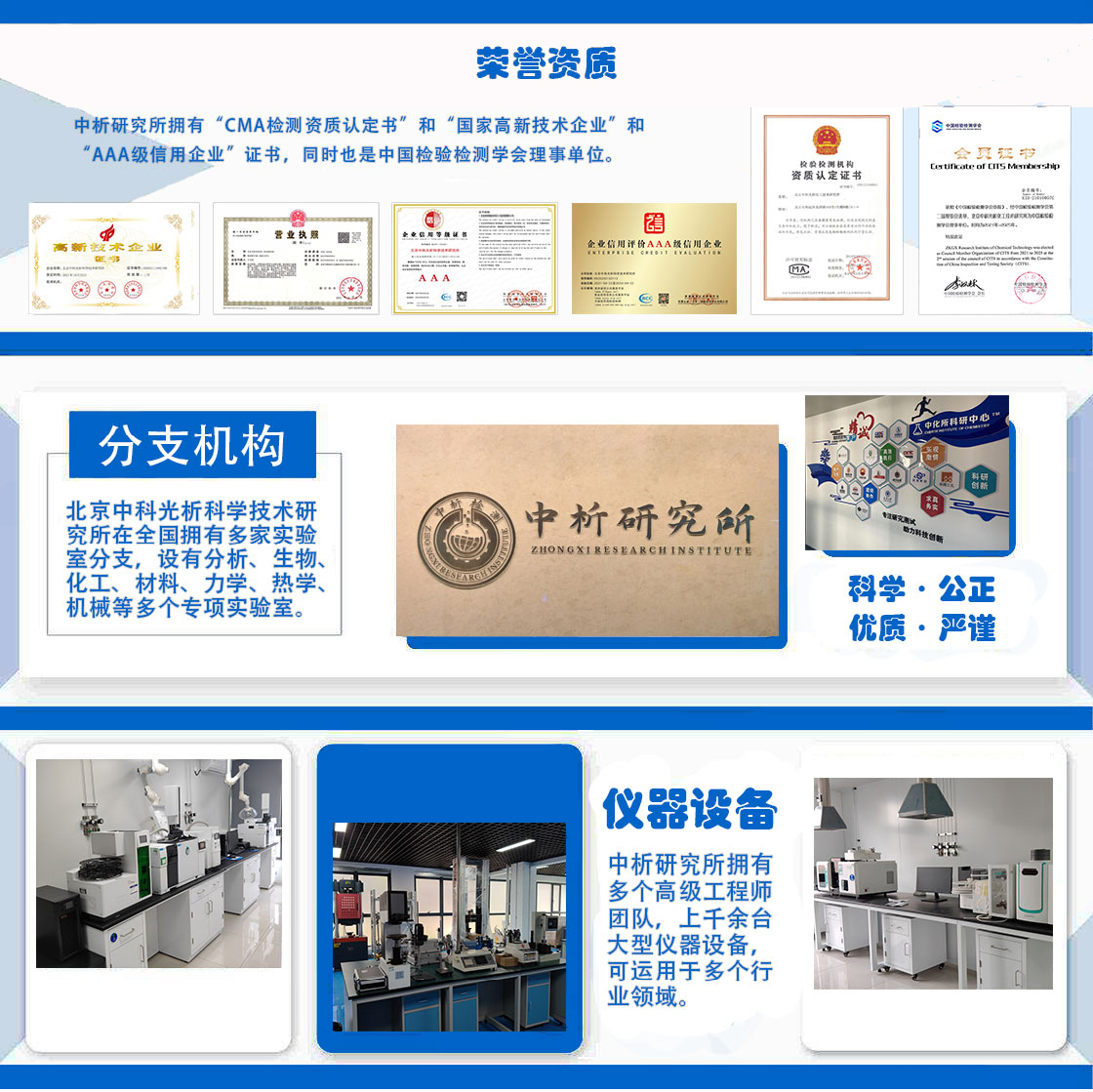
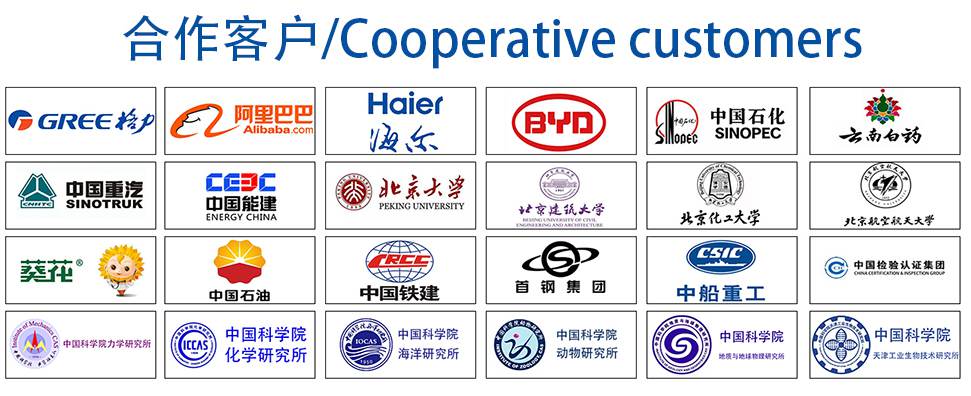