E/E/PE安全相关系统检测的核心内容与实施要点
在工业自动化、轨道交通、汽车电子等领域,E/E/PE(电气/电子/可编程电子)安全相关系统是保障功能安全的核心载体。随着IEC 61508、ISO 26262等安全标准的广泛应用,针对这类系统的专业化检测已成为确保设备可靠性和人员安全的关键环节。检测过程需覆盖系统全生命周期,从硬件设计、软件逻辑到环境适应性进行全面验证,同时需满足功能安全完整性等级(SIL/ASIL)的严格要求。
一、检测标准与法规框架
E/E/PE系统检测须严格遵循国际标准体系:IEC 61508作为基础安全标准,定义了SIL等级划分及验证方法;ISO 13849针对机械安全控制系统提出PL等级要求;汽车行业则采用ISO 26262标准进行ASIL等级评估。检测机构需依据产品应用领域选择对应标准,同时结合国家强制性认证(如CCC)和行业特殊规范,构建多维度的检测框架。
二、硬件安全性能检测
硬件检测重点包括元器件故障率分析(FMEDA)、电磁兼容性(EMC)测试和耐久性验证:使用故障注入技术模拟元器件失效场景,验证硬件冗余机制的有效性;通过辐射抗扰度、静电放电等EMC测试确保系统在复杂电磁环境中的稳定性;加速寿命试验则评估硬件在极端温度、振动条件下的可靠性表现。
三、软件安全验证方法
软件验证涵盖V模型开发过程的全方位审查:通过静态代码分析工具检查编码规范性,采用MISRA-C等标准约束编程实践;设计结构化测试用例实现需求覆盖率和代码覆盖率双重验证;形式化方法则用于证明关键算法逻辑的正确性。对于AI驱动的智能系统,还需增加神经网络鲁棒性测试和决策可解释性验证。
四、系统集成与功能安全评估
在系统级验证阶段,需执行闭环测试验证安全功能响应:包括安全状态转换测试、故障诊断覆盖率验证、紧急停机响应时间测量等。使用HIL(硬件在环)测试平台模拟真实工况,结合故障树分析(FTA)和事件树分析(ETA)量化系统风险。最终由认证机构依据检测数据出具功能安全评估报告。
五、环境适应性与现场验证
完成实验室检测后,需进行现场安装验证:检查机械防护装置的联锁有效性,验证安全通信协议(如PROFIsafe)的数据完整性,评估多系统协同工作的时序一致性。特殊应用场景还需补充防爆认证(ATEX)、防水防尘(IP等级)等专项测试,确保系统在目标环境中的长期可靠性。
六、持续安全监测与维护
通过部署预测性维护系统,实时监测关键参数变化趋势:采集继电器触点磨损数据、记录电子元件老化特征、分析软件运行日志异常。建立安全审计机制,定期更新失效模式数据库,确保系统在整个生命周期内持续满足安全完整性要求。对于软件系统,还需建立安全补丁管理流程和版本追溯体系。
随着智能制造和自动驾驶技术的快速发展,E/E/PE安全检测正从传统的结果验证转向过程管控。检测机构需构建涵盖需求工程、安全架构设计、验证测试的完整服务体系,同时加强AI赋能的自动化测试工具开发,以应对日益复杂的安全系统检测挑战。
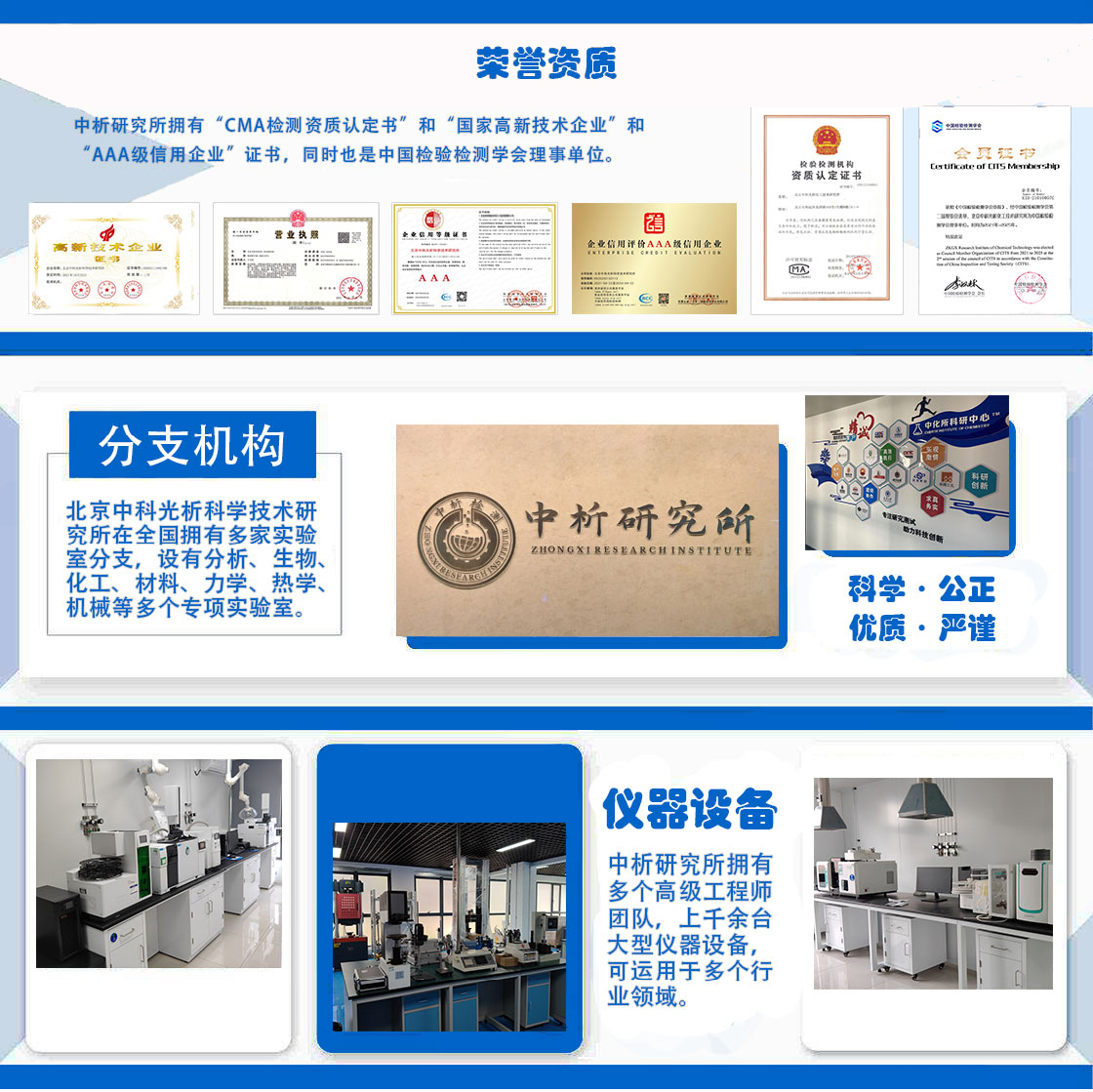
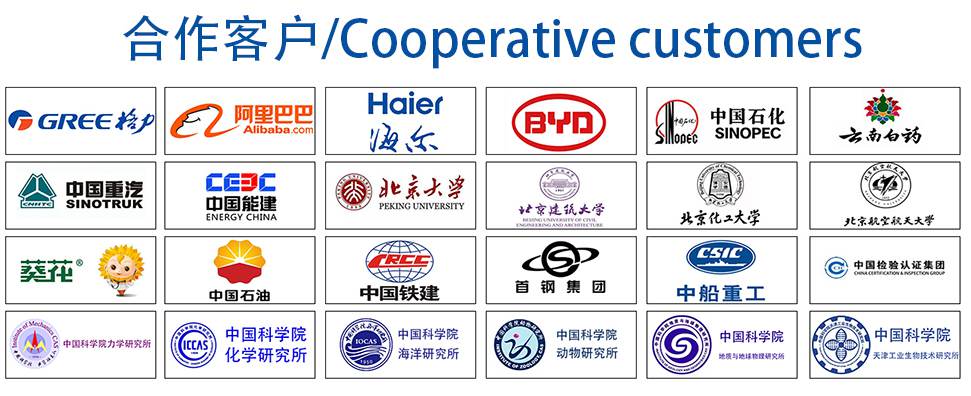