钢构件防腐层检测的重要性与核心内容
在工业建筑、桥梁工程、石油化工设备及船舶制造等领域,钢构件的防腐层是保障结构耐久性和安全性的关键屏障。由于钢材长期暴露于潮湿、盐雾、化学腐蚀等恶劣环境中,若防腐层出现缺陷或失效,将导致钢材锈蚀、强度下降甚至结构崩塌等严重后果。因此,钢构件防腐层的检测不仅是质量验收的必要环节,更是设备全生命周期维护的核心内容。通过系统化的检测项目,可精准评估涂层性能、识别潜在风险,并为修复方案提供科学依据,从而延长钢构件的服役寿命。
防腐层检测的核心项目与方法
1. 涂层厚度检测
利用磁性测厚仪或超声波测厚仪对防腐层进行多点测量,确保厚度符合设计要求(如环氧涂层≥200μm)。依据ISO 19840或ASTM D7091标准,记录平均值与极差值,重点关注焊缝、边缘等易薄区域。
2. 附着力强度测试
采用划格法(ASTM D3359)或拉开法(ISO 4624)评估涂层与基材的结合力。划格法通过刀片在涂层表面形成网格,观察剥离情况;拉开法则通过液压装置定量测定剥离强度,要求≥5MPa为合格。
3. 涂层破损与连续性检查
使用电火花检漏仪(适用于埋地管道)或湿海绵法(导电基材)检测针孔、裂缝等缺陷。检测电压根据涂层厚度设定(如1kV/mm),配合目视检查确认锈斑、鼓包等表观异常。
特殊性能评估与辅助检测技术
4. 耐腐蚀性能验证
通过盐雾试验(ASTM B117)、循环腐蚀试验(ISO 11997)模拟极端环境,评估涂层抗氯离子渗透能力。实验室加速老化测试可预测涂层在湿热、紫外线等复合因素下的耐久性。
5. 表面处理质量追溯
检测喷砂处理后的钢材表面清洁度(SSPC VIS 1标准)和锚纹深度(ISO 8503),使用比对样板或轮廓仪验证粗糙度(通常要求Ry=50-100μm),确保涂层与基材的机械咬合效果。
6. 涂层均匀性与色差分析
采用光泽度计(ASTM D523)和色差仪(ASTM D2244)量化涂装质量,控制光泽度偏差≤10%、色差值ΔE≤1.5,避免因施工工艺问题导致局部防护性能下降。
检测数据管理与工程应用建议
现代检测技术已结合数字化手段,如配备GPS定位的智能测厚仪可生成三维涂层厚度云图,而AI图像识别系统可自动标记破损区域。建议建立检测数据库,关联环境参数与涂层退化速率模型,实现预测性维护。对于海洋平台、化工厂等高风险场景,需每季度开展重点区域检测,普通建筑钢结构则建议每年至少进行一次全面评估。
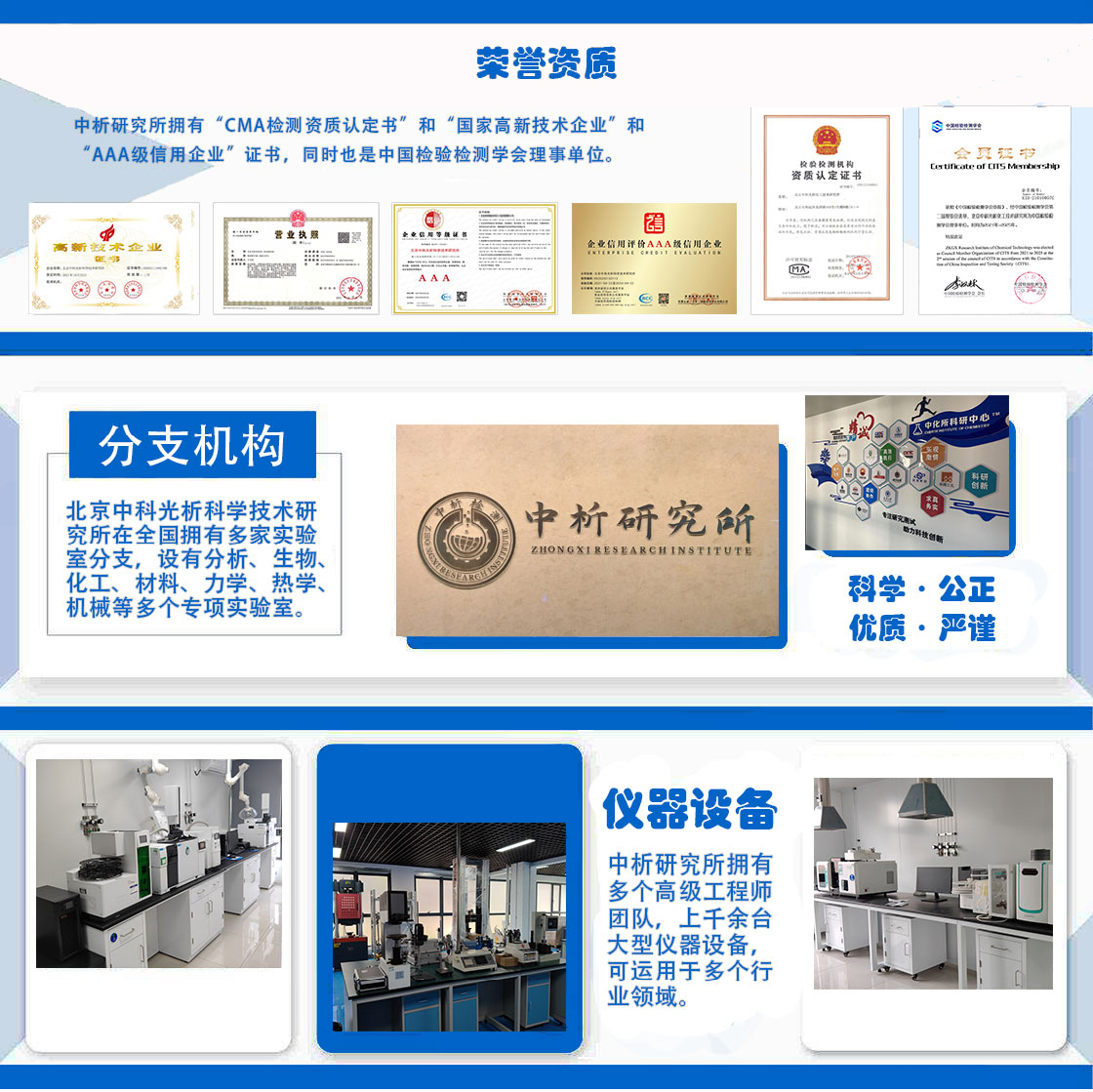
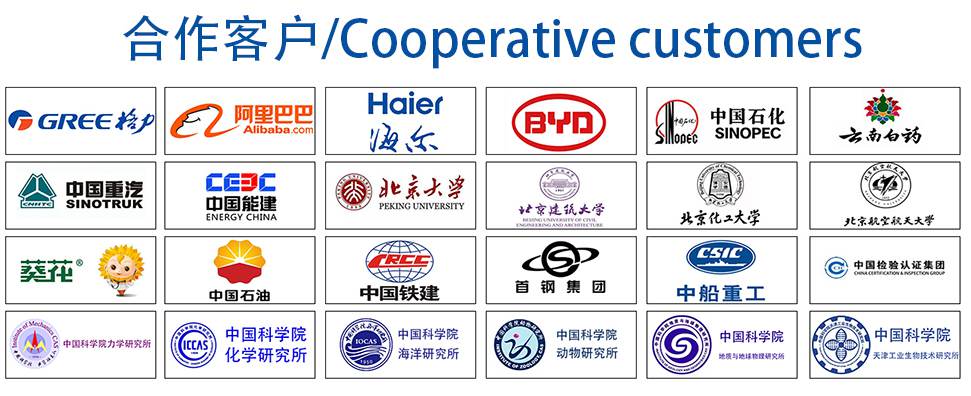