部件检查与安全检查检测的重要性
在工业制造、设备运维及安全管理领域,部件检查和安全检查检测是确保系统稳定运行的核心环节。随着现代设备复杂性的提升,任何微小部件的失效或安全漏洞都可能引发连锁反应,导致生产效率下降、设备损坏甚至人员伤亡。据统计,60%以上的工业事故源于未及时发现的部件缺陷或安全疏漏。因此,通过科学规范的检测流程对关键部件进行定期检查,并系统性排查安全隐患,已成为企业生产管理中的强制性要求。这些检测不仅覆盖机械性能、材料老化、结构完整性等物理指标,还需结合智能化工具对电气系统、数据安全等新兴风险进行动态监控。
部件检查的核心检测项目
1. 外观与结构检测:通过目视检查、三维扫描或探伤技术(如X射线、超声波)识别部件表面裂纹、腐蚀或变形,评估其结构承载能力。例如在航空发动机叶片检测中,需精确测量微米级缺损。
2. 材料性能测试:利用硬度计、金相分析仪等设备检测材料硬度、抗拉强度及微观组织变化,判断是否因疲劳或环境侵蚀导致性能退化。
3. 功能性验证:模拟实际工况对部件进行负载测试,包括动态压力测试(如液压系统阀门)、温度循环测试(如电子元件)等,确保其在极端条件下的可靠性。
安全检查检测的关键领域
1. 机械安全防护检测:重点检查设备急停装置、防护罩联动机制、运动部件隔离措施是否符合ISO 13849等安全标准,防止机械伤害事故发生。
2. 电气系统安全检查:运用绝缘电阻测试仪、接地连续性检测仪等工具,排查线路老化、漏电风险,同时验证防爆设备在易燃环境中的合规性。
3. 环境安全监测:针对有毒气体泄漏、粉尘爆炸等风险,部署传感器网络实时监控作业环境,并定期校准检测设备的灵敏度。
智能化检测技术的应用趋势
当前,基于AI的预测性维护系统正逐步替代传统人工检测。例如,利用振动传感器结合机器学习算法,可提前3-6个月预警轴承磨损;红外热成像技术能非接触式识别电气过载热点。这些技术不仅提升了检测效率,更通过数据建模实现了风险的可视化管理。未来,数字孪生技术与物联网的结合,将进一步推动部件检查和安全检查向全生命周期智能监控转型。
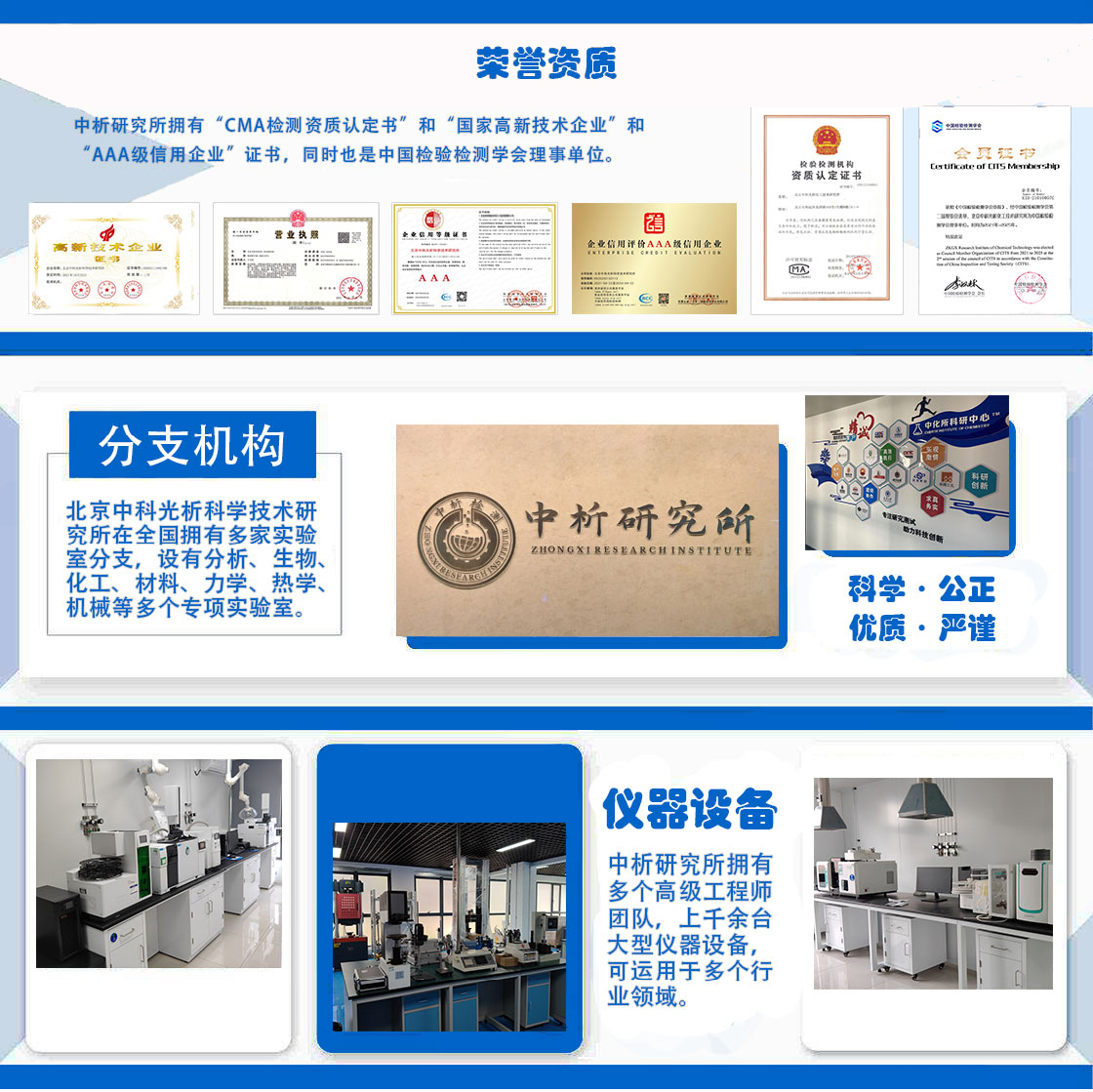
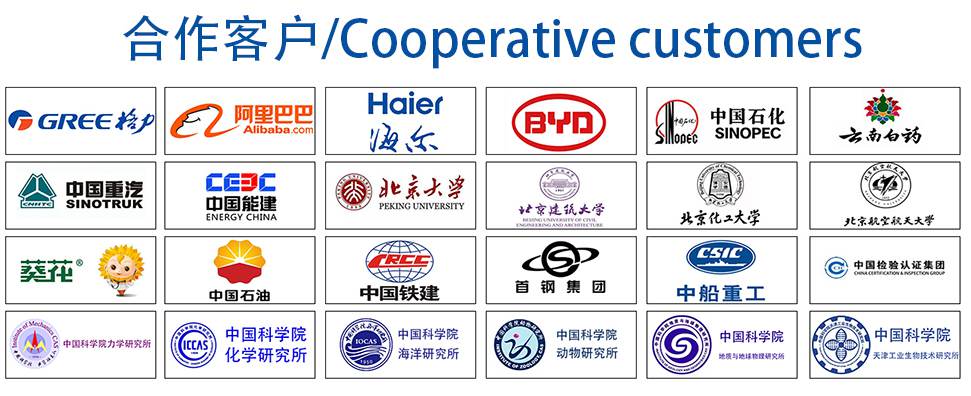