冶金焦炭检测的重要性与技术要点
冶金焦炭作为高炉冶炼的核心原料,承担着还原剂、发热剂和料柱骨架支撑的三重作用。其质量直接影响高炉运行效率、铁水品质及能源消耗水平,因此构建科学的焦炭质量检测体系是钢铁企业提质增效的重要保障。根据《冶金焦炭质量标准》(GB/T 1996-2017)要求,现代冶金焦炭检测涵盖物理性能、化学组成及工艺特性三大类共12项关键指标,形成从原料入厂到生产监控的全周期质量管控网络。
核心检测项目体系
1. 工业分析检测
采用GB/T 2001《焦炭工业分析方法》进行四组分测定:固定碳(FC, Fixed Carbon)反映有效还原能力,要求≥85%;灰分(A, Ash)采用高温灼烧法,控制≤12.5%;挥发分(V, Volatile Matter)通过隔绝空气加热测定,要求≤1.8%;全硫(St, Total Sulfur)采用库仑滴定法,严控≤0.7%。其中硫分超标将导致钢材热脆性风险上升。
2. 机械强度检测
转鼓试验(GB/T 2006)系统评估抗碎强度M40(≥82%)和耐磨强度M10(≤7.5%),模拟高炉料柱中焦炭承受的机械应力。微米级气孔结构分析(ISO 7404-3)配合显微硬度测试,可预测焦炭抗热冲击性能。
3. 反应性检测
CO2反应性(CRI)与反应后强度(CSR)构成关键控制对指标(GB/T 4000-2017)。优质焦炭要求CRI≤28%、CSR≥65%,确保在高温还原环境中既能参与反应又保持结构完整。激光导热仪可同步测定800℃下热导率(≥0.25 W/m·K)。
4. 粒度分布检测
执行GB/T 2005标准进行筛分试验,要求25-75mm粒度级占比≥75%,超限粒级需进行破碎改性。三维激光粒度仪可实现动态粒度监控,结合DEM离散元模拟优化筛分工艺。
检测技术创新趋势
随着智能化检测设备的普及,在线中子活化分析(PGNAA)技术已实现焦炭成分的实时监测,X射线衍射(XRD)可解析焦炭显微结构,太赫兹时域光谱(THz-TDS)技术为焦炭气孔率检测提供了非接触式解决方案。这些齐全技术正推动冶金焦炭检测向数字化、智能化方向快速发展。
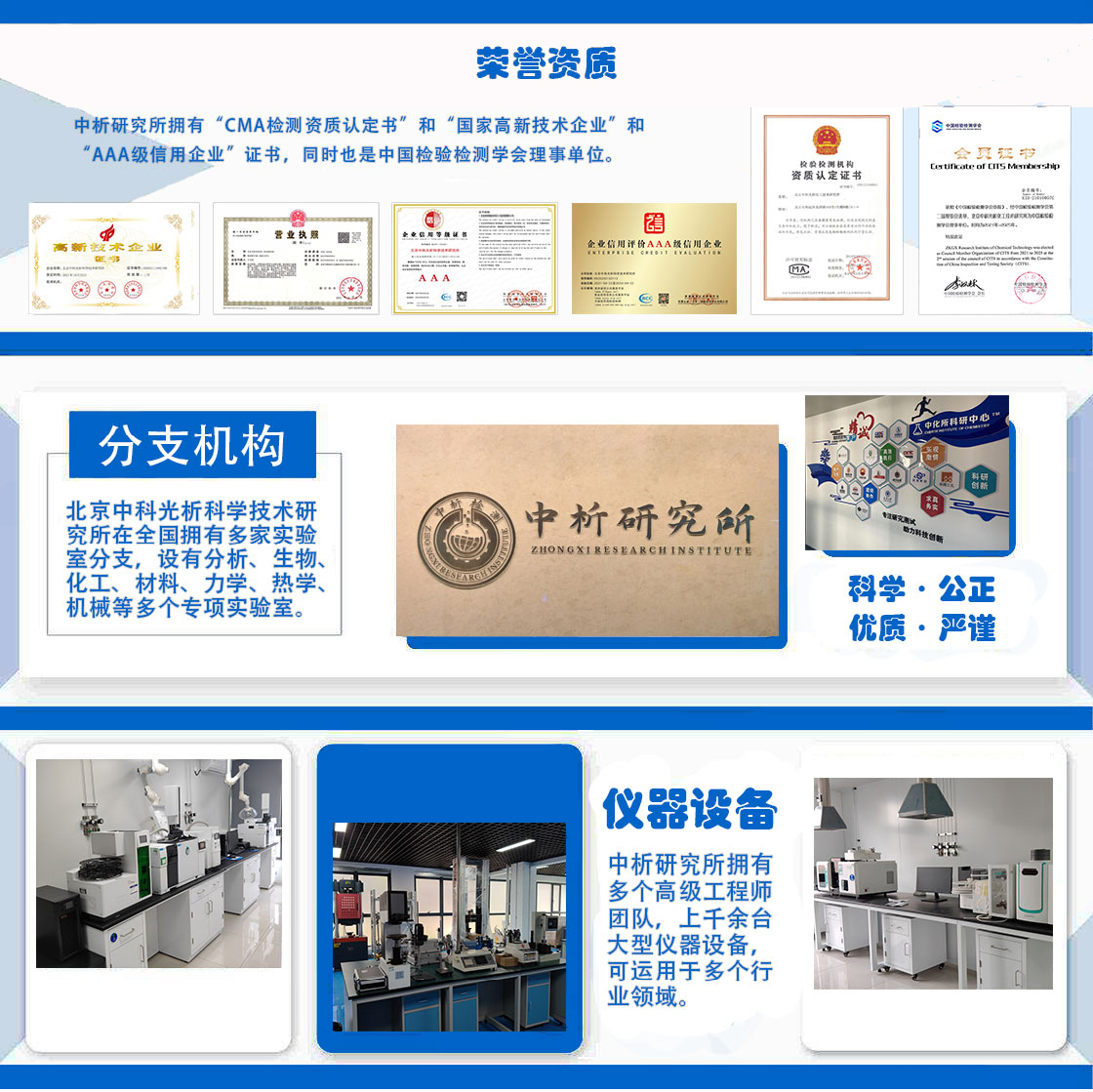
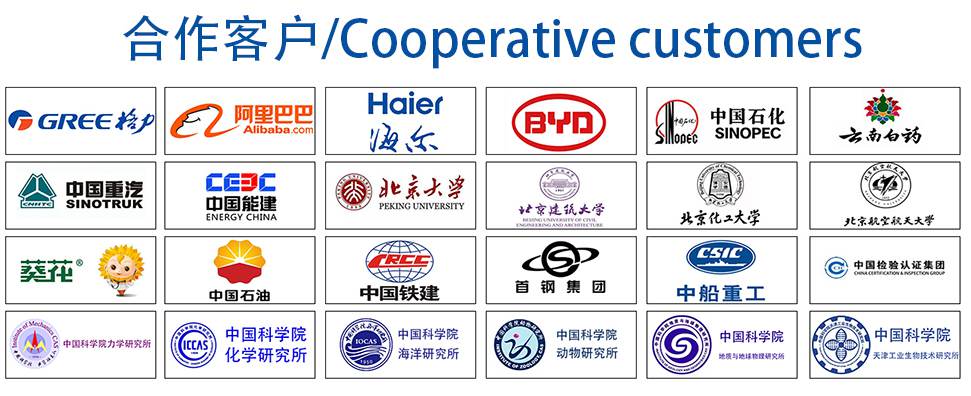