汽车液压盘式制动缸用橡胶密封件检测的重要性
在汽车制动系统中,液压盘式制动缸的橡胶密封件承担着关键作用。它通过保持制动液压力传递的密封性,确保制动力精准响应驾驶员操作,直接影响行车安全。由于橡胶材料易受温度、压力、磨损和化学腐蚀的影响,其性能退化可能导致制动失效或泄漏风险。因此,对橡胶密封件进行系统性检测是保障制动系统可靠性的必要环节,也是汽车零部件质量控制的核心内容之一。
核心检测项目及方法
1. 外观与尺寸精度检测
通过光学显微镜或三维测量仪对密封件表面进行观察,检查是否存在裂纹、气泡、毛边等缺陷,同时测量关键尺寸(如内径、外径、断面厚度)是否符合GB/T 3452.2-2020标准要求。尺寸偏差超过±0.1mm可能影响密封效果。
2. 耐压性能测试
模拟实际工况,在液压试验台上施加最高35MPa压力,持续24小时观察密封件变形量及是否出现渗漏。合格标准要求压力损失不超过初始值的5%,且无永久性结构损伤。
3. 耐温耐候性验证
通过高低温交变试验箱进行循环测试:-40℃至120℃范围内,每个温度点保持4小时,完成100次循环后检查材料硬度变化(邵氏硬度波动≤5HA)、体积膨胀率(<3%)及表面龟裂情况。
4. 化学稳定性分析
将试样浸泡在DOT4制动液中,于100℃环境下保持168小时后,检测质量变化率(±5%以内)、拉伸强度保留率(≥80%)和延伸率保留率(≥70%),评估抗溶胀性能。
5. 动态密封耐久性试验
在专用台架上模拟制动缸活塞往复运动(频率1Hz,行程12mm),连续运行50万次后,检测密封唇口磨损量(≤0.2mm)、摩擦力波动范围(±15%以内)及泄漏量(<0.1ml/h)。
6. 加速老化测试
依据ISO 188标准进行热氧老化试验:120℃环境下暴露500小时,检测拉伸强度、断裂伸长率等力学性能衰减情况,要求性能保留率不低于原始值的75%。
检测标准与质量控制
当前行业主要采用QC/T 831-2010《汽车液压制动主缸、轮缸用橡胶密封件》及SAE J200标准。企业需建立从原材料入厂(如EPDM橡胶的门尼粘度、炭黑分散度)到成品全流程的检测体系,结合X射线探伤、红外光谱分析等齐全技术,确保密封件在10年/20万公里使用周期内的可靠性。
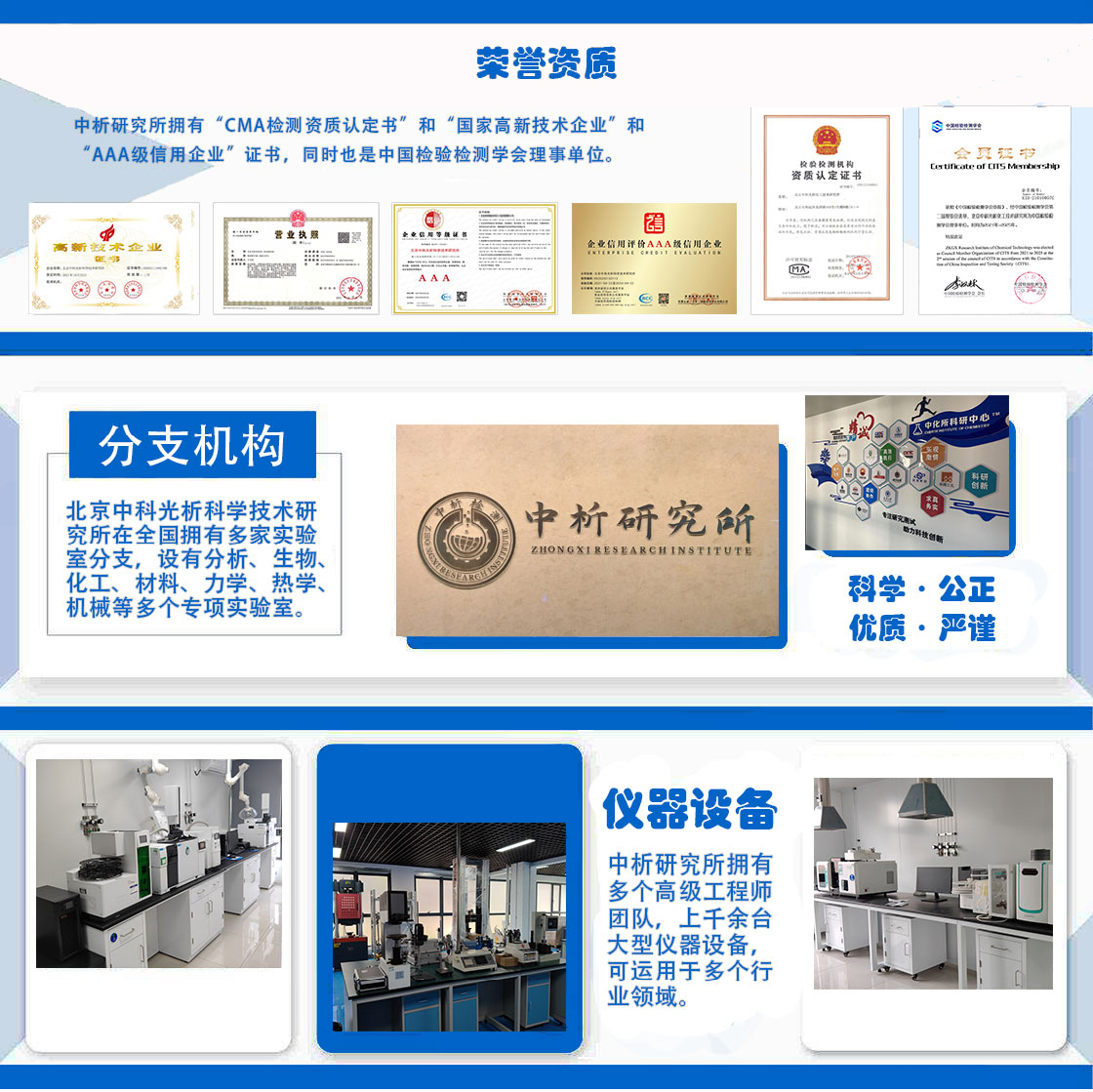
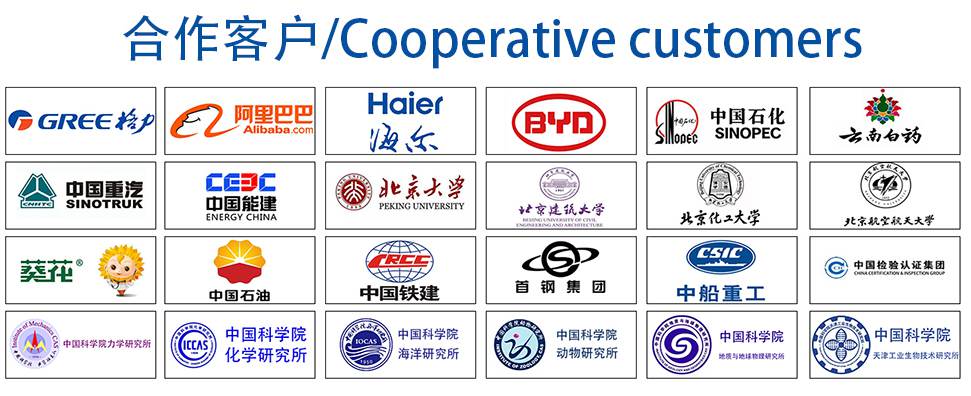