道岔部件检测:保障铁路安全的核心环节
道岔作为铁路轨道的关键设备,承担着引导列车转向、切换轨道的重要功能。其结构复杂且长期承受高频率、高强度的载荷,部件磨损、变形等问题直接影响列车运行的平稳性和安全性。因此,对道岔部件的系统化检测是铁路运维中不可或缺的环节。通过科学规范的检测手段,能够及时发现潜在隐患,预防脱轨、卡阻等重大事故,同时延长道岔使用寿命,降低维护成本。
核心检测项目与技术要求
1. 尖轨检测
尖轨是道岔的核心活动部件,需重点检查轨头磨损量、轨腰厚度及密贴度。使用游标卡尺测量轨头宽度偏差(允许±1mm),激光轮廓仪分析轨面磨耗深度;密贴检测要求尖轨与基本轨间隙≤0.5mm,通过塞尺或电子间隙仪实现动态监测。特殊环境下还需开展低温冷缩变形测试。
2. 辙叉检测
辙叉区需重点检测心轨、翼轨的垂直磨耗和肥边情况。心轨顶面宽度磨损超过6mm需更换,翼轨工作面肥边高度超过2mm必须打磨修复。同时需使用超声波探伤仪对辙叉咽喉、叉心等应力集中区域进行内部缺陷扫描,裂纹深度超过3mm即判定为失效。
3. 连接部件检测
包括螺栓扭矩检测(标准值110-130N·m)、垫板胶垫老化测试(硬度变化超过15%需更换)、滑床台板与尖轨底面的接触面积(应≥80%)。采用智能扳手配合压力传感系统,可实时记录螺栓预紧力数据,防止松动或过紧导致的应力集中。
4. 几何参数综合检测
使用轨检仪对道岔整体几何状态进行三维测量,重点控制轨距偏差(±2mm)、水平高差(≤4mm)、导曲线正矢值等参数。对于大号码道岔(如18#、42#),还需采用全站仪检测线型平顺度,确保列车高速通过的稳定性。
智能化检测技术发展
随着AI与物联网技术的应用,基于机器视觉的轨面伤损自动识别系统、搭载激光雷达的移动检测机器人逐步普及。某铁路局试点项目显示,智能检测将道岔故障识别准确率提升至98%,检测效率提高40%,标志着道岔运维进入数字化新时代。
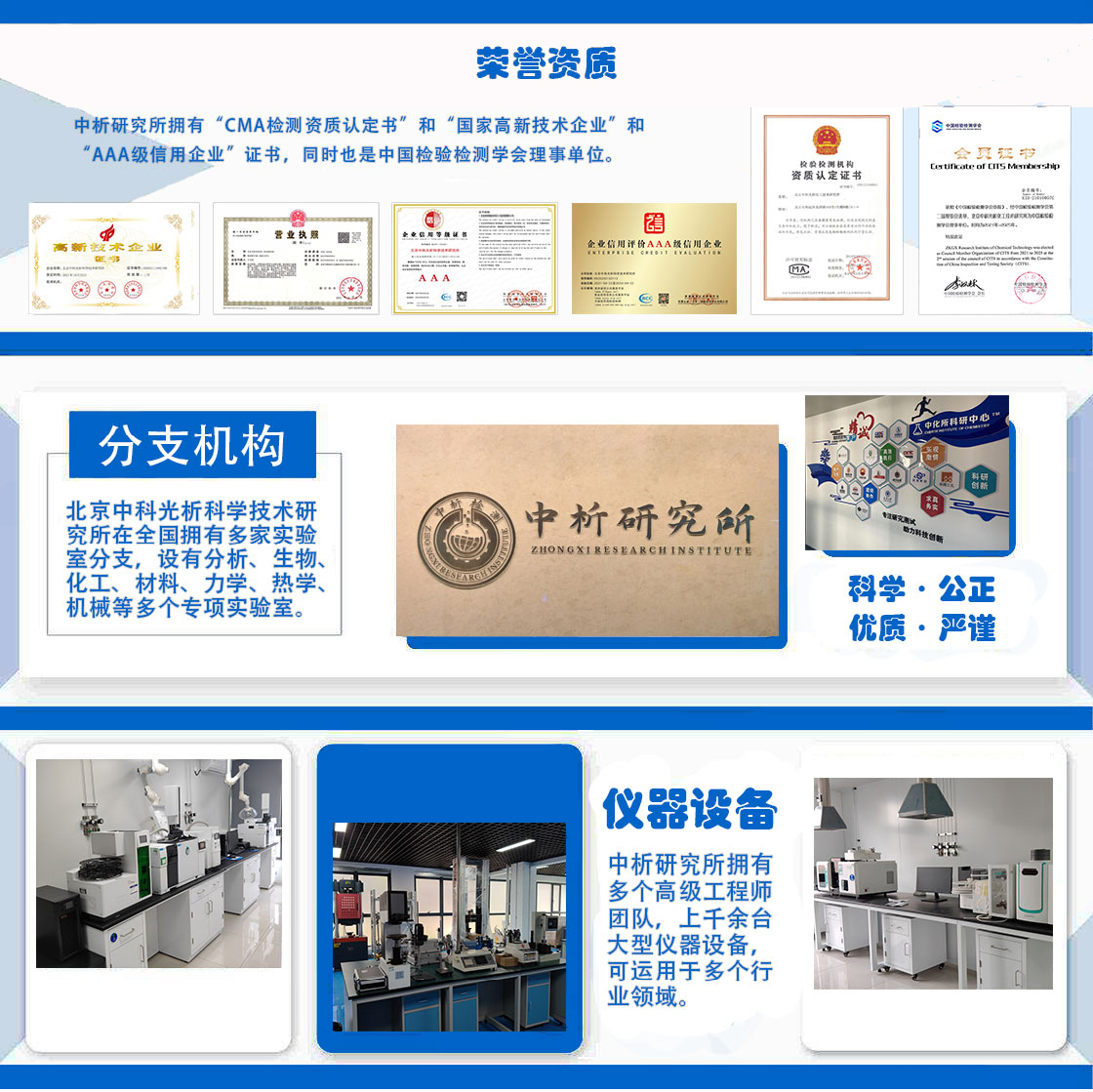
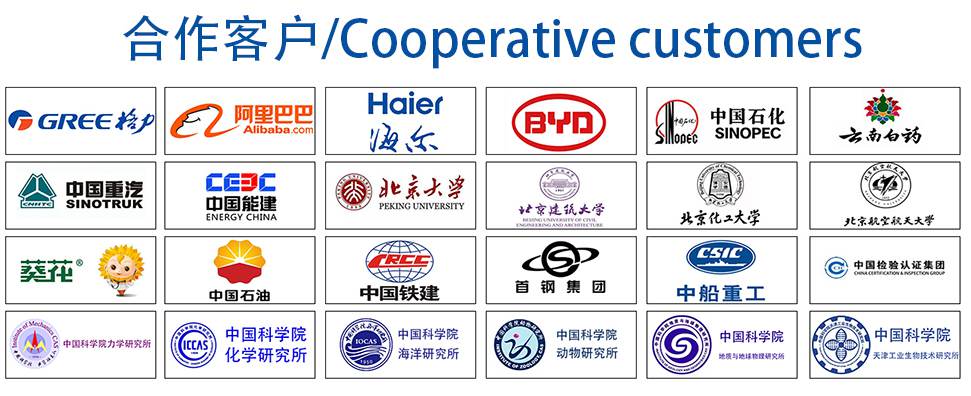