工业设备及管道检测的重要性与核心内容
工业设备及管道是石油化工、能源电力、冶金制造等领域的核心基础设施,其安全性和可靠性直接影响生产效率和人员安全。随着设备运行年限的增加以及复杂工况的长期作用,管道腐蚀、焊缝开裂、材料老化等问题逐渐显现,可能引发泄漏、爆炸等重大事故。因此,定期开展系统化、专业化的检测工作至关重要。科学的检测项目不仅能识别潜在风险,还能通过数据积累优化设备维护策略,延长使用寿命,降低运维成本。同时,在环保法规日益严格的背景下,检测结果也为企业满足排放标准和安全生产要求提供技术支撑。
核心检测项目分类与应用
1. 外观与几何尺寸检测
通过目视检查、三维激光扫描等技术,评估设备及管道表面腐蚀、变形、焊接缺陷等问题。重点检测焊缝质量、法兰连接状态、支撑结构完整性,并使用测厚仪对关键部位进行壁厚测量,判断材料损耗程度。
2. 无损检测技术(NDT)
包括超声波检测(UT)用于内部裂纹探测,射线检测(RT)观察焊接接头质量,磁粉检测(MT)和渗透检测(PT)发现表面及近表面缺陷。其中相控阵超声(PAUT)和衍射时差法(TOFD)可实现高精度缺陷定位。
3. 压力与密封性测试
通过水压试验、气压试验验证管道承压能力,结合气泡法、氦检漏技术或红外热成像检测微泄漏点。在线声发射监测技术可实时捕捉压力变化时的异常信号。
4. 腐蚀状态评估
采用电化学阻抗谱(EIS)、线性极化电阻(LPR)等电化学方法分析腐蚀速率,结合金相显微镜观察微观组织变化。对于保温层下腐蚀(CUI),需使用脉冲涡流(PEC)等穿透性检测技术。
5. 材料性能分析
通过光谱分析、硬度测试、拉伸试验等手段验证材料力学性能,判断是否发生氢脆、应力腐蚀开裂(SCC)等失效现象。对高温高压设备还需进行蠕变损伤评估。
6. 智能检测技术应用
运用管道爬行机器人(PIG)、无人机(UAV)搭载高清摄像头或热像仪进行长距离巡检,结合AI算法实现缺陷自动识别。分布式光纤传感系统可实时监测温度、应变等参数变化。
检测数据管理与决策支持
建立设备健康档案数据库,通过剩余寿命预测模型和风险评估矩阵,制定分级维护计划。检测结果需符合ASME、API、GB/T等国内外标准规范,为技术改造和备件更换提供科学依据。
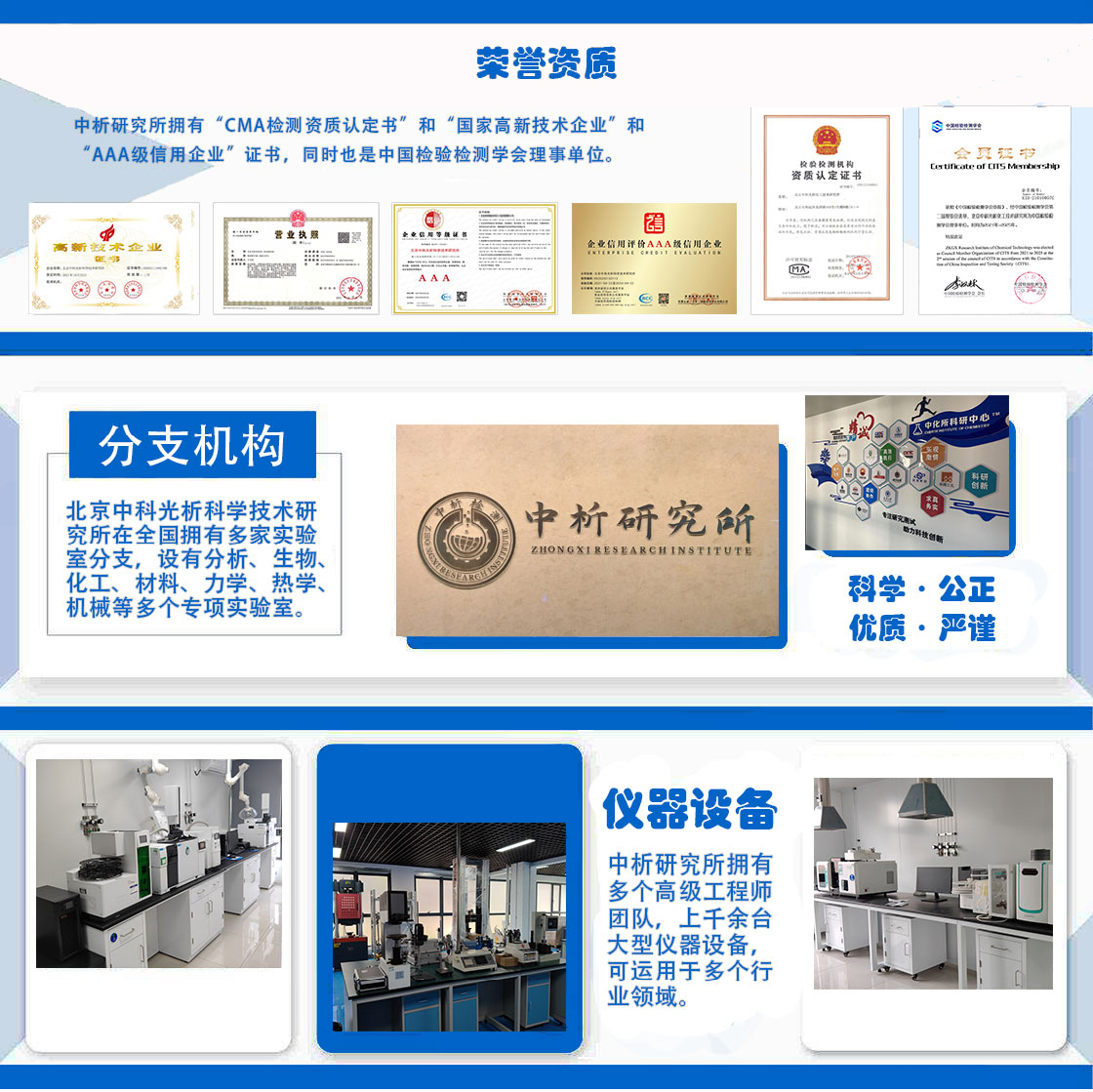
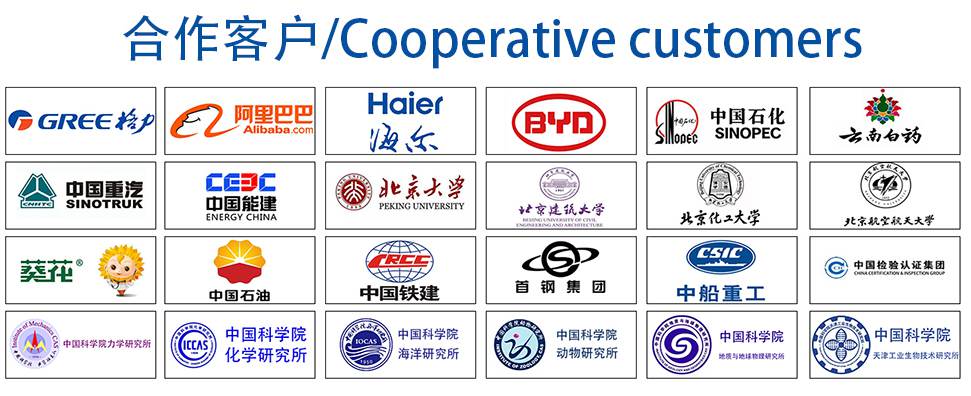