汽车空调用密封件检测的重要性
汽车空调系统的密封件是保障制冷剂循环、防止泄漏的核心部件,其性能直接影响空调的制冷效率、能耗及环保性。随着新能源汽车和智能驾驶技术的快速发展,空调系统对密封件的耐高温、耐腐蚀、抗老化等要求日益严格。据统计,约30%的空调系统故障源于密封件失效,因此对密封件的检测成为汽车零部件质量控制的关键环节。检测项目需覆盖材料性能、密封性、耐久性等多个维度,确保其在复杂工况下的可靠性。
核心检测项目及方法
1. 材料理化性能检测
通过硬度测试(邵氏A/D)、拉伸强度试验、压缩永久变形测试等,评估密封件橡胶材料的机械性能。例如,ASTM D2000标准要求橡胶件在125℃下老化70小时后,硬度变化不超过±5 IRHD。
2. 密封性能测试
采用氦质谱检漏法或压力衰减法检测密封件的气密性,模拟空调系统实际工作压力(通常为2.5-4.0MPa)。国际通用标准ISO 188要求密封件在交变压力下5000次循环后泄漏量≤1.5g/年。
3. 耐候性试验
通过高温高湿试验(85℃/85%RH,持续1000小时)、低温脆性试验(-40℃)及臭氧暴露试验(50pphm浓度,72小时),验证密封件的环境适应性。符合SAE J200标准的密封件应无龟裂、硬化现象。
精密尺寸与装配检测
采用三坐标测量仪对密封件的截面直径、圆度、表面粗糙度(Ra≤1.6μm)进行微米级检测,确保与压缩机、管路的装配匹配度。同时运用有限元分析(FEA)模拟密封件在振动工况下的接触应力分布,优化结构设计。
综合评估与质量控制
建立包含60余项参数的检测数据库,结合AI算法对检测数据进行趋势分析。例如,通过监测橡胶硫化曲线的焦烧时间(T10)和正硫化时间(T90),实现生产工艺的实时优化。合格的密封件需通过DV(设计验证)和PV(生产验证)双重认证,确保全生命周期可靠性。
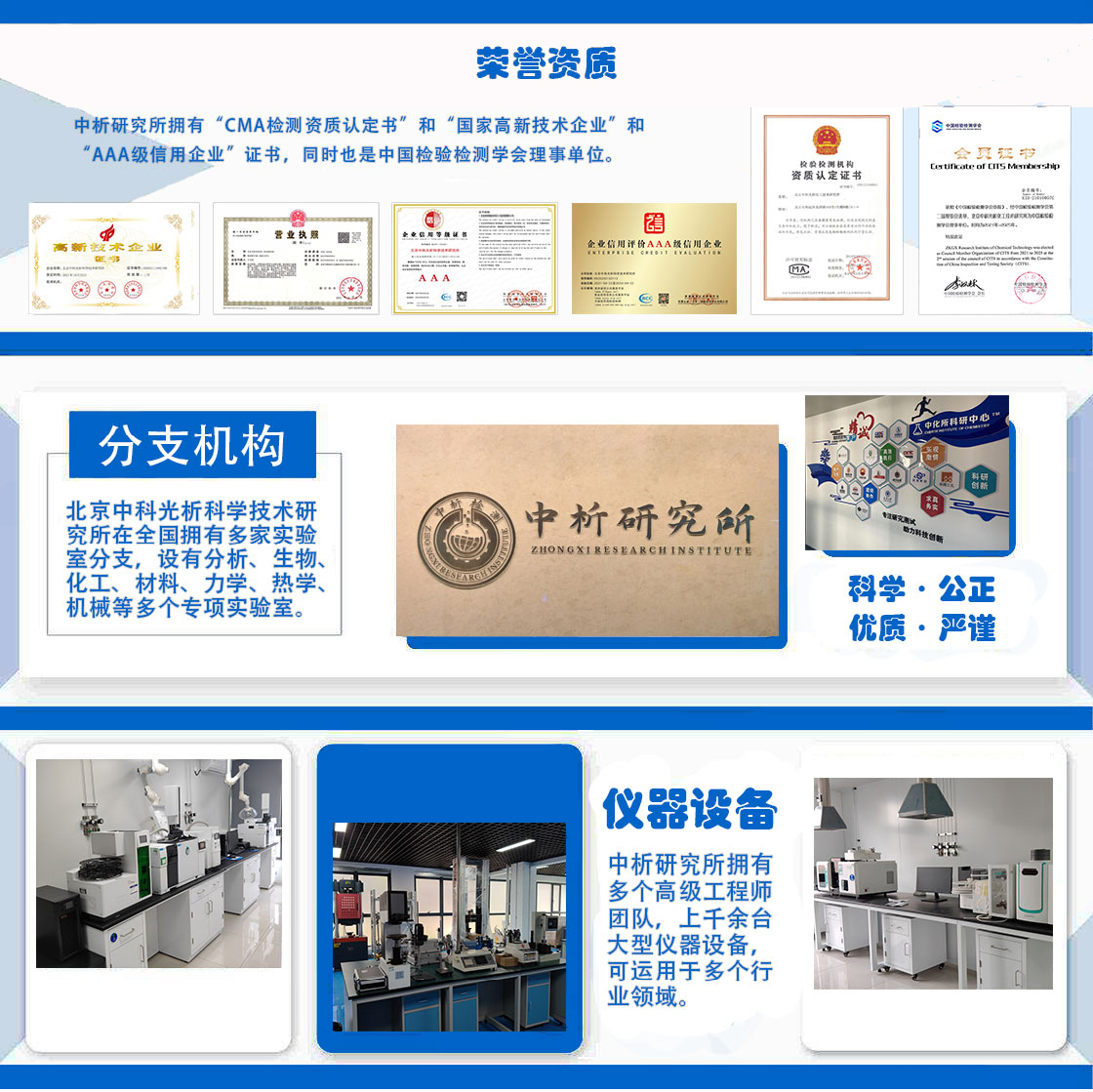
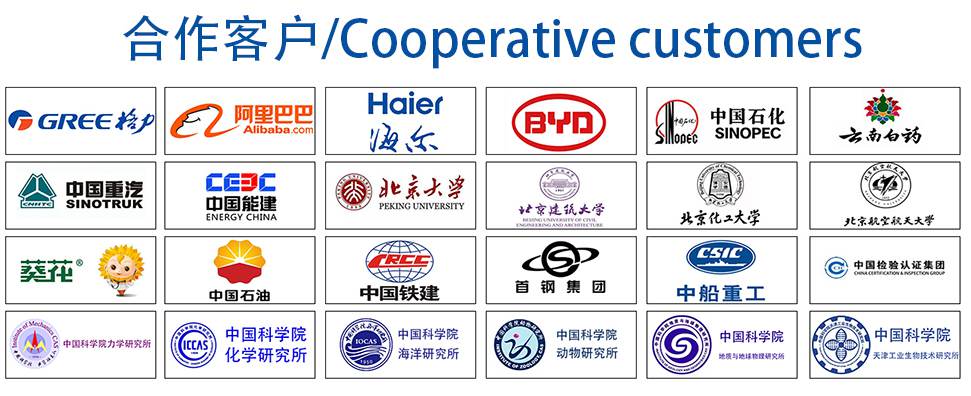