船用防锈漆检测的重要性
船用防锈漆是船舶防腐体系的核心组成部分,直接关系到船舶在海洋恶劣环境中的使用寿命和安全性。由于船舶长期暴露于高盐雾、高湿度、紫外线辐射及微生物侵蚀等复杂条件下,防锈漆的失效可能导致船体结构腐蚀、设备损坏甚至安全隐患。因此,对船用防锈漆的检测不仅是行业规范要求,更是保障船舶运营安全和经济性的必要措施。通过科学系统的检测,可评估涂层的附着力、耐腐蚀性、耐候性等关键性能,确保其符合国际标准(如ISO 12944、IMO PSPC)和实际工况需求。
船用防锈漆的主要检测项目
1. 附着力测试
附着力是衡量防锈漆与基材结合强度的核心指标。通过划格法(ASTM D3359)或拉开法(ISO 4624)进行测试,评估涂层在机械应力下的抗剥离能力。附着力不足可能导致漆膜脱落,加速船体腐蚀。
2. 耐盐雾性能检测
采用盐雾试验箱(ASTM B117)模拟海洋盐雾环境,连续喷洒5%氯化钠溶液,测试漆膜在特定周期(如1000小时)内的抗腐蚀能力。观察表面起泡、锈斑或剥落现象,评估防锈性能等级。
3. 膜厚检测
使用磁性测厚仪(ISO 2808)或涡流测厚仪,测量干膜厚度(DFT)是否符合设计要求。膜厚不足会降低防护效果,过厚则可能导致开裂或成本浪费,需确保均匀性控制在±20%以内。
4. 耐候性测试
通过QUV加速老化试验(ASTM G154),模拟紫外线、温湿度循环等环境因素,评估漆膜抗粉化、变色和开裂的能力。测试周期通常为2000小时以上,以预测涂层在长期暴晒下的性能变化。
5. 化学成分分析
采用FTIR红外光谱或GC-MS检测漆料中树脂、颜料、溶剂的配比是否符合配方标准,重点筛查铅、铬等有害物质含量是否满足IMO《船舶有害涂层控制公约》要求。
6. 耐阴极剥离性测试
模拟船体阴极保护系统(-0.8V~-1.1V)下的涂层表现,通过标准测试(ISO 15711)评估漆膜在电解环境中的抗剥离能力,防止因电化学腐蚀导致的失效。
检测方法的选择与意义
针对不同船型(如散货船、油轮、军舰)和涂装部位(水线以下、甲板、压载舱),需结合具体服役环境选择检测项目。例如,压载舱涂层需额外增加耐水压试验(IMO MSC.215(82)),而水线区涂层需关注耐干湿交替性能。通过第三方权威机构检测,可为船舶设计、维修和保险评估提供客观数据支持,避免因涂层失效引发的数千万美元级腐蚀损失。
结语
船用防锈漆检测是船舶建造与维护中不可忽视的技术环节。随着环保法规(如VOCs限制)和智能检测技术(如涂层传感器)的发展,未来检测将更加注重全生命周期性能监测。建议企业建立从原料采购、施工监理到定期检测的全流程质量管理体系,以最大限度延长船舶服役周期,保障航行安全。
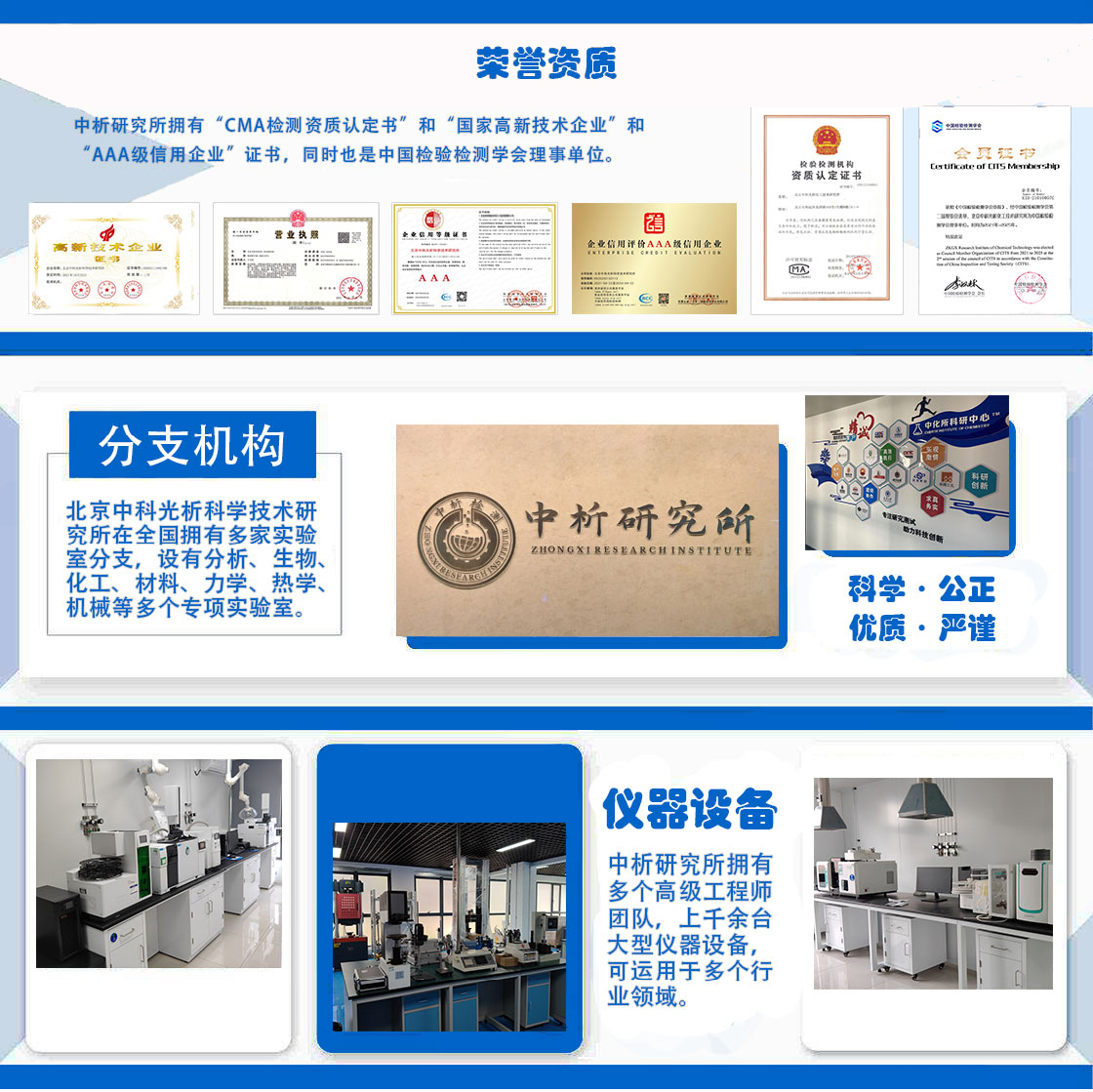
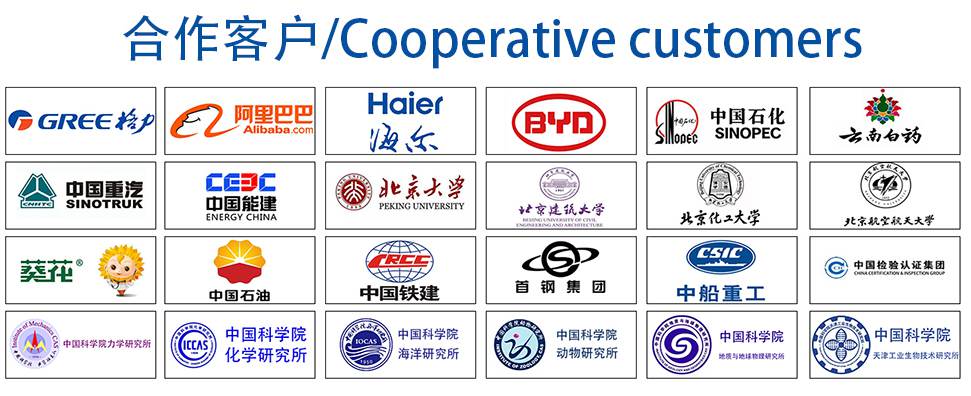