密闭翼环检测的重要性与核心内容
密闭翼环作为管道系统、压力容器及特殊设备中关键的密封组件,其性能直接影响设备运行安全性与介质防泄漏能力。在石油化工、核电、医药制造等高危行业,密闭翼环的失效可能导致严重的安全事故、环境污染或生产中断。因此,系统化的密闭翼环检测成为设备维护与质量控制的核心环节,需通过科学的检测项目验证其设计强度、密封效能及耐久性,确保符合GB/T 12459、ASME B16.9等国家标准或国际规范要求。
密闭翼环检测核心项目
1. 几何尺寸与形位公差检测
使用三维坐标测量仪、激光扫描仪等设备,检测翼环的内外径、环体厚度、螺栓孔间距等关键尺寸,验证与设计图纸的吻合度。重点检测密封面的平面度、表面粗糙度(Ra≤3.2μm),确保安装后接触面紧密无缝隙。
2. 材料成分与力学性能检测
通过光谱分析仪进行材质验证,确认不锈钢、哈氏合金等材料的元素含量符合ASTM A182标准。开展拉伸试验(屈服强度≥205MPa)、冲击试验(-46℃低温冲击功≥27J)及硬度测试(HB≤187),评估材料在极端工况下的抗变形能力。
3. 密封性能压力测试
采用液压试验台进行1.5倍工作压力的静态保压测试,持续时间≥30分钟,观察有无渗漏或变形。对于气体介质系统,需额外进行氦质谱检漏,泄漏率需≤1×10⁻⁶ Pa·m³/s,确保在动态工况下的气密性。
4. 腐蚀防护与表面质量检测
运用金相显微镜检查镀层(如镀锌、镀镍)厚度(30-50μm)及结合力,通过盐雾试验(500小时)评估耐腐蚀性。使用渗透探伤(PT)或磁粉探伤(MT)检测表面微裂纹,缺陷长度应≤0.8mm且无贯穿性裂纹。
5. 安装配合与疲劳寿命测试
模拟实际工况进行5000次以上的循环加载试验,检测翼环与法兰的配合间隙(≤0.05mm)变化,同时通过有限元分析(FEA)评估应力分布情况,预测在交变载荷下的疲劳寿命是否达到10万次循环要求。
检测结果的应用与发展趋势
通过上述检测项目生成的量化数据,可为设备安全评级、维修周期制定提供科学依据。随着智能传感技术的应用,未来将逐步实现翼环状态在线监测,结合大数据分析提前预警失效风险,推动检测方式从定期维护向预测性维护转型。
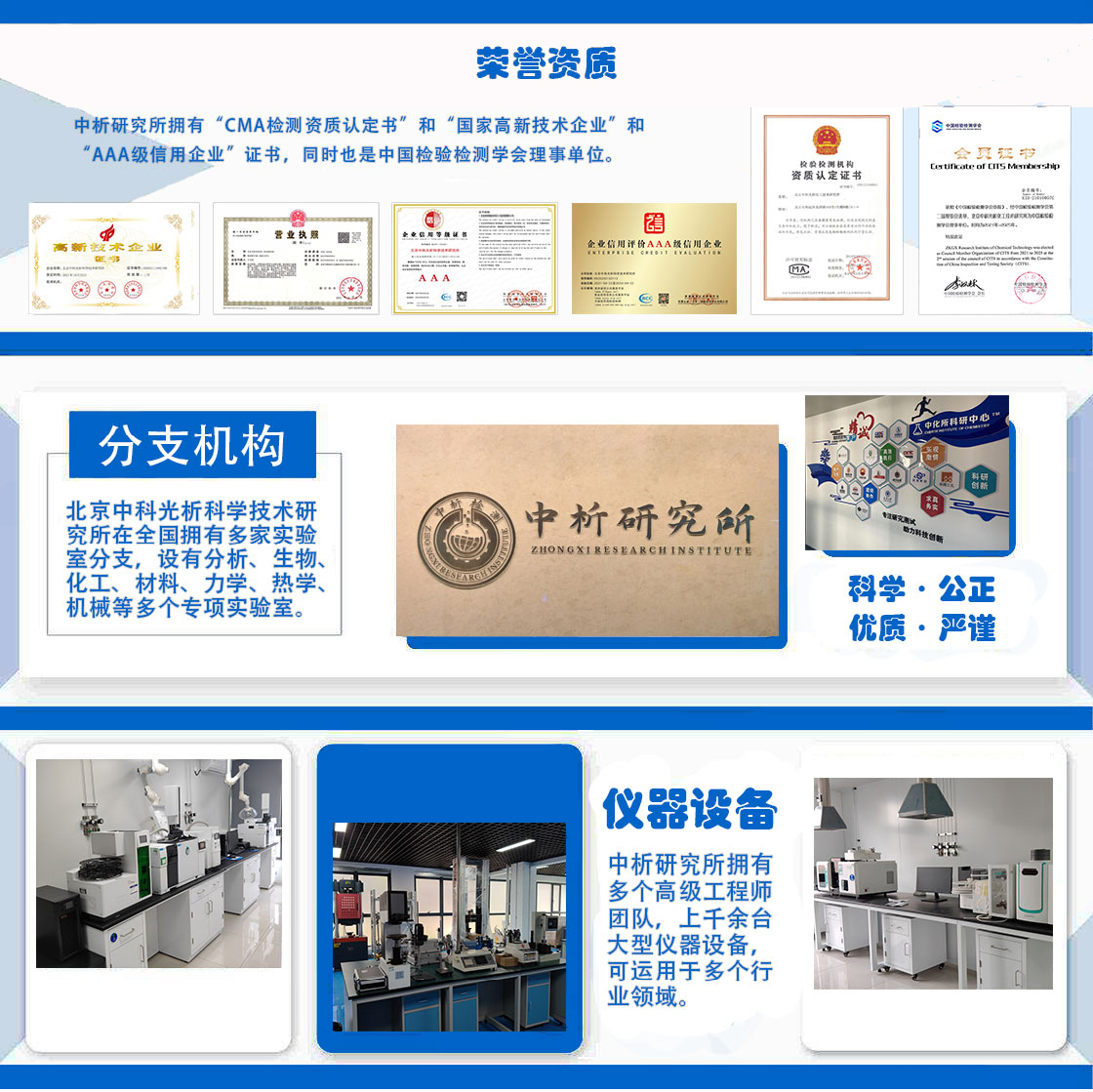
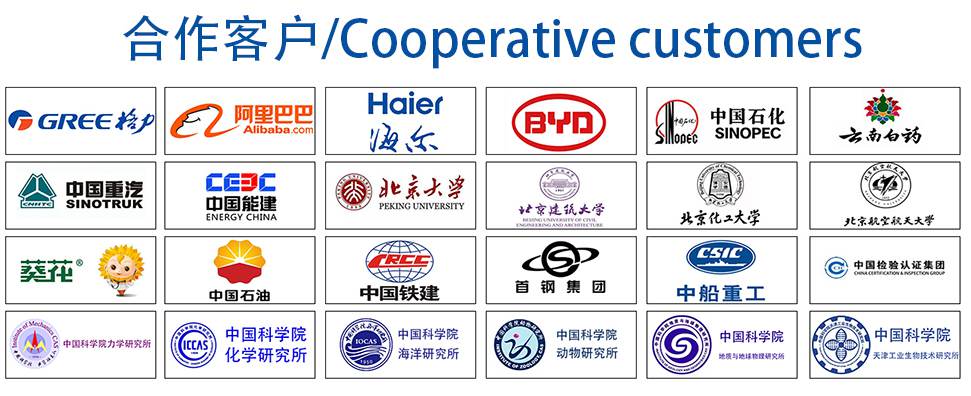