离心泵检测的重要性及核心内容
离心泵作为工业生产和流体输送领域的核心设备,广泛应用于化工、能源、水处理、农业灌溉等场景。其运行状态直接影响生产效率、能耗水平和系统安全性。由于离心泵长期处于高速旋转、介质腐蚀及复杂工况下,叶轮磨损、轴承失效、密封泄漏等故障易发,可能引发停机事故或安全隐患。因此,定期开展系统化的离心泵检测是设备管理的重要环节,能够有效评估泵体性能、预测潜在风险并延长使用寿命。
离心泵检测的核心项目
1. 性能参数检测
包括流量、扬程、轴功率及效率的实测值与设计值的对比分析。通过流量计、压力传感器和功率测试仪,结合国家标准(如GB/T 3216)进行工况点测试,判断是否存在性能衰减。若实测效率下降5%以上,可能提示叶轮磨损或流道堵塞。
2. 振动与噪声检测
使用振动分析仪对轴承座、泵壳等部位进行多点振动频谱测量,重点关注振幅(RMS值)和频率特征。异常高频振动可能指示轴承损坏,低频振动则与转子不平衡或对中偏差相关。同时需检测运行噪声,超过85dB(A)时应排查气蚀或结构松动问题。
3. 密封系统检测
针对机械密封或填料密封进行泄漏量监测,结合红外热成像技术检查密封面温度分布。机械密封泄漏量超过5滴/分钟或填料密封压盖过热(>80℃)均需立即维护。对于高危介质场景,还需进行密封失效模拟试验。
4. 材料完整性检测
采用超声波测厚仪量化泵壳、叶轮的壁厚减薄情况,结合内窥镜观察流道腐蚀状态。关键部位(如叶轮入口)厚度损失超过10%时需更换。同时检查螺栓预紧力是否符合VDI 2230标准,防止连接失效。
5. 电气系统检测
包括电机绝缘电阻(500V兆欧表测量值应≥1MΩ)、三相电流平衡度(偏差<10%)及温升检测。使用电能质量分析仪捕捉电压谐波和功率因数异常,防止因电气问题导致的效率损失。
6. 润滑系统检测
通过油液光谱分析检测轴承润滑油的金属磨粒含量,铁元素浓度超过100ppm需预警。同时检查油品粘度变化,当偏离标称值15%时应更换润滑油。对于脂润滑轴承,需定期补充润滑脂并监测注脂压力。
检测周期与数据管理
建议每月进行运行参数巡检,每季度开展振动分析,年度大修期间实施全面检测。建立设备健康档案,通过趋势分析预测剩余寿命。对高风险泵体(如输送腐蚀性介质)应缩短检测周期,必要时加装在线监测系统实现实时预警。
通过科学的检测体系,可降低离心泵故障率30%-50%,同时提高能效3%-8%。检测数据不仅指导维保决策,更为设备改造和新泵选型提供重要参考依据。
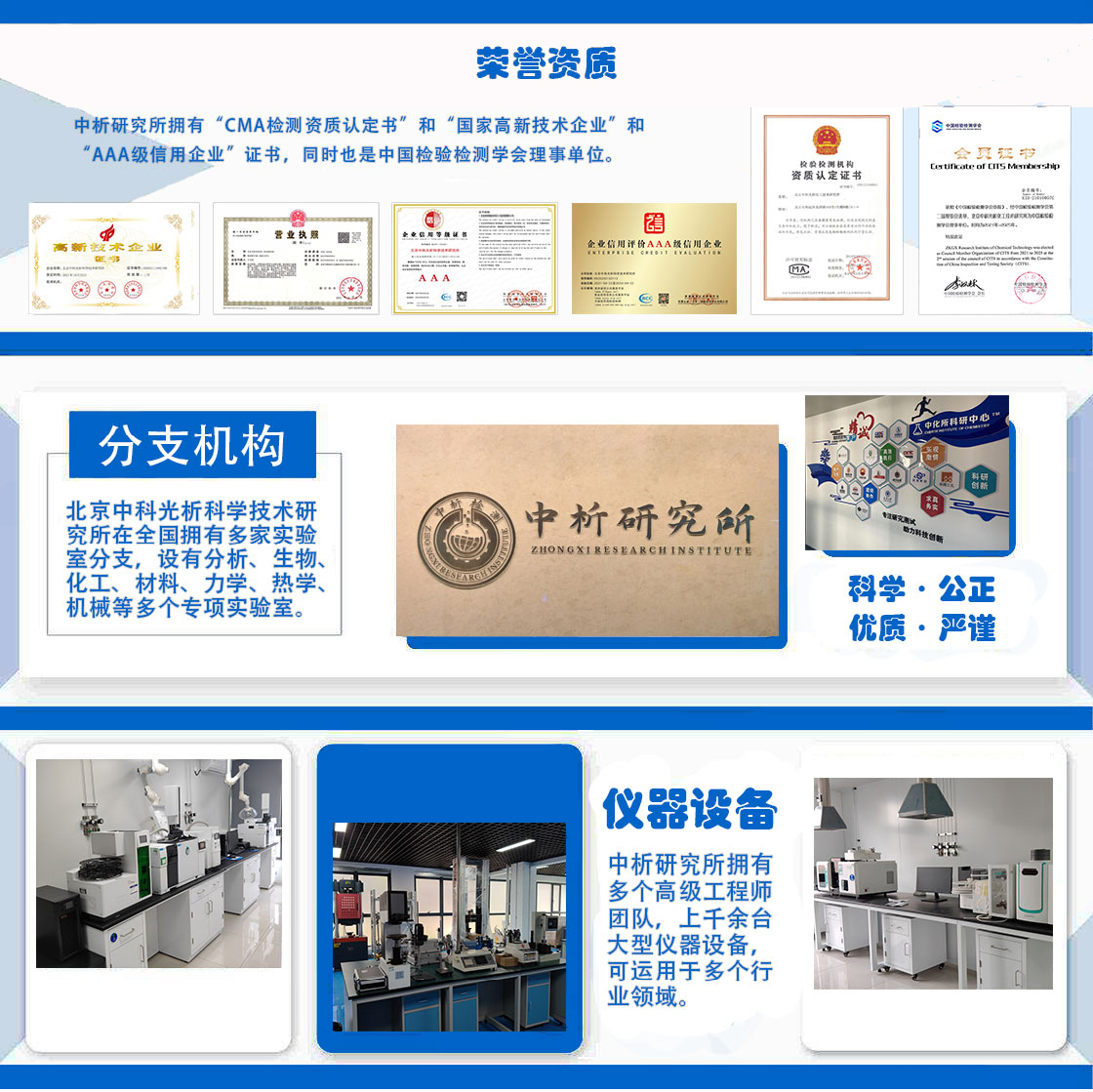
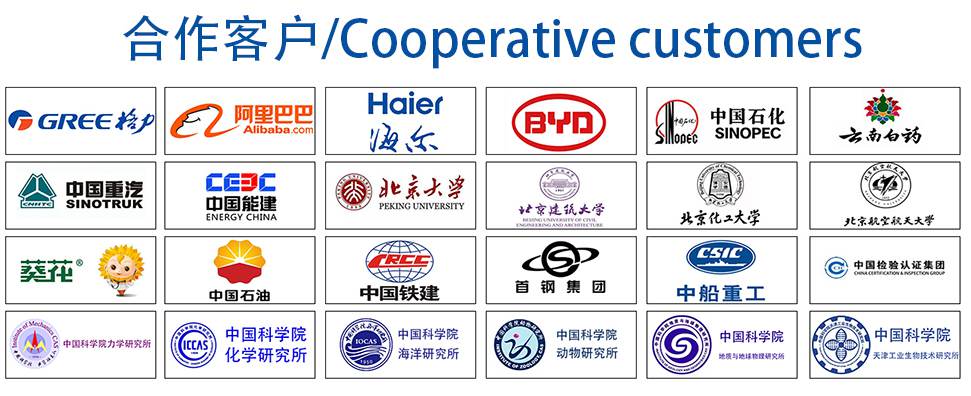