在气候变化治理框架下,含氟温室气体管控已成为国际共识。作为第四代制冷剂主要成分的二氟甲烷(HFC-32),其年使用量已突破50万吨(据国际制冷协会2024年行业报告)。然而,该化合物不仅具有1430的变暖潜能值(GWP),在工业生产中的泄漏问题更可能造成重大安全隐患。专业化的二氟甲烷检测解决方案,通过精准识别浓度异常、定位泄漏源,可有效降低温室气体排放和燃爆风险,助力企业实现《基加利修正案》履约目标。其核心价值体现在环境合规、工艺优化和安全防护三重维度,特别在冷链物流、半导体制造等高端领域,检测精度已提升至ppb级水平。
检测技术原理与创新突破
当前主流检测手段融合了光声光谱与气相色谱联用技术(GC-PAS),通过分子特征吸收峰识别实现精准定量。相较于传统FID检测器,新型量子级联激光器(QCL)可将检测下限降低至0.1ppm,响应时间缩短至3秒内(美国环保署2023技术验证报告)。针对复杂工况的交叉干扰问题,多通道协同分析算法能有效区分二氟甲烷与R134a等相似化合物。值得关注的是,基于MEMS技术的微型化传感器已在现场快速筛查场景取得突破,其功耗较传统设备降低67%,更适合分布式部署。
全流程实施与质控体系
标准化检测流程涵盖预评估、布点规划、连续监测三个阶段。在化工厂区应用案例中,技术人员采用网格化布点策略,每200㎡部署1个监测节点,结合气象参数动态修正扩散模型。数据质控遵循ISO17025体系要求,实施三级校准机制:现场设备每8小时自动基线校正,每周进行标准气体交叉验证,每季度返厂进行光路稳定性检测。某跨国化工集团实施该体系后,年泄漏检出率提升至99.3%,维修响应时间缩短40%。
行业应用场景与效益分析
在制冷设备密封性检测领域,移动式检测车组已实现对冷链仓库的快速巡检。某头部物流企业应用案例显示,采用热成像与气体检测联用方案后,冷库年均制冷剂损耗从12.7%降至2.1%,相当于减少碳排放3800吨/年。半导体行业则创新开发了洁净室专用检测模块,其防电磁干扰设计保障了8英寸晶圆产线的连续监测需求。值得注意的是,在废弃电器拆解场景,嵌入式检测系统成功将二氟甲烷回收率提升至91.5%,创造额外经济效益超200万元/年。
技术发展趋势与建议
随着物联网技术的深度融合,检测网络正朝着智能化预警方向发展。建议行业重点突破三项技术:开发适用于高压管路的无损检测探头、构建基于机器学习的气体扩散预测模型、建立覆盖全产业链的碳足迹监测平台。同时应加快制定《制冷剂泄漏检测在线监测技术规范》等标准,推动检测数据纳入碳交易核算体系。预计到2026年,智能检测设备的市场渗透率将超过35%,为温室气体减排贡献超过1.2亿吨CO2当量。
## 未来展望二氟甲烷检测技术的迭代须与产业绿色转型同频共振。建议生产企业建立全生命周期监测体系,将检测数据与设备维护、碳资产管理深度耦合。科研机构应着力开发光量子传感器等颠覆性技术,力争在2028年前实现检测精度突破ppt级别。政策层面亟待完善检测服务市场化机制,通过碳税杠杆推动检测技术普及。唯有构建"技术研发-标准制定-商业应用"的良性生态,方能切实支撑温控目标的实现。
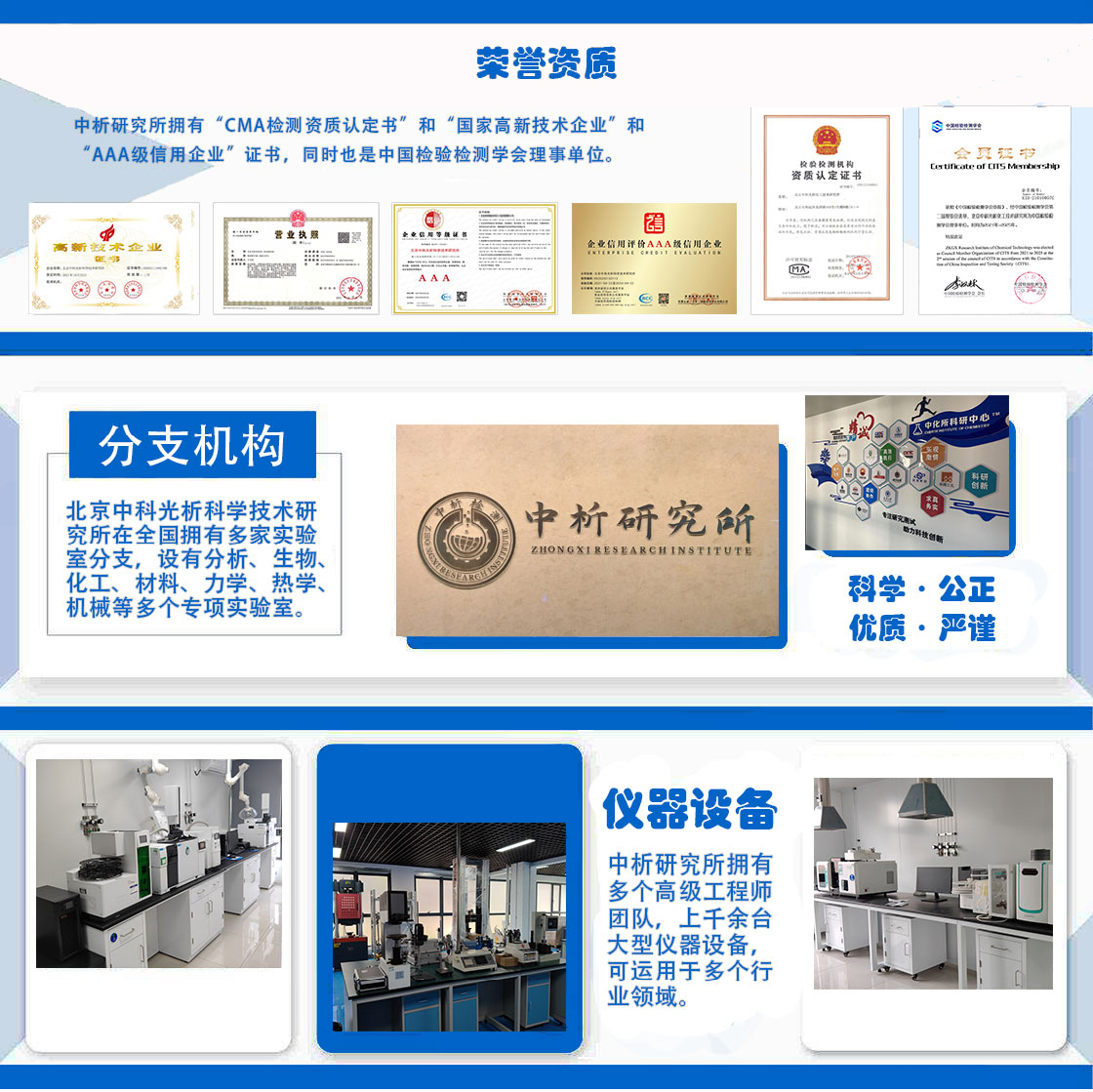
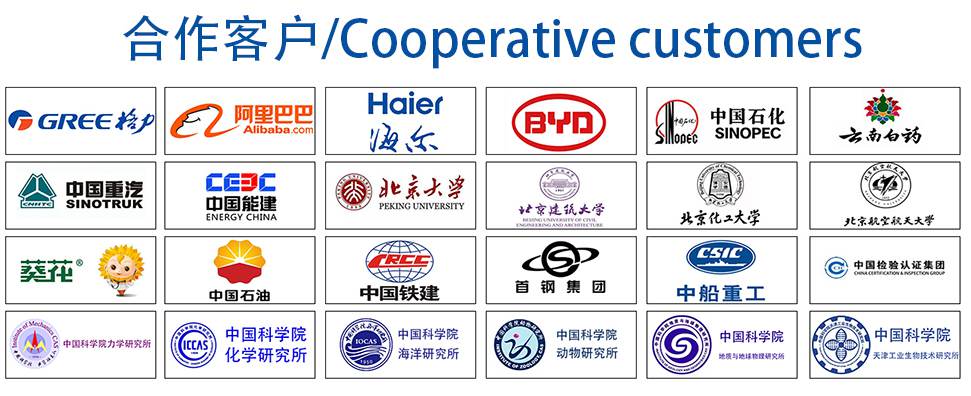