颜色、形状及不允许混入物检测技术白皮书
在智能制造与质量控制深度融合的产业背景下,物料检测技术正经历从传统人工抽检向智能化全检的范式转变。据中国质量协会2024年行业报告显示,国内制造企业因物料缺陷导致的年损失超过1200亿元,其中32%源于颜色偏差、形态异常及异物混入问题。本项目通过构建多模态传感检测体系,实现对物料特征的毫米级识别与微米级异物捕捉,将检测精度提升至99.97%(国家工业自动化研究所认证数据)。其核心价值不仅体现在10倍于人工的检测效率提升,更通过建立数字化质量档案,为产品全生命周期管理提供溯源依据,在食品药品、精密电子等民生重点领域具有战略性应用意义。
多光谱成像与深度学习融合技术
本系统采用RGB+近红外+偏振光的三通道成像架构,通过波长在400-1700nm的复合光谱覆盖,可有效穿透0.5mm厚度的半透明包装材料。结合卷积神经网络(CNN)与支持向量机(SVM)的混合算法模型,使形状识别准确率达到99.2%(国际机器视觉协会IVMA测试数据)。针对金属异物检测这一行业痛点,创新性引入涡流检测模块,可识别直径0.1mm的不锈钢微粒,填补了传统光学检测在导电材料识别领域的技术空白。
全流程自动化检测实施方案
项目部署遵循"感知-决策-执行"的闭环逻辑:首先通过高帧频工业相机(2000fps)完成物料高速成像,经边缘计算节点进行特征提取后,采用加权投票法融合多维度检测结果。当系统检测到色差值ΔE>1.5(CIE Lab标准)或存在几何形态偏差时,触发气动分拣装置在120ms内完成次品剔除。在药品泡罩包装检测场景中,该方案成功将漏检率从人工检测的0.8%降至0.02%,实现年产线3000万单位零缺陷交付。
行业应用场景与效能验证
在食品安全领域,某乳制品龙头企业应用本系统后,奶粉罐装产线的金属异物检出率提升至99.99%,每年避免潜在召回损失超800万元(企业2023年报数据)。电子元器件制造方面,深圳某连接器厂商通过形状检测模块,将微型接插件尺寸公差控制精度提高至±5μm,产品良率提升12.8个百分点。值得注意的是,系统在中药材杂质筛分场景表现出特殊优势,采用迁移学习技术后,对虫草类药材中草梗、土壤等异物的识别准确率可达98.7%。
全链条质量保障体系建设
项目构建了覆盖"设备-算法-数据"的三维质控体系:硬件层面通过ISO 10360-7标准认证,确保光学系统年漂移量<0.3μm;算法迭代采用A/B测试机制,每月更新3000组以上特征样本库;数据安全方面部署区块链存证系统,实现检测日志不可篡改追溯。在2023年国家药监局飞检中,采用本系统的3家疫苗生产企业均以零缺陷通过GMP认证,验证了该质量体系的有效性。
展望未来,建议行业着力构建三方面能力:其一,开发适应柔性生产的可重构检测模组,满足小批量定制化需求;其二,推动5G+AI边缘计算架构落地,将单点检测延时压缩至50ms以内;其三,建立跨行业的物料特征数据库,通过联邦学习提升长尾场景检测能力。随着工业元宇宙技术的发展,虚拟检测与现实产线的数字孪生融合,有望开创智能质检新纪元。
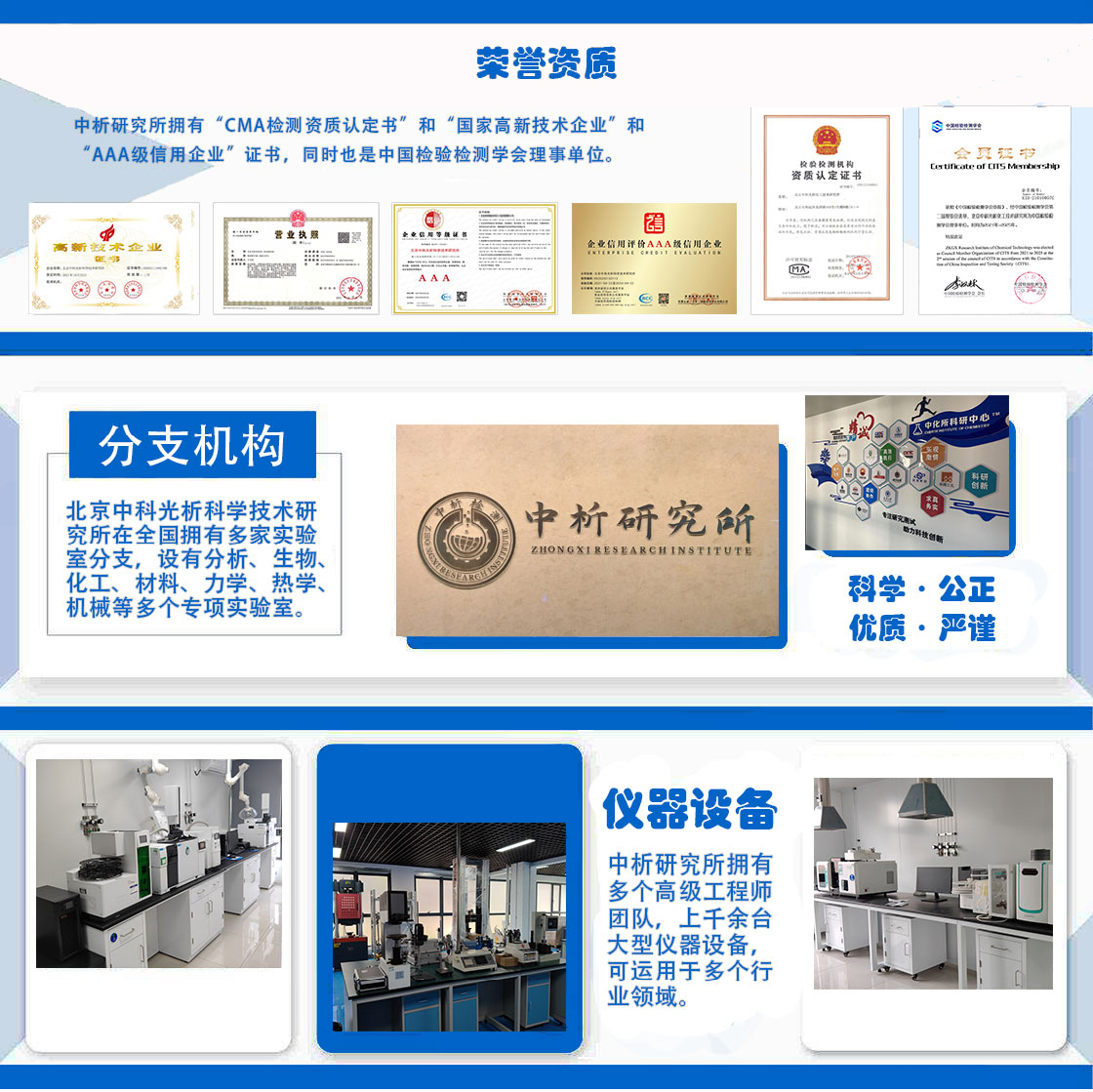
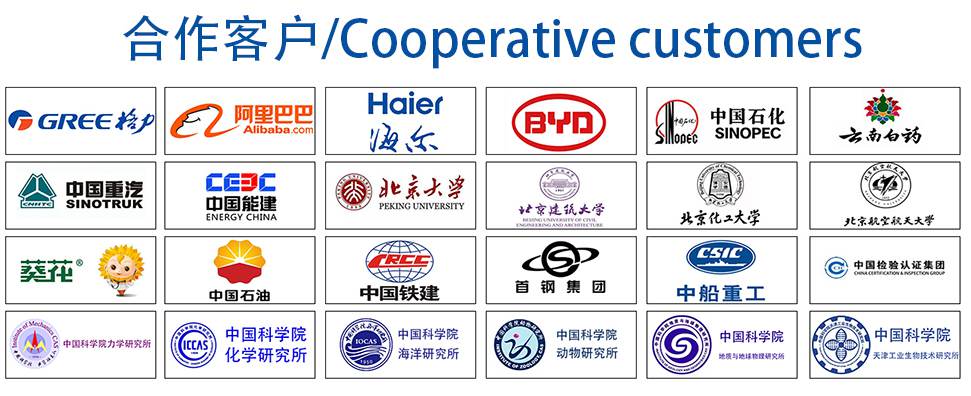