平均长度检测:核心检测项目与应用解析
一、核心检测项目
-
- 目标产品:明确被测物类型(如金属零件、塑料管材、纺织品、印刷纸张、电缆等)。
- 检测层级:单个产品长度、批次平均长度或多个连续样本的动态平均值。
-
- 手动工具:高精度卡尺、千分尺、卷尺(精度需符合ISO 9001或GB/T标准)。
- 自动化设备:激光测距仪、光学影像测量系统、在线连续测量装置(如CCD传感器系统)。
- 辅助工具:固定夹具、温度补偿装置(用于热膨胀系数敏感材料)。
-
- 抽样规则:按GB/T 2828或MIL-STD-105E标准确定抽样比例及随机性。
- 测量流程:
- 校准设备(每日使用前需进行零点校准)。
- 固定被测物以减少振动误差。
- 多点测量(至少3次不同位置取均值)。
- 记录原始数据并标记环境条件(温度、湿度)。
- 特殊场景:柔性材料需施加标准张力(如纺织品检测参照ASTM D3773)。
-
- 计算公式: 平均长度=∑�=1����平均长度=n∑i=1nLi 其中 ��Li 为单次测量值,�n 为样本数量。
- 误差分析:
- 允许公差范围(如±0.5mm或设计值的±1%)。
- 使用标准差(SD)或极差(R)评估批次一致性。
- 不合格处理:触发自动报警、隔离问题批次、启动根因分析(如设备偏移或材料收缩)。
-
- 通用标准:ISO 9001(质量管理体系)、ISO 2768(一般公差标准)。
- 行业规范:
- 纺织业:ASTM D1776(织物长度检测)。
- 制造业:ASME Y14.5(尺寸与公差规范)。
- 电子工业:IPC-A-600(PCB尺寸验收标准)。
二、检测应用场景
-
- 案例:汽车零部件供应商需确保螺栓螺纹长度为12±0.1mm,每批次抽检100件,使用三坐标测量机(CMM)验证。
- 价值:避免装配失误导致的召回风险。
-
- 案例:布料卷材的平均长度检测,通过光电传感器实时监控,防止裁切浪费。
- 标准:误差超过±0.5%时自动调整生产线张力。
-
- 案例:纸箱印刷模切尺寸的在线检测,利用机器视觉系统剔除超差品。
三、技术趋势与挑战
- 智能化升级:AI算法实时分析检测数据,预测设备偏移趋势。
- 高精度需求:纳米级测量需求推动激光干涉仪的应用(如半导体晶圆检测)。
- 环境干扰:温度波动对金属材料的影响需动态补偿。
四、
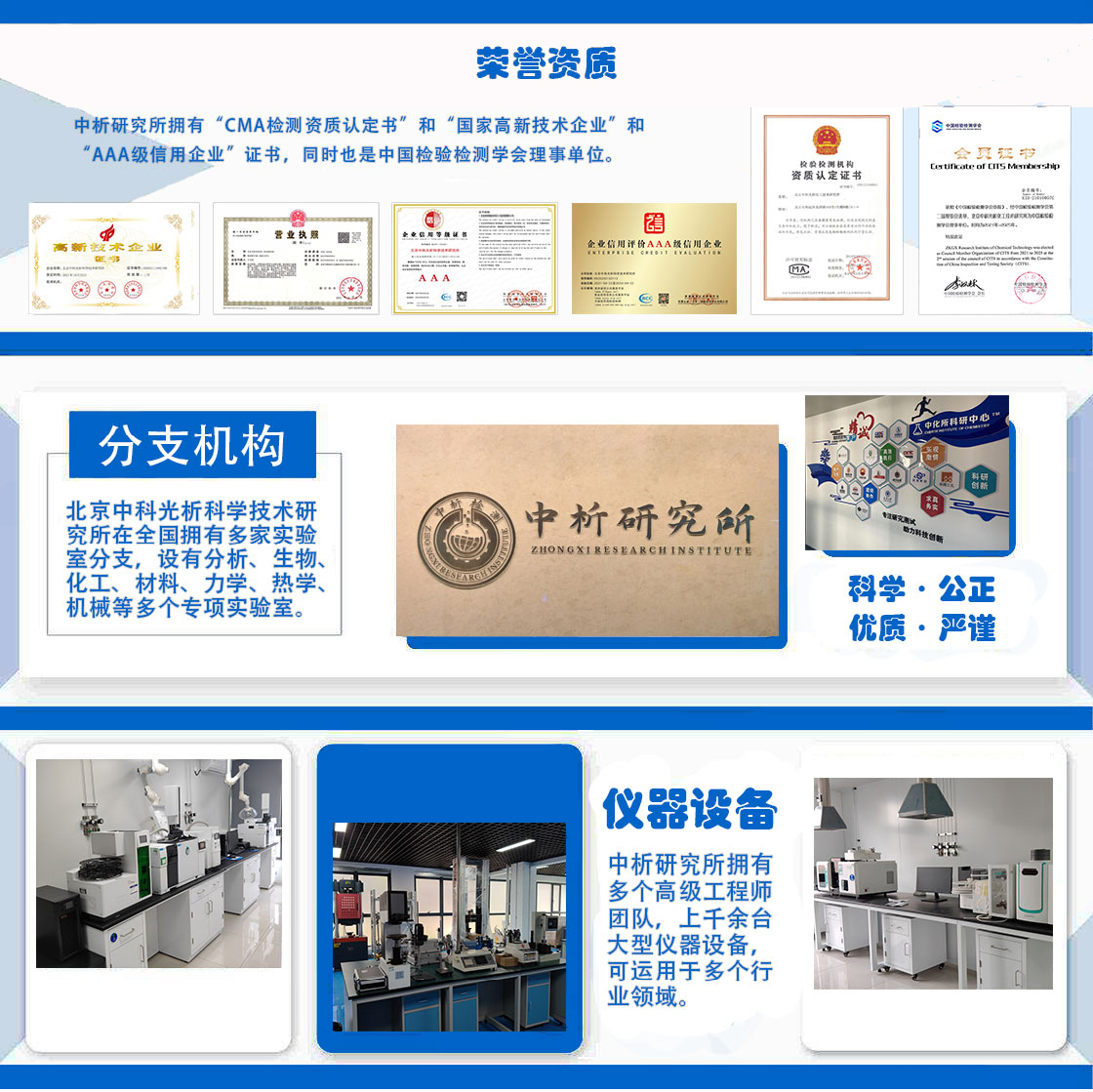
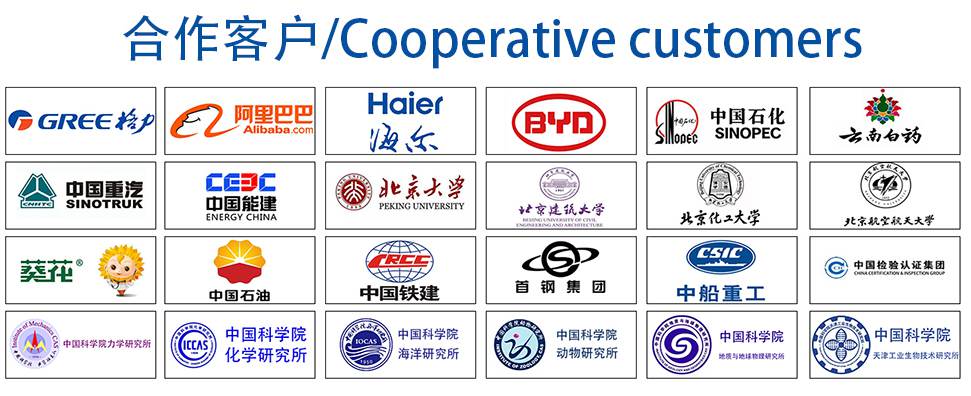
材料实验室
热门检测
276
233
208
217
215
220
230
223
233
233
220
219
222
219
213
210
227
212
224
218
推荐检测
联系电话
400-635-0567