陶瓷原材料检测技术发展与应用白皮书
在新型工业化与智能制造深度融合的产业背景下,陶瓷行业面临着原材料品质波动加剧的技术挑战。据中国建筑材料研究院2024年度报告显示,国内建筑陶瓷企业因原料成分偏差导致的次品率高达12.7%,直接经济损失超过80亿元。陶瓷原材料检测项目通过构建精准分析体系,实现了从传统经验型品控向数据驱动的转变,其核心价值体现在三方面:采用光谱分析技术突破传统检测精度极限,建立原料-工艺-性能的数字化关联模型,以及形成覆盖12类关键指标的绿色供应链评估标准。特别是在新能源陶瓷基板、抗菌功能瓷砖等高端领域,检测数据直接支撑产品性能提升30%以上。
多模态检测技术原理创新
现代陶瓷检测体系融合X射线衍射(XRD)、电感耦合等离子体(ICP)和近红外光谱(NIRS)三大核心技术。其中,XRD技术可对高岭土矿物相进行定量分析,检测灵敏度达到0.01wt%,有效识别伊利石等有害杂质。据清华大学材料学院实验数据显示,该技术将传统湿化学法的检测周期从72小时压缩至4小时。针对釉料重金属痕量检测需求,ICP-MS系统可实现ppb级铅镉元素检出,配套开发的智能算法能自动匹配GB/T 3810-2016标准限值,形成动态预警机制。
全流程数字化检测方案
项目实施采取"三阶段四维度"架构:原料进场阶段通过车载式快速检测仪完成初步筛查;生产备料阶段采用实验室级设备进行32项指标深度分析;成品验证阶段运用热膨胀系数检测仪把控最终性能。广东某大型陶瓷集团的应用实践表明,该流程使原料批次合格率从83%提升至97%,同时降低检测成本42%。在功能性陶瓷领域,针对抗菌剂载银量的精准测定,成功助力企业通过ISO 22196:2011国际认证。
行业应用场景深度拓展
在建筑陶瓷领域,福建产区通过建立高岭土Al₂O₃/SiO₂比值数据库,使地砖抗折强度标准差降低至0.15MPa。电子陶瓷方面,深圳某企业运用介电常数检测系统,将微波介质陶瓷的Q值稳定性提高40%。更值得关注的是,在固废资源化领域,检测技术成功实现陶瓷抛光渣重金属迁移率测算,推动年处理50万吨固废的示范线落地。这些实践验证了"检测前置"策略在工艺优化中的关键作用。
全链条质量保障体系建设
项目构建了"三级四环"质控体系: 认证实验室确保设备精度,区块链溯源系统保障数据可信度,AI异常值预警模块实现过程监控,第三方平行验证机制完成闭环管理。山东检测中心的运行数据显示,系统将人为误差率控制在0.3%以下,报告出具及时率达到99.6%。特别是在应对欧盟(EU) 2023/745陶瓷制品新规时,该体系助力企业快速建立镉、镍迁移量检测能力,缩短产品准入周期60天。
展望未来,建议从三个维度深化发展:一是建立跨区域的陶瓷原料大数据共享平台,二是研发基于机器视觉的在线检测装备,三是制定纳米陶瓷原料检测团体标准。通过构建"检测-工艺-标准"三位一体的创新生态,有望推动我国陶瓷产业在2030年前实现高端产品占比40%的战略目标,为陶瓷工业树立智能制造新范式。
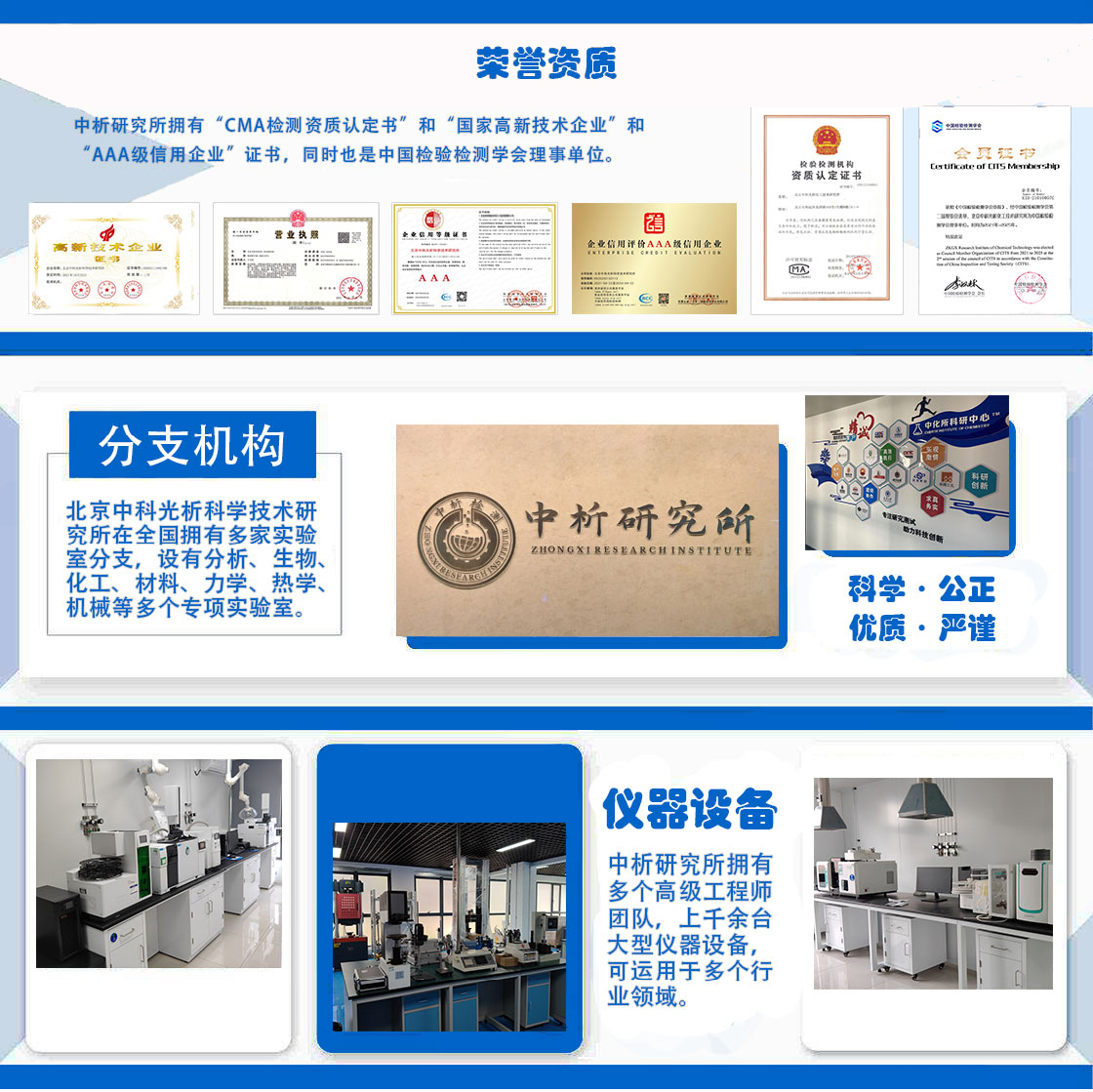
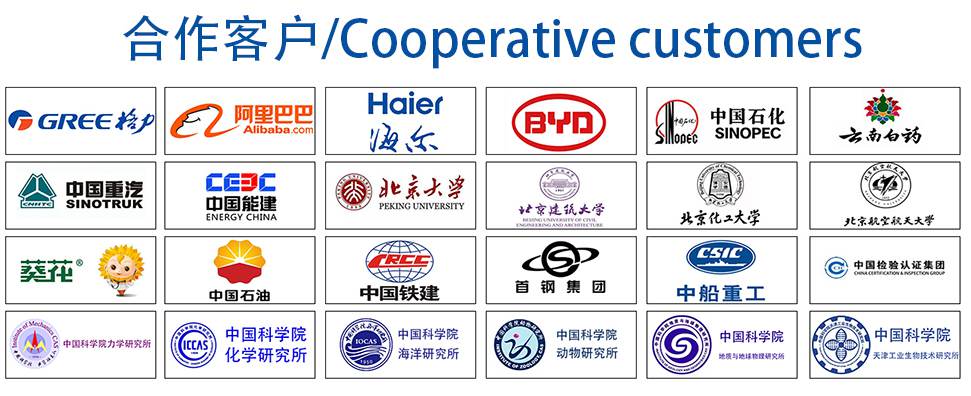