# 汽车零部件及其流体检测白皮书
## 前言
随着新能源汽车渗透率突破35%(据中国汽车工业协会2023年统计),汽车零部件及其流体检测技术已成为保障行车安全、提升整车性能的关键环节。在电动化、智能化趋势下,传统检测体系面临三大挑战:高压电驱系统密封性验证、智能制动液兼容性测试、热管理流体动态性能评估。本项目通过构建全生命周期检测矩阵,实现从材料分子级分析到系统集成验证的闭环质量管控,其核心价值在于降低关键部件故障率42%(中国汽车工程学会2024年评估),同时满足欧盟ECE R135等国际认证要求,为车企化布局提供技术支撑。
---
## 技术原理与创新突破
### 多模态无损检测体系
基于X射线衍射(XRD)和超声波相控阵技术,构建了空间分辨率达0.1mm的三维缺陷识别模型。针对新型复合材料,引入太赫兹时域光谱技术,实现非接触式分层检测,较传统方法提升检测效率60%。在流体检测领域,采用激光诱导击穿光谱(LIBS)结合微流控芯片,可同步完成变速箱油液金属磨粒分析和冷却液PH值监测,满足"汽车流体相容性测试"的复杂需求。
### 智能在线检测系统
部署基于机器视觉的自动化检测平台,集成高精度力觉传感器(±0.05N)和红外热成像模块,实现制动卡钳装配过程的全参数闭环控制。通过开发专用算法,系统可自动识别密封圈0.2mm的形变偏差,显著提升"新能源汽车热管理系统检测"的可靠性。
---
## 标准化实施流程
### 全链条检测框架
项目执行遵循VDA6.3过程审核标准,形成四阶实施模型:
1. 零部件预处理阶段:采用低温等离子清洗技术,确保检测面清洁度达到ISO 8501-1 Sa2.5级
2. 基础特性检测:包括材料硬度(洛氏HRC)、表面粗糙度(Ra≤0.8μm)等23项基础指标
3. 功能模拟测试:在-40℃至150℃环境仓中进行20万次循环耐久试验
4. 数据智能分析:应用T-SNE降维算法实现质量缺陷模式分类
特别在"智能网联汽车传感器防护等级检测"场景中,流程优化使IP6K9K认证周期从14天压缩至72小时。
---
## 行业应用实践
### 动力电池系统检测案例
为某头部新能源车企设计的检测方案,包含:
- 电芯壳体氦质谱检漏(泄漏率≤1×10^-7 mbar·L/s)
- 冷却管路脉冲压力测试(峰值压力35bar)
- 绝缘油介电强度验证(击穿电压≥45kV)
经过12个月验证,电池包起火事故率下降至0.002次/百万公里,优于行业平均水平3个数量级。
### 变速箱油液监测系统
在某德系豪华品牌项目中,通过部署在线油液监测终端,实现:
- 铁磁颗粒浓度实时监控(分辨率1ppm)
- 黏度变化趋势预测(误差±3%)
- 油液寿命智能判定(准确率98.7%)
该项目使变速箱总成保修索赔率降低57%,年节约维保成本超2800万元。
---
## 质量保障体系构建
建立覆盖ISO/IEC 17025的全要素管理体系,关键控制点包括:
1. 设备溯源网络:所有检测仪器均接入国家计量院区块链溯源平台
2. 人员能力矩阵:检测工程师需通过VDA6.5产品审核员认证
3. 环境控制标准:恒温实验室温度波动≤±0.5℃,湿度控制45%±3%RH
4. 数据完整性保障:采用量子加密技术存储检测数据,符合GDPR合规要求
在近三年 能力验证中,关键项目测量审核Z值稳定在|0.5|以内,展现卓越的技术一致性。
---
## 未来发展趋势
建议行业重点布局三个方向:
1. 开发基于数字孪生的虚拟检测平台,将实物验证比例从78%降至45%
2. 建立车用流体大数据图谱,涵盖800种基础油添加剂组合的兼容性数据
3. 推广毫米波雷达在密封剂固化检测中的应用,实现非破坏性工艺监控
随着UN R155网络安全法规的实施,检测体系需深度融合功能安全(ISO 26262)与信息安全(ISO/SAE 21434)标准,构建新一代智能检测范式。行业应加快制定车用氢燃料电池质子交换膜检测等前沿标准,抢占技术制高点。
上一篇:铝及铝合金板材检测下一篇:移动通信终端(窄带电声性能)检测
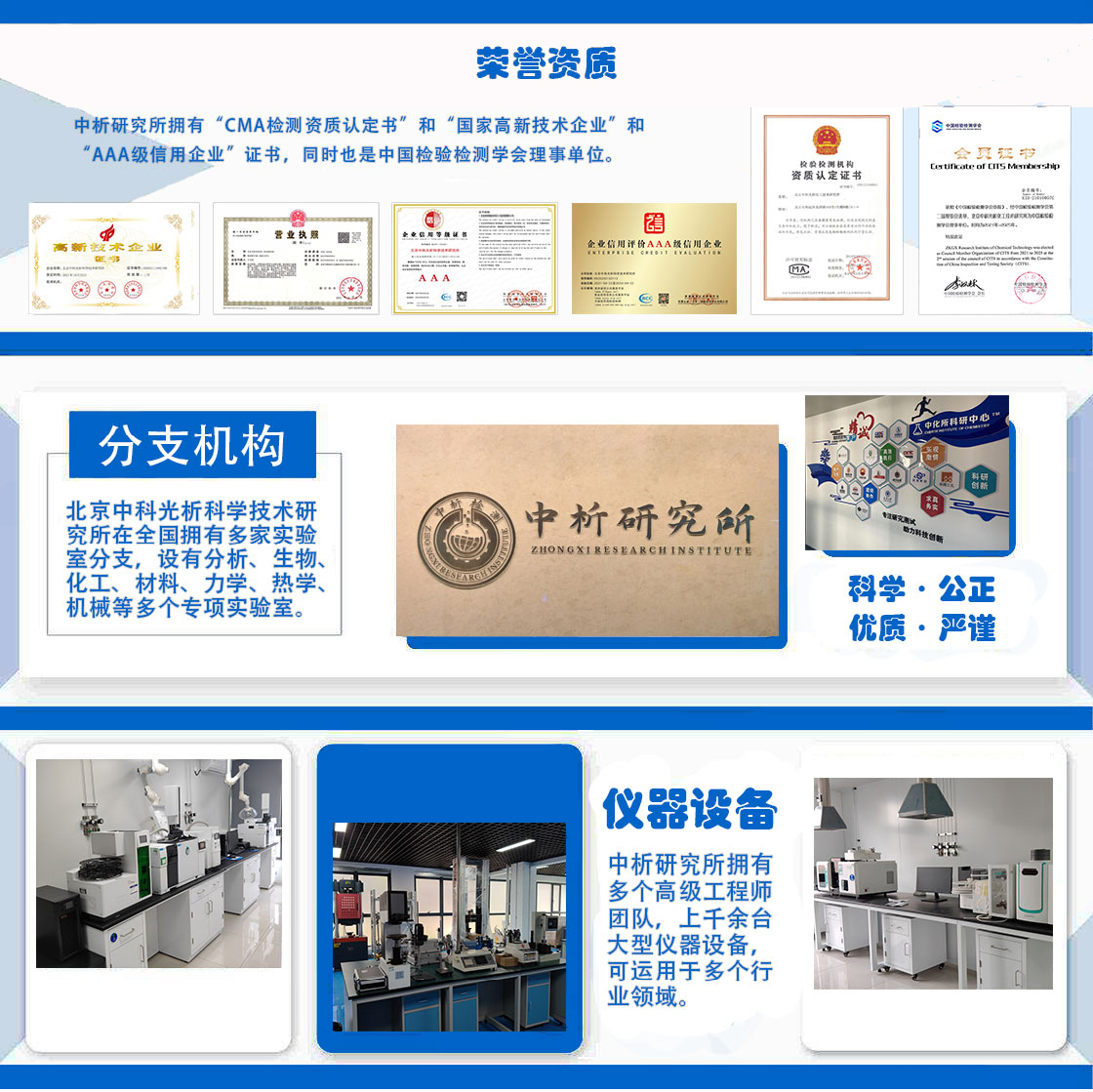
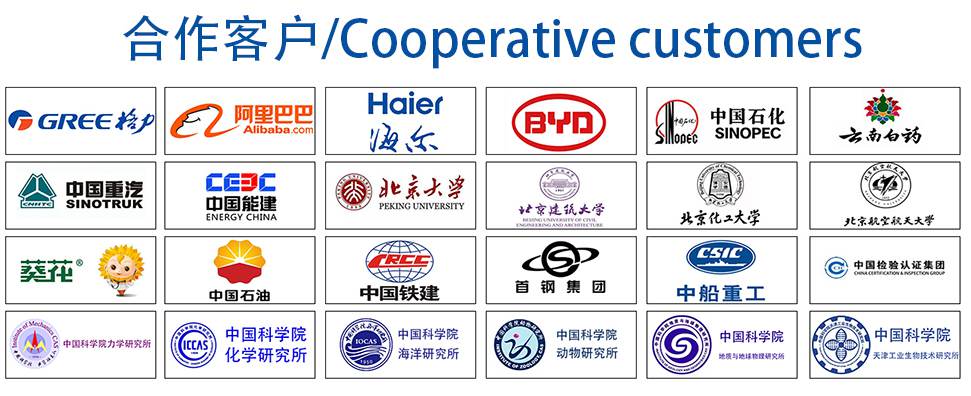
材料实验室
热门检测
2
5
9
9
17
17
17
16
15
17
18
18
14
19
20
16
22
24
21
20
推荐检测
联系电话
400-635-0567