铝及铝合金板材检测技术发展与应用白皮书
在碳中和战略推动下,铝材需求量持续攀升,据国际铝业协会2024年报告显示,交通运输领域铝合金用量较2020年增长42%,其中新能源汽车电池托盘、航空航天结构件等高端应用场景对材料性能提出更高要求。铝及铝合金板材检测作为产业链质量管控的核心环节,直接影响着产品安全性和使用寿命。通过建立系统化的检测体系,不仅能精准识别晶粒度异常、表面缺陷、力学性能偏差等关键质量问题,更可推动材料研发创新,助力企业实现每吨产品良率提升15%(中国有色金属工业协会,2023)。特别是在新能源汽车轻量化进程中,动力电池壳体用3003-H14铝合金的焊接完整性检测,已成为保障整车安全的核心技术壁垒。
多模态检测技术集成体系
现代铝合金板材检测采用"物理-化学-数字"三元融合技术架构,集成光谱分析、超声波相控阵、数字图像处理等齐全手段。其中,激光诱导击穿光谱(LIBS)技术可实现5μm级元素偏析检测,配合ASTM E1251标准建立的数据库,能够精确识别Mg、Si等合金元素的梯度分布。对于7075-T6航空板材的内部缺陷检测,相控阵超声以0.1mm分辨率定位夹杂物,较传统A超检测效率提升3倍。值得关注的是,基于深度学习的表面缺陷识别系统(DLS)在江苏某龙头企业已实现98.7%的划伤识别准确率,大幅降低人工漏检风险。
全生命周期质量控制流程
完整的检测流程涵盖原料验收、过程监控、成品检验三个阶段。某轨道交通装备制造企业的实践表明,实施GB/T 3880标准的全项检测后,铝板折弯开裂率从1.2%降至0.3%。具体实施中,首道工序采用X射线荧光光谱仪进行来料成分验证;在热轧工序部署红外热像仪实时监测温度均匀性;最终制品阶段运用电子背散射衍射(EBSD)技术分析晶粒取向,确保各向异性指标符合EN 485-2标准。全过程数据通过MES系统集成,形成可追溯的质量档案。
行业典型应用场景解析
在航空航天领域,中航工业某研究院针对2219铝合金焊接接头的相控阵超声检测方案,成功将火箭燃料贮箱漏检率控制在十万分之三以下。新能源汽车领域,宁德时代采用的6061-T6铝合金电池托盘微裂纹检测系统,通过涡流阵列技术实现0.05mm级缺陷捕捉,保障电池模组结构完整性。建筑幕墙行业典型案例显示,珠海某超高层项目通过实施应力腐蚀敏感性(SCC)测试,使铝板幕墙服役寿命延长至40年,远超行业平均25年标准。
四维质量保障体系构建
行业领先企业已建立包含设备、人员、标准、数据的立体化质控网络:其一,检测设备实行 实验室三级校准体系,关键仪器每日进行GR&R分析;其二,检测人员需通过NADCAP认证并完成年度120学时继续教育;其三,执行ASTM B209、ISO 6892-1等17项国际标准;其四,搭建质量大数据平台,某上市公司通过分析十年检测数据,成功将5052-H32铝板屈服强度波动范围缩小18%。
展望未来,建议重点发展三方面能力:一是开发基于量子传感的纳米级缺陷检测技术,应对6xxx系铝合金汽车板更严格的成型性要求;二是建立覆盖全国的区域性检测认证中心,据测算可降低中小企业检测成本35%;三是推动检测标准国际化互认,特别是在"一带一路"沿线国家推广GB/T 3191标准的应用。通过构建智能检测生态系统,铝加工行业有望在2025年前实现质量损失率降低至0.8%以下,支撑我国高端制造转型升级战略。
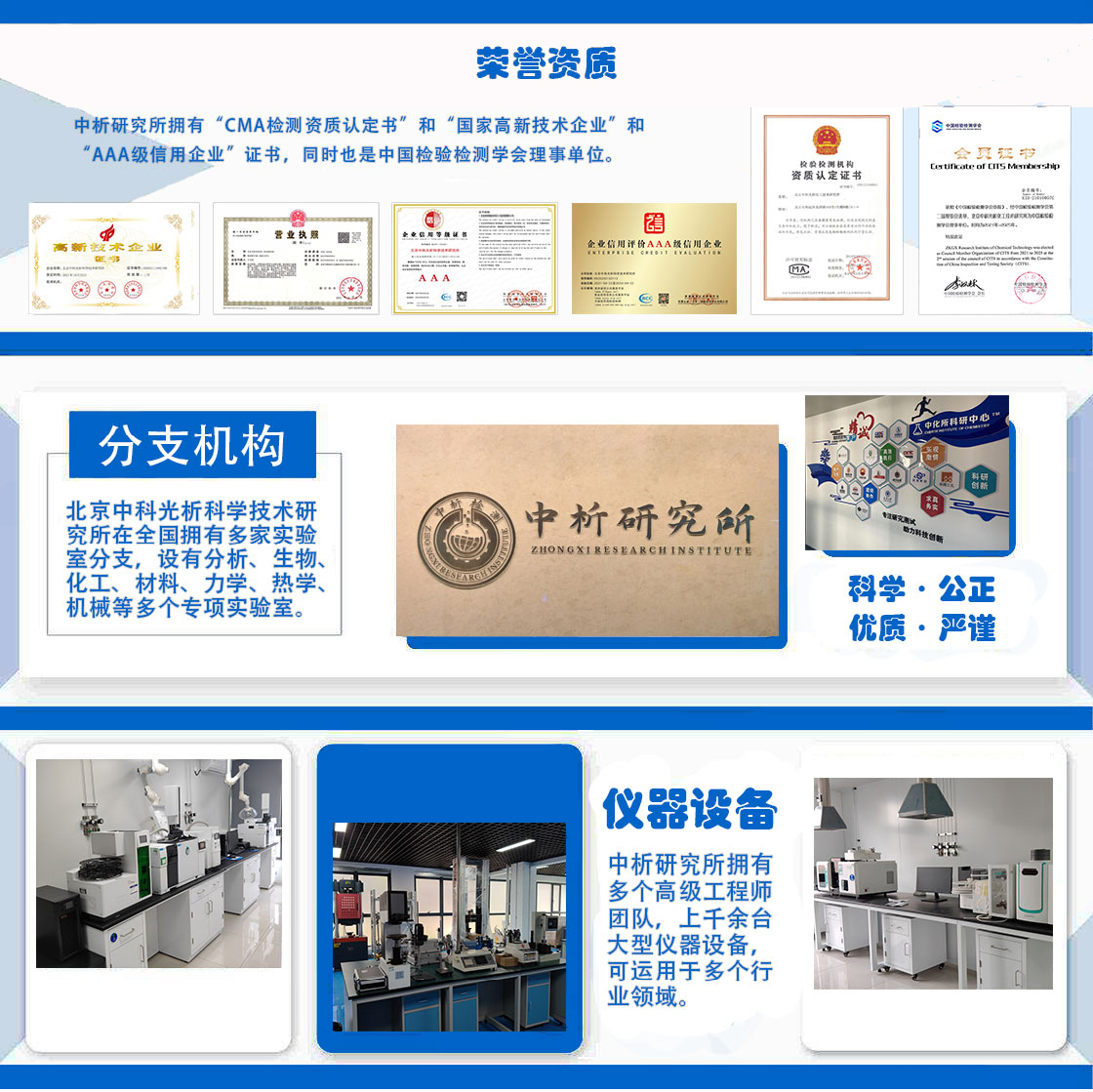
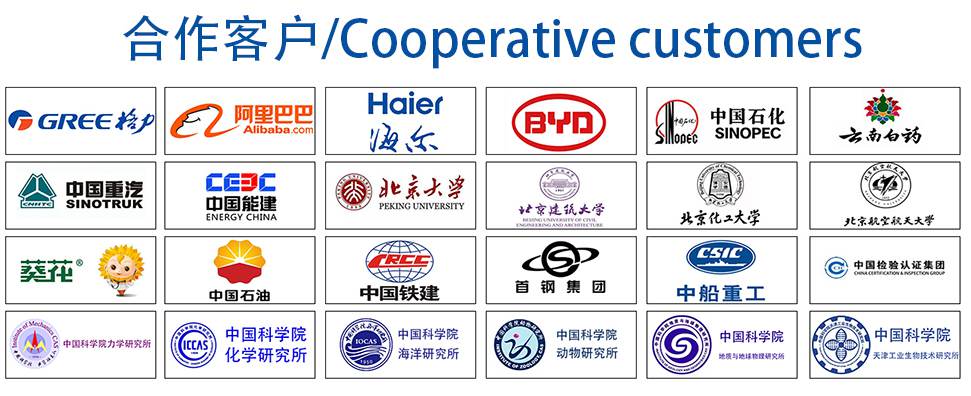