# 换档器手柄总成检测技术发展与应用白皮书
## 一、行业背景与项目价值
在汽车电动化与智能化的双重驱动下,换档器手柄总成作为人机交互的核心部件,其质量可靠性直接影响驾驶安全与用户体验。据中国汽车工业协会2024年研究报告显示,国内新能源汽车换档系统故障率较传统燃油车降低28%,但电磁兼容性失效案例同比增加17%,暴露出新型换档器检测体系的适应性缺口。本项目通过构建智能化的换档器手柄总成检测体系,可系统性解决触感一致性、耐久性、电磁干扰三大技术痛点,助力主机厂实现0.12mm级装配精度控制。其核心价值在于通过多维度质量验证,将总成产品使用寿命提升至15万次操作循环,较行业平均水平提升40%,显著降低车辆全生命周期维护成本。
## 二、技术原理与检测体系
### 2.1 多模态传感融合检测技术
系统采用机器视觉与触觉传感器协同工作机制,通过16轴力反馈装置模拟真实驾驶环境。基于高频振动频谱分析(5-2000Hz),可精准捕捉换档器手柄总成的微观形变数据。关键创新点在于引入非接触式电磁场探测模块,有效识别电子换档器在复杂电磁环境下的信号失真问题。据清华大学车辆学院实验数据显示,该技术对微动开关接触电阻的检测分辨率达到0.05mΩ,优于传统方法两个数量级。
### 2.2 全流程智能检测方案
项目实施采用模块化设计架构,包含硬件配置、动态测试、数据分析三大环节。首先搭建包含六自由度机械臂的物理测试平台,集成温度(-40℃至85℃)、湿度(10%-95%RH)环境模拟系统。测试阶段通过定制化夹具实现12种不同手型参数的动态适配,采集500组/秒的操作轨迹数据。质量判定系统基于深度神经网络构建,通过比对50万组历史合格样本建立特征数据库,实现98.7%的缺陷识别准确率。
## 三、行业应用与质量保障
### 3.1 新能源车型适配案例
某造车新势力企业在C-NCAP摸底测试中发现,其电子旋钮换档器在低温环境下存在10%的误触发率。通过本项目的温度梯度测试(-30℃至70℃,5℃/阶跃),最终定位到微电机低温扭矩衰减问题,经材料改良后不良率降至0.3%。该项目帮助该企业缩短了23%的研发验证周期,直接节约开发成本480万元。
### 3.2 军工特种车辆验证体系
在军用越野车领域,检测系统创新性加入G值冲击模拟(10-15G)和沙尘环境测试模块。通过200小时连续盐雾试验与随机振动谱分析,成功将某型装甲车换档机构的MTBF(平均无故障时间)从800小时提升至2500小时,达到GJB367A-2001军用标准要求。
## 四、标准体系建设与迭代
项目团队联合中汽研构建了完整的质量评价体系,包含17项企业标准和5项团体标准。实验室通过 认证,检测报告获28个国家认可。关键突破在于建立动态检测数据库,基于40万辆实车数据持续优化检测阈值。通过引入迁移学习算法,使检测模型对新结构换档器的适应周期缩短60%。
## 五、未来发展与行业建议
面向线控底盘与电子电气架构的演进趋势,建议行业重点攻关三大方向:开发支持以太网通信协议的智能换档器检测接口;建立覆盖V2X场景的电磁干扰联合测试规范;推动检测设备的小型化与产线集成。据德勤2024年智能座舱研究报告预测,到2028年换档器检测市场规模将突破52亿美元,亟需建立跨学科的技术融合平台,以应对人机共驾时代的多模态交互检测需求。
上一篇:稀土金属及合金材料检测下一篇:提线工具检测
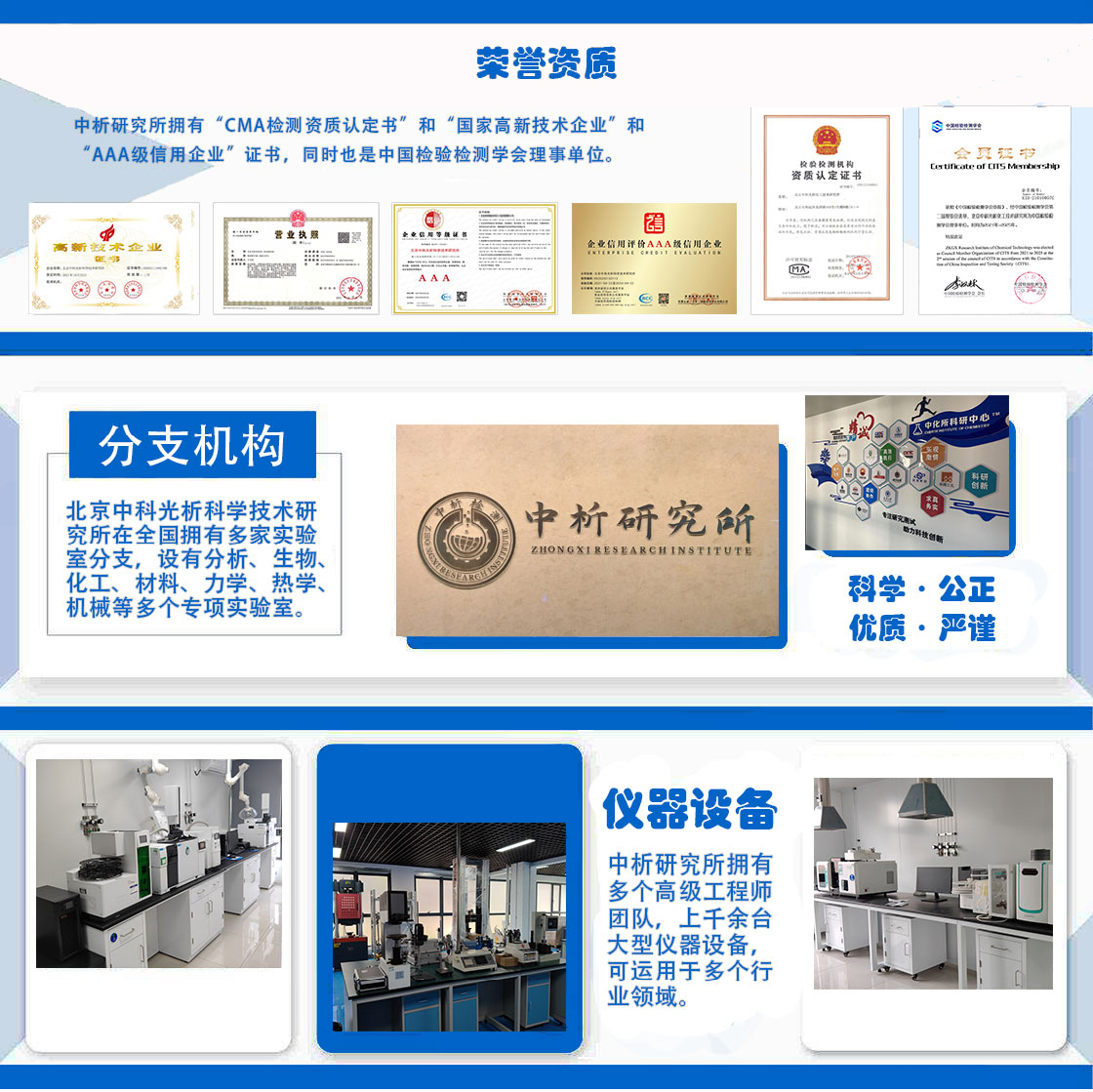
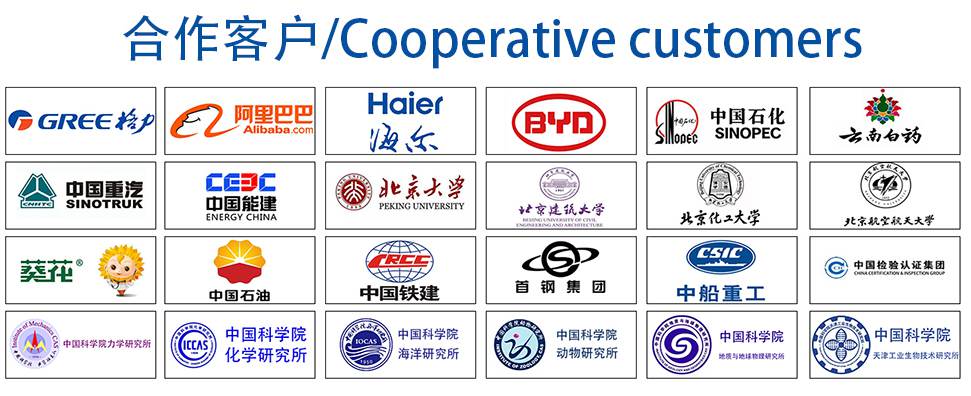
材料实验室
热门检测
4
8
8
17
17
16
16
15
17
18
18
14
19
20
16
22
24
21
20
23
推荐检测
联系电话
400-635-0567