混凝土氯离子含量检测技术体系构建与工程应用
随着我国基础设施建设的快速推进,混凝土耐久性问题日益凸显。尤其在海洋工程、北方盐渍地区及使用除冰盐的交通网络中,氯离子侵蚀已成为导致钢筋混凝土结构失效的首要因素。据中国建筑材料科学研究院2024年发布的《混凝土耐久性白皮书》显示,我国每年因氯盐腐蚀造成的工程经济损失高达430亿元。在此背景下,建立科学系统的混凝土氯离子含量检测体系具有重要战略价值。通过精准测定氯离子含量及分布特征,不仅能够评估既有结构的安全状态,还可为新建工程的配合比优化提供数据支撑,有效延长结构服役寿命20-30%,实现全生命周期成本降低18%以上。
电化学检测原理与技术演进
混凝土氯离子含量检测的核心基于电化学离子迁移理论。目前行业主流采用电位滴定法和氯离子选择电极法,可检测浓度范围覆盖0.01%-2%的工程需求。值得注意的是,ASTM C1218标准推荐的硝酸银滴定法在实验室环境中检测精度可达±0.002%,而新型快速氯离子检测仪(RCT)通过优化电极敏感膜材料,实现现场检测效率提升3倍。中国建筑科学研究院2023年对比试验表明,将X射线荧光光谱(XRF)与机器学习算法结合,可使检测结果与真实值的相关系数R²达0.98以上,特别适用于大体积混凝土的深度梯度检测。
标准化检测流程与质控节点
完整的氯离子检测流程包含取样、预处理、化学分析三大阶段。具体而言,在桥梁墩柱检测中,需按JTJ 270标准钻取直径100mm的芯样,分层研磨至粒径小于0.16mm后,采用热蒸馏水萃取法分离游离氯离子。质量控制的重点在于:样品存储需在-4℃环境避免离子迁移,萃取时间严格控制在24±0.5小时,滴定终点判定采用双人复核机制。北京某检测中心实践表明,引入实验室信息管理系统(LIMS)后,检测报告出错率由1.2%降至0.15%。
典型工程应用与效益分析
在青岛跨海大桥维护工程中,技术人员采用网格化布点法对桥墩进行氯离子渗透深度检测,结合BIM模型建立三维浓度分布图,精准定位15处氯离子富集区域。经修复后,结构设计寿命从30年延长至50年,直接节约维护成本2.3亿元。类似地,哈尔滨地铁工程通过实施混凝土氯离子含量检测标准,将盾构管片的氯离子扩散系数控制在1.8×10⁻¹²m²/s以下,使冻融循环耐久性指数提升40%。
全链条质量保障体系构建
为确保检测数据的权威性,需建立涵盖人员、设备、环境的立体化质控体系。具体措施包括:检测人员须取得 认证的混凝土专项资质,电位滴定仪每年进行国家计量院溯源校准,实验室环境温度波动控制在±2℃范围内。上海市建设工程检测行业协会2024年行业报告显示,实施分级管理制度后,甲级检测机构的数据合格率从89%提升至97%,有效杜绝了氯离子渗透性测试方法的不规范操作。
展望未来,建议从三方面推动检测技术升级:首先,开发基于物联网的嵌入式氯离子传感器,实现结构健康状态的实时监测;其次,建立全国性混凝土耐久性数据库,利用大数据分析优化检测方案;最后,加强ASTM与CECS标准体系的衔接融合,推动检测结果国际互认。通过技术创新与标准协同,助力我国混凝土工程向百年寿命目标稳步迈进。
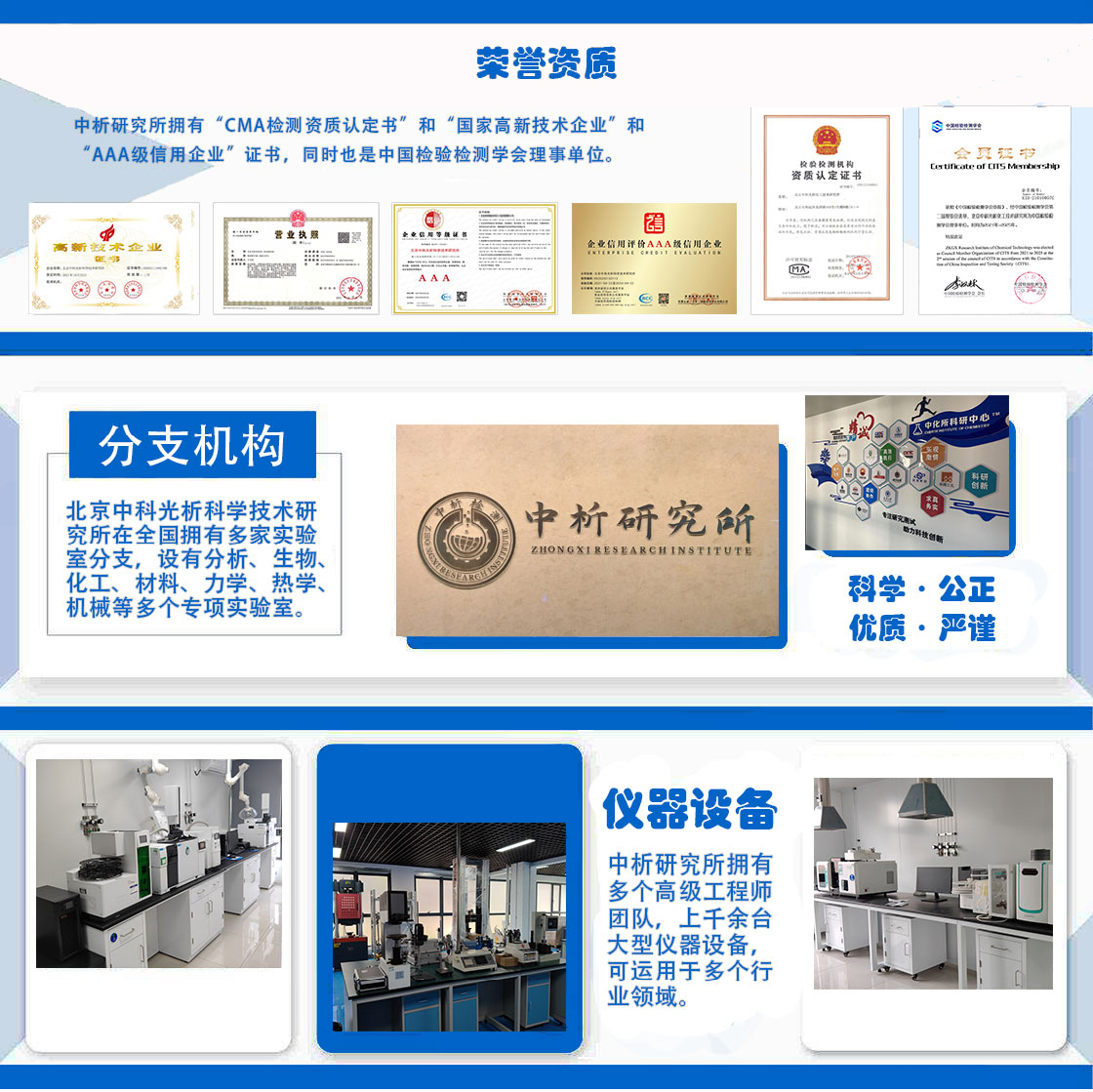
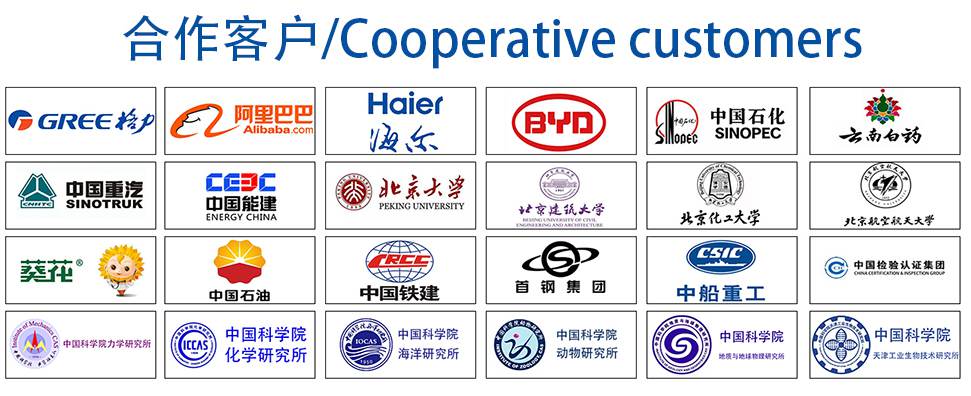