焊剂检测的重要性与技术要点
焊剂作为焊接工艺中的关键辅助材料,其质量直接影响焊接接头的强度、耐腐蚀性和电气性能。随着工业制造对焊接质量要求的日益严苛,焊剂检测已成为航空航天、电子设备、汽车制造等领域的核心质量控制环节。焊剂的主要功能包括去除金属表面氧化物、防止焊接过程中二次氧化、改善熔融金属流动性等,但其成分残留或性能不达标可能引发虚焊、焊点腐蚀、绝缘性能下降等问题。因此,通过系统性检测可有效评估焊剂的清洁能力、活性强度、残留物危害性等关键指标,确保符合GB/T 15829、IPC J-STD-004等行业标准。
核心检测项目解析
1. 化学成分分析
使用X射线荧光光谱仪(XRF)或电感耦合等离子体发射光谱仪(ICP-OES)测定焊剂中卤素(Cl、F)、金属离子(Na⁺、K⁺)、有机酸等活性成分含量。重点检测卤素含量是否超出ISO 9454-1规定的0.1%限值,避免造成设备腐蚀。
2. 物理性能测试
通过旋转黏度计测量液态焊剂黏度(25℃条件下通常需控制在35-55 mPa·s),比重计检测密度偏差(允许波动±0.05g/cm³),以及扩展率试验评估焊剂铺展能力(目标值>80%)。
3. 残留物检测
采用离子色谱法测定氯离子、硫酸根离子残留量(IPC-TM-650标准要求Cl⁻<1.56μg/cm²),表面绝缘电阻测试评估残留物对电路板的影响(>1×10⁸Ω为合格),并通过热重分析(TGA)验证高温分解特性。
4. 腐蚀性评估
执行铜镜试验(依据JIS Z3197)观察铜箔腐蚀程度,同时进行168小时盐雾试验(ASTM B117标准)检验焊后金属件的抗腐蚀性能,要求锈蚀面积占比<5%。
5. 电气性能验证
采用四探针法测量焊点接触电阻(波动值需<5%初始值),配合TDR时域反射仪检测高频信号传输完整性(阻抗偏差控制在±10%以内)。
检测实施要点与标准参照
现代焊剂检测需结合离线实验室分析与在线监测技术,如引入近红外光谱(NIR)实时监控产线焊剂浓度。检测过程应严格参照IPC-J-STD-004B(电子行业)、AWS A5.1(通用焊接)等标准体系,对无铅焊剂还需符合RoHS 2.0的镉、铅、汞等重金属限值要求。建议生产企业建立涵盖原材料入场检验、生产过程抽检、成品全检的三级检测体系,并定期进行第三方权威机构认证。
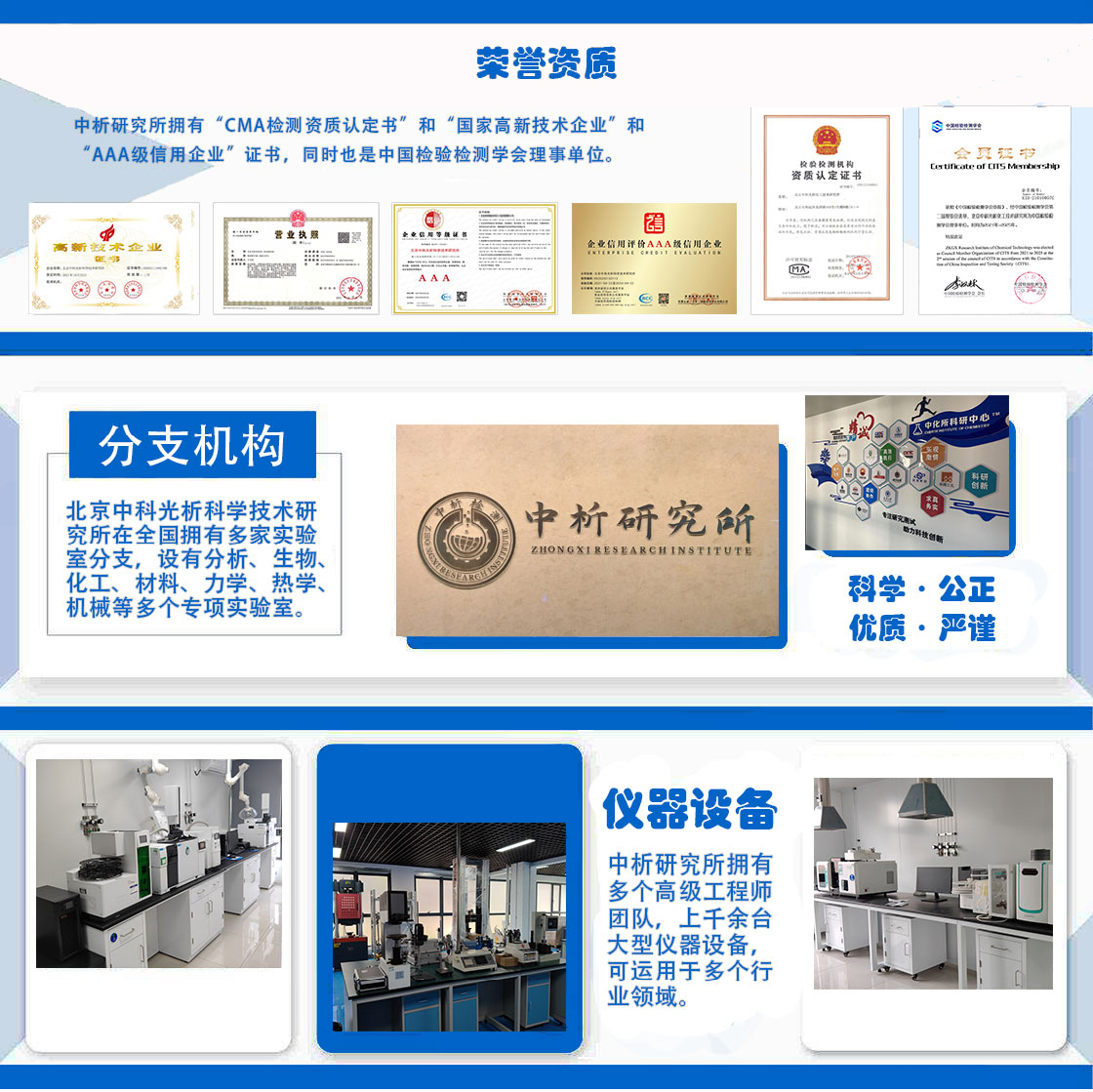
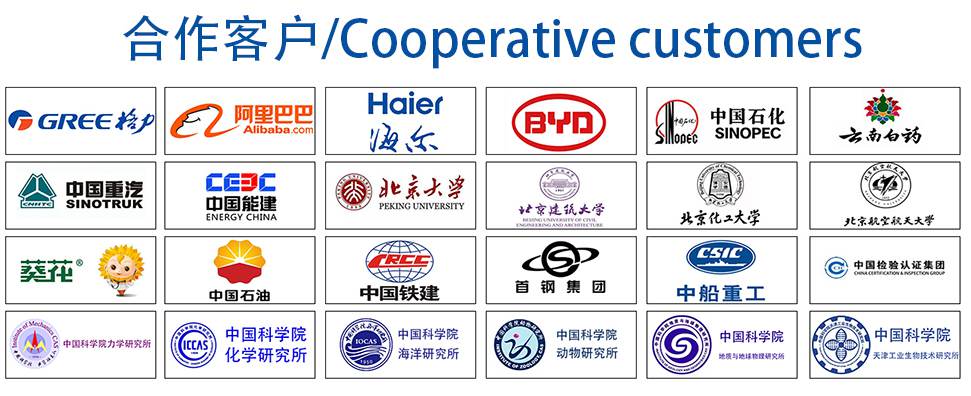