冷镦和冷挤压钢检测的重要性与核心项目
冷镦和冷挤压是金属加工中常用的成型工艺,广泛应用于紧固件、汽车零部件、机械配件等产品的生产。这两种工艺通过高压力使金属材料在常温下发生塑性变形,从而形成所需形状。然而,由于加工过程中材料需承受极大的应力和形变,原材料性能的稳定性和质量直接影响最终产品的强度、精度及使用寿命。因此,冷镦钢和冷挤压钢的检测成为确保加工工艺可行性和产品质量的关键环节。
核心检测项目及技术要求
1. 化学成分分析
冷镦钢和冷挤压钢的化学成分直接影响其加工性能和机械性能。检测需通过光谱分析仪(如OES)或化学滴定法,精确测定碳(C)、硅(Si)、锰(Mn)、磷(P)、硫(S)等元素的含量。低磷、低硫的洁净钢可减少冷加工裂纹风险,而碳含量需根据产品强度要求调整。例如,中碳钢(如35#、45#)常用于高强度紧固件,低碳钢(如SWRCH22A)则适合复杂变形零件。
2. 机械性能测试
包括抗拉强度、屈服强度、延伸率和断面收缩率的测定。冷镦钢需具有较高的塑性(延伸率≥20%)和良好的断面收缩率(≥60%),以确保加工时不易开裂。硬度测试(如洛氏硬度HRB)可快速评估材料加工硬化倾向,通常要求硬度值在75-95 HRB范围内。
3. 表面质量与缺陷检测
钢材表面裂纹、折叠、划痕或氧化皮会直接影响冷镦/挤压过程中的模具寿命和成品合格率。检测方法包括目视检查、磁粉探伤(MT)或涡流检测(ECT)。对于高端应用,需使用显微镜或扫描电镜(SEM)观察表面微观缺陷。
4. 冷镦适应性试验
通过实际模拟冷镦工艺(如顶锻试验),观察材料在压缩变形时的开裂倾向。试样在特定压缩比(如1/3或1/2高度压缩)下不应出现裂纹。此外,还需评估材料的冷作硬化曲线,优化加工参数。
5. 金相组织分析
通过金相显微镜观察钢材的晶粒度、带状组织及非金属夹杂物分布。晶粒度需控制在5-8级(ASTM标准),避免粗大晶粒导致塑性下降。带状组织应小于2级,夹杂物等级需满足GB/T 10561标准中B类≤1.5级的要求。
6. 尺寸与形状公差检测
使用卡尺、千分尺或光学测量仪对线材直径、椭圆度及直线度进行测量。以Φ5.5mm冷镦钢线材为例,直径公差需控制在±0.05mm以内,椭圆度不超过0.03mm,以确保送料稳定性。
检测标准与质量控制
冷镦钢检测需遵循GB/T 6478《冷镦和冷挤压用钢》、ISO 4954《冷锻钢》等标准。企业应建立从原料入库到成品出厂的全流程检测体系,结合SPC统计过程控制技术,对关键参数(如硬度波动、夹杂物含量)进行实时监控。通过严格的质量控制,可降低废品率10%-30%,延长模具寿命2-3倍,显著提升生产效益。
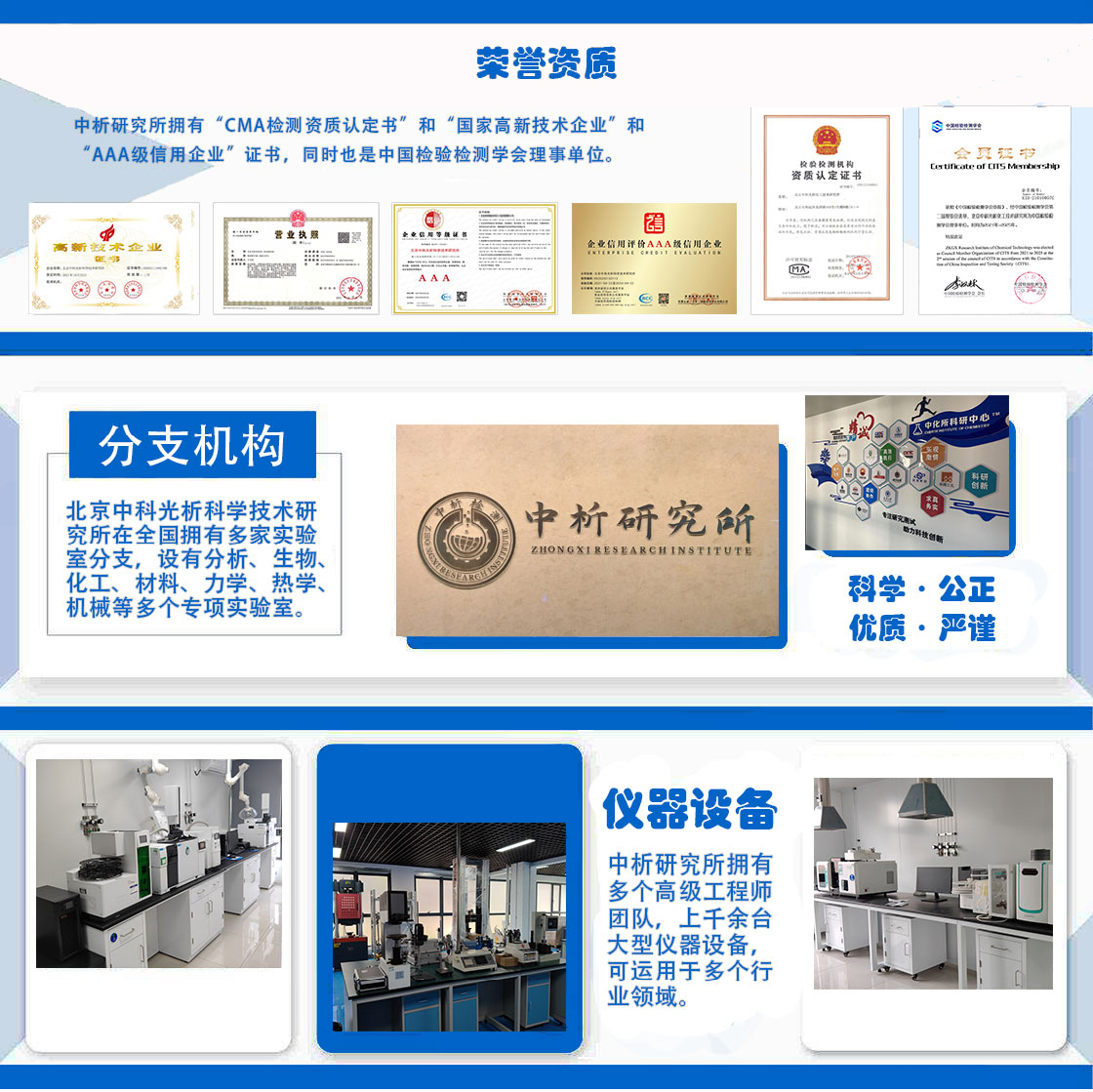
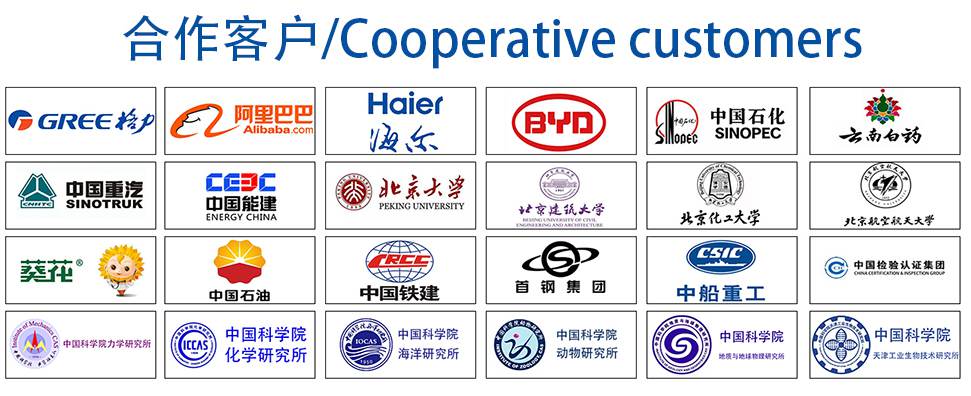