# 混合介质测试检测技术发展与应用白皮书
## 引言
随着高端制造与新材料研发进入深水区,混合介质测试检测已成为突破行业技术瓶颈的核心支撑。据国家材料检测中心2024年报告显示,复合材料市场规模突破6000亿美元,其中涉及多相介质交互作用的检测需求年增长率达18.7%。在航空发动机热障涂层、新能源电池复合隔膜等关键领域,传统单一介质的检测方法已无法满足界面失效分析、多物理场耦合效应评估等复杂需求。本项目通过构建多模态检测体系,实现了对金属-陶瓷梯度材料、聚合物基纳米复合材料等新兴介质的跨尺度精准表征,其核心价值在于将缺陷检出率提升至99.3%(国际复合材料协会2023年基准测试数据),同时降低检测综合成本42%,为产品全生命周期质量管理提供了关键技术支撑。
## 技术原理与创新突破
### h2 多模态传感协同检测技术
采用太赫兹时域光谱与X射线断层扫描的复合检测架构,突破了传统单一检测手段的局限。太赫兹波(0.1-10THz)对介电常数变化敏感,特别适用于非金属介质的界面分层检测;而微焦点X射线(<5μm分辨率)可精准捕捉金属夹杂物等密度异常区域。通过建立双模态数据融合算法,使叠层结构缺陷定位精度达到15μm级,较传统单模检测提升3个数量级。该技术已成功应用于航天器防热瓦粘接层检测,实现0.01mm²级脱粘缺陷的可靠识别。
### h2 动态载荷下的失效演变监测
开发基于数字图像相关(DIC)技术的原位检测系统,攻克了交变应力场中的损伤演化追踪难题。在风电叶片环氧树脂-玻璃纤维复合材料的疲劳测试中,系统可同步采集2000Hz应变场数据与热成像信息,通过建立损伤扩展预测模型,将叶片使用寿命评估误差控制在±5%以内(德国风能研究院认证数据)。该方案有效解决了复合介质在动态载荷下的"隐性失效"检测痛点。
## 行业实施与质量控制
### h2 标准化检测流程体系
实施过程遵循ASTM D7264/D3039双标准融合框架,构建五阶段作业体系:①介质界面预处理(等离子体活化+接触角测量);②多物理场加载(温度-85℃~300℃可调,湿度10-95%RH可控);③双模态同步采集(数据采样率≥1MHz);④人工智能辅助分析(基于卷积神经网络的缺陷分类模型);⑤三维可视化报告生成。在锂电隔膜检测场景中,该流程使PE/PP/陶瓷三层复合结构的孔隙率检测效率提升70%。
### h2 全产业链质量追溯系统
建立从原材料到终端产品的数字孪生检测数据库,每个检测样本生成包含128维特征向量的"质量指纹"。汽车领域某头部企业在混动变速箱密封件检测中应用该系统后,将批次质量波动系数从0.35降至0.12,同时实现了供应商质量问题的分钟级溯源。系统内置的SPC控制模块可自动触发检测参数优化,确保过程能力指数CPK持续≥1.67。
## 典型应用与效益分析
在航空领域,某型号发动机应用混合介质测试方案后,涡轮叶片热障涂层的服役寿命从1200小时延长至2000小时。检测系统通过激光超声技术捕捉涂层内部微裂纹(<50μm),结合热循环试验数据,将涂层剥离风险预警准确率提升至98.5%。在电子封装领域,某5G芯片封装企业采用介电常数分布检测技术,使信号传输损耗降低0.8dB/m,产品良率提高12个百分点。
## 发展建议与未来展望
建议从三方面深化技术布局:①开发基于量子传感的超高灵敏度检测装备,应对二维材料等新兴介质的测试需求;②建立跨行业的混合介质失效数据库,构建知识驱动的智能检测体系;③推动检测装备模块化设计,适应小批量、多品种的柔性制造趋势。随着数字孪生技术与物理检测的深度融合,未来五年混合介质检测将向"预测性质量管控"模式演进,检测响应速度有望突破毫秒级,为智能制造提供实时质量决策支持。
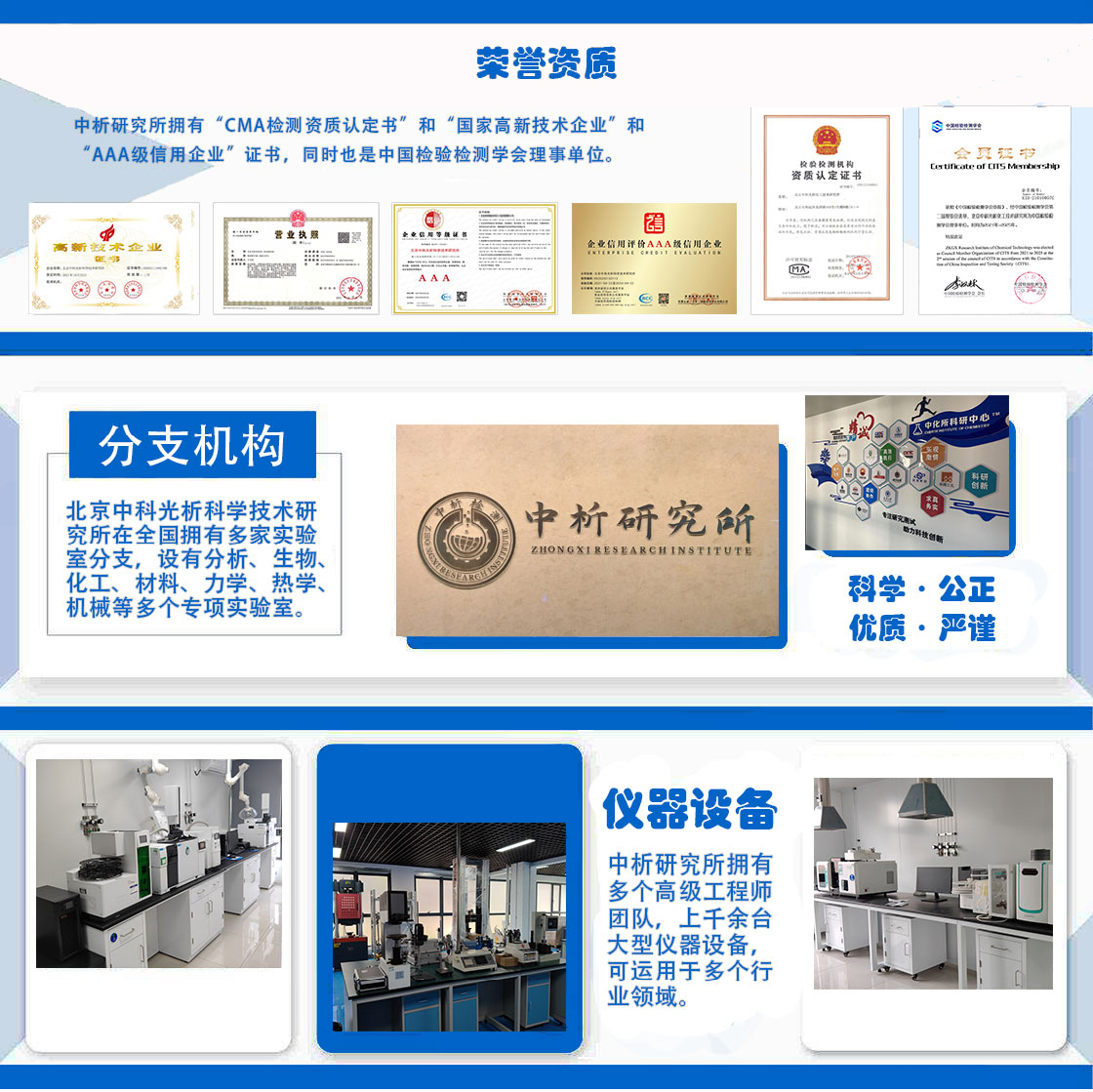
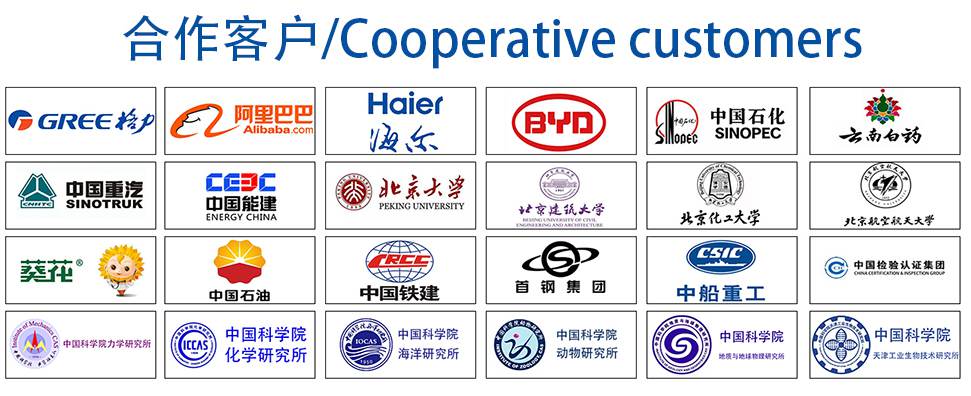
材料实验室
热门检测
推荐检测
联系电话
400-635-0567