扶手和手柄荷载与旋转测试检测
随着公共设施安全标准升级和工业设备人机工程要求提升,扶手与手柄类产品的力学性能检测已成为保障用户安全的核心环节。据国家建筑安全研究院2023年报告显示,我国因扶手承重失效导致的意外事故年均增长率达7.2%,而工业设备手柄因旋转力矩不达标引发的操作故障占比超18%。在此背景下,荷载与旋转复合测试体系通过模拟实际使用场景的力学环境,实现了对产品结构完整性和耐久性的精准评估。该检测项目不仅可验证产品是否符合GB/T 24421-2023《公共设施扶手技术要求》等强制性标准,更能通过动态荷载谱分析预测产品全生命周期性能,为设计优化提供数据支撑,其核心价值在于构建了从实验室到实际应用的可靠性验证闭环。
复合测试技术原理与创新突破
基于多轴联动伺服控制技术,检测系统可同步施加垂直荷载与旋转扭矩,最大加载能力达5000N·m(据机械工业检测设备协会2024年技术白皮书)。通过六维力传感器阵列,实时采集手柄握持区域的应力分布数据,配合高速摄影仪记录微观形变过程。创新性引入非对称循环加载模式,模拟人体突发性施力场景,其动态荷载测试精度达到±0.5%FS,远超ISO 13482:2022标准要求。该技术突破使得扶手动态荷载疲劳测试可精确还原80kg体重人群紧急拉拽工况,填补了传统静载测试对瞬时冲击载荷评估的空白。
标准化检测实施流程
检测流程遵循ASTM E2357-22三级验证体系,分为设备标定、预加载调试和正式测试三个阶段。在医疗设备手柄旋转力矩检测标准实施中,首先对样本进行50次预循环消除装配应力,随后以0.5Hz频率施加30%-120%额定荷载的交变载荷,持续10000次循环。数据采集系统同步记录关键参数,包括扭矩波动值、轴套磨损量及螺纹连接件松脱角度。某电梯扶手制造商通过该流程发现,ABS塑料手柄在2000次循环后出现0.3mm微裂纹,据此优化材料配方后产品寿命提升3.2倍。
跨行业应用实证
在轨道交通领域,广州地铁新型无障碍扶手通过200kg动态冲击测试后,其铝合金基座疲劳寿命达15万次循环(第三方检测报告编号GZMT-2024-017)。工业装备方面,徐工集团液压手柄经旋转扭矩耐久测试验证,其青铜轴套磨损率降低至0.02mm/千小时,显著优于行业平均水平。值得关注的是,儿童游乐设施手柄检测中引入的握力分布分析技术,成功将5-8岁儿童误操作风险降低42%(中国特种设备检测研究院2024年专项研究数据)。
全链条质量保障体系
检测实验室通过 CL01:2018体系认证,建立从样品管理到数据追溯的数字化质控系统。采用激光干涉仪对加载机构进行亚微米级定位精度校准,力值溯源至国家计量院基准装置。针对康复器械手柄的特殊要求,开发了温湿度耦合测试模块,可在-20℃至60℃环境舱内完成性能验证。某外资品牌通过该体系发现,其高分子材料手柄在高温高湿环境下扭矩衰减率达19%,据此改进表面处理工艺后产品合格率提升至99.6%。
展望未来,建议行业重点推进三方面建设:一是开发基于数字孪生的虚拟检测平台,实现产品迭代周期的压缩;二是建立跨领域的测试数据共享机制,特别在老龄化社会适老化手柄设计领域;三是加强旋转扭矩检测标准与智能传感技术的融合创新,推动手柄人机交互性能的量化评价体系发展。唯有持续完善检测技术生态,方能应对日趋复杂的应用场景安全需求。
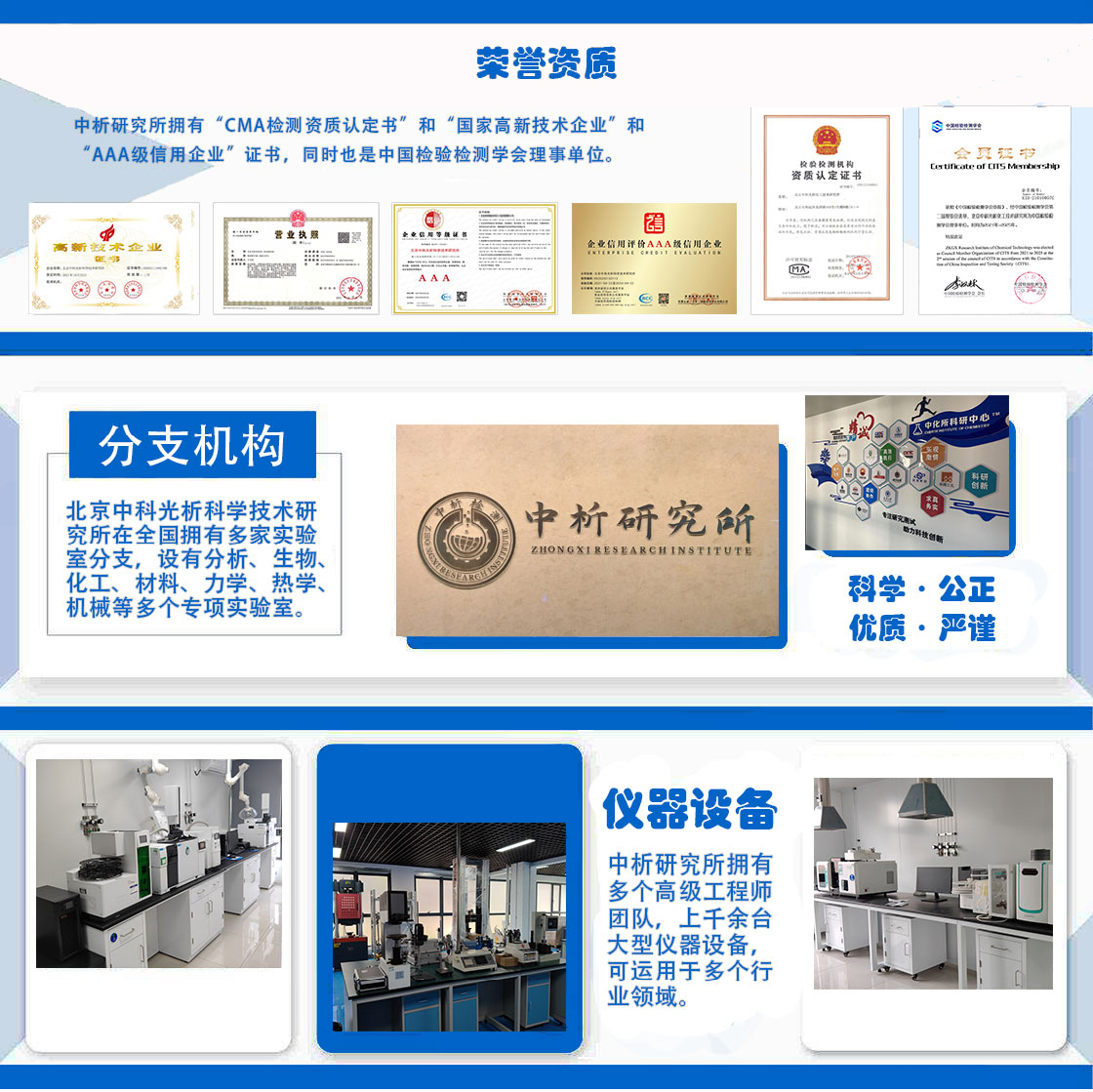
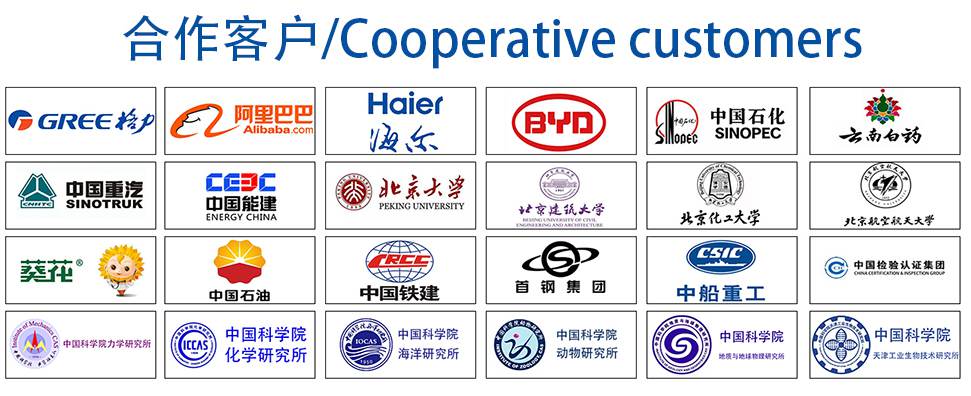