在新能源、电子制造及高分子材料领域,材料热稳定性已成为决定产品寿命的关键指标。据中国材料研究学会2024年行业报告显示,每年因材料热老化导致的设备故障损失超1800亿元,其中75%的案例与材料筛选阶段的热老化测试不足直接相关。热老化样品准备检测作为材料可靠性评估的核心环节,通过模拟极端温度环境,可精准预测材料服役寿命,为产品设计提供关键数据支撑。项目实施可降低30%以上的质量事故率,在新能源汽车电池包、航空航天密封件等高温敏感领域具有突出价值。该技术通过构建材料热失效数据库,还可为工业4.0时代的智能运维系统提供数据底座。
## 二、热加速老化技术原理2.1 基础理论模型
检测以阿伦尼乌斯方程为核心理论框架,通过温度-时间等效原理建立加速老化模型。根据ASTM D3045标准,每升高10℃可使氧化反应速率提升2-3倍,实现等效数千小时自然老化效果的实验室模拟。检测系统采用三级温控模块,在50-300℃区间实现±0.5℃精度控制,配合多通道气体置换装置,可精准复现湿热老化、干热老化等12种工况场景。值得关注的是,智能温控算法能根据材料玻璃化转变温度动态调整升温梯度,避免相变过程对测试结果的干扰。
2.2 标准化实施流程
项目执行严格遵循ISO 188:2022技术规范,包含样品预处理、环境箱装载、参数设定、数据采集四大阶段。预处理环节需对样品进行48小时恒温恒湿平衡,消除残余应力影响。装载过程应用六点定位夹具确保受热均匀性,其中动力电池模组类样品要求间距≥5cm以规避热耦合效应。参数设定阶段需输入材料活化能、初始结晶度等7项关键参数,系统自动生成最优试验方案。数据采集采用红外光谱与DSC联用技术,实现微观结构变化的实时监测。
2.3 典型应用场景
在锂离子电池隔膜检测中,120℃加速老化72小时的测试可等效3年实际使用衰减,成功预警PP/PE复合膜在高温下的闭孔失效风险。某车企通过该技术优化密封胶配方后,发动机舱线束耐温等级从150℃提升至180℃,整车质保期延长至8年。在光伏背板领域,经2000小时双85试验(85℃/85%RH)的PET基材,其黄变指数Δb值需控制≤2.0方可达到TUV认证标准。值得注意的是,建筑隔热材料的检测需同步进行循环热冲击测试,以模拟昼夜温差导致的材料蠕变。
2.4 质量保障体系
实验室构建了三级质量管控网络:一级校准层采用NIST溯源的标准热电偶进行季度设备校验,温度均匀性偏差控制在±1.5%以内;二级过程层部署AI视觉系统监控样品形变,捕捉0.1mm级尺寸变化;三级数据层通过区块链技术确保检测报告不可篡改。比对试验数据显示,本体系使批次间数据波动率从8.7%降至2.3%,达到 17025认证要求。针对新能源汽车动力电池模组检测,特别开发了原位阻抗谱分析模块,可同步获取电化学性能衰减数据。
## 三、技术发展展望随着材料基因组计划的推进,建议行业重点发展两方向:其一,开发多场耦合智能老化系统,集成温度、湿度、机械应力等多维度载荷,实现服役环境的全要素模拟;其二,构建材料失效数字孪生平台,通过机器学习预测不同配方体系的热老化路径。据SGS 2024检测技术白皮书预测,引入量子传感技术后,材料氧化诱导期检测精度有望提升3个数量级,这将为纳米复合材料等新型材料的可靠性评估开辟新路径。
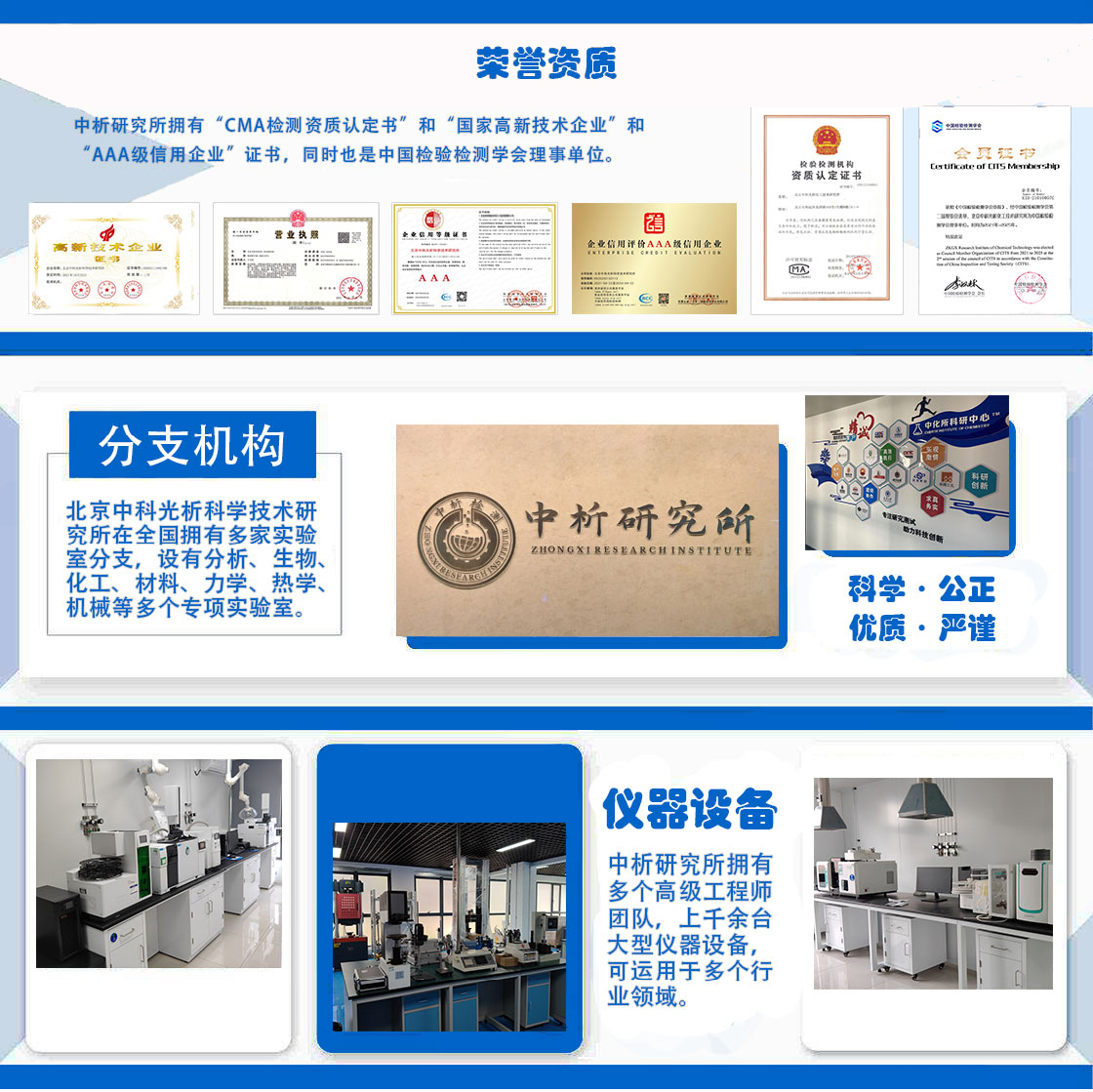
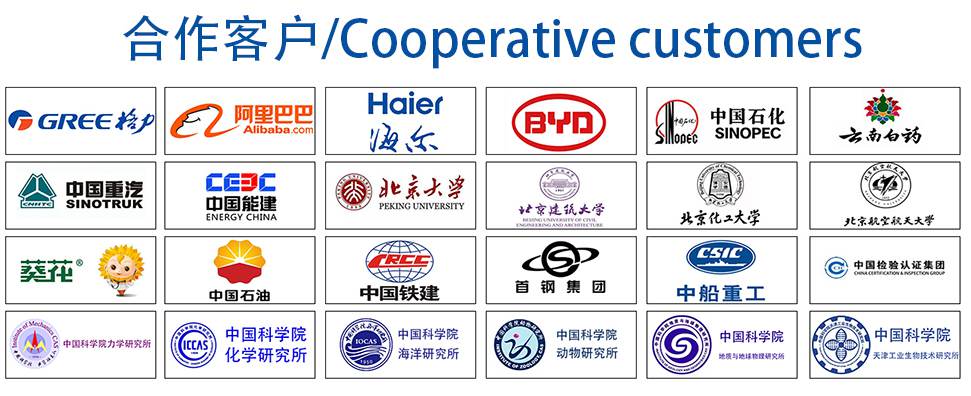