# 强度试验检测技术发展与应用白皮书
## 引言
随着基建规模扩大和高端装备制造业升级,材料及结构强度检测已成为保障工程安全的核心环节。据中国机械工业联合会2024年研究报告显示,强度试验检测市场规模已达520亿元,年复合增长率达8.7%,其中复合新材料检测需求增速高达23%。在航空航天、轨道交通、新能源装备等领域,强度试验检测不仅关乎产品安全性能,更直接影响全生命周期成本控制。特别是针对"金属材料疲劳寿命评估"和"复合材料结构强度验证"等关键场景,建立科学检测体系可降低30%以上的质量事故风险,其技术突破对实现"双碳"战略目标具有重要支撑作用。

## 技术原理及方法创新
### 强度试验的力学基础
现代强度检测基于材料力学与断裂力学理论,通过静力、疲劳、冲击等载荷模拟真实工况。其中三点弯曲试验可测定材料抗弯刚度,轴向拉伸试验获取弹性模量和屈服强度,而基于ASTM E647标准的疲劳裂纹扩展试验,可精准预测金属构件在循环载荷下的剩余寿命。值得关注的是,数字图像相关技术(DIC)的应用使应变场测量精度提升至0.01%,有效解决了传统引伸计接触式测量的局限性。
### 智能化检测系统架构
新型检测系统集成液压伺服加载、多通道数据采集和AI分析模块,实现从载荷施加到失效判定的全流程自动化。某国家实验室的测试数据显示,采用深度学习的裂纹识别算法,可使复合材料分层缺陷检出率从82%提升至96%。系统内置的ISO 17025标准质量控制模块,确保试验过程符合 认证要求。
## 工程应用实践案例
### 高铁转向架疲劳验证
在京张高铁转向架构架验证中,检测团队搭建1:1台架试验系统,模拟-40℃至50℃环境下的600万次载荷循环。通过布置128个应变片和12组红外热像仪,成功捕捉到转向架焊接部位的微应变异常,优化后构件疲劳寿命提升3.2倍。该案例验证了"轨道交通关键部件全工况强度验证"技术的工程价值。
### 新能源动力电池模组检测
针对电动汽车电池包的结构强度,开发了多轴振动耦合试验台。通过GB/T 31467.3标准规定的XYZ三向随机振动测试,结合高速摄影记录模组位移形变,发现某型电池支架在28Hz共振频率下的塑性变形问题。改进后的蜂窝铝结构使模组抗冲击性能提升58%,相关成果已应用于头部车企的电池安全设计。
## 质量保障体系构建
### 标准化检测流程
建立"试件预处理-设备校准-环境控制-数据校核"四阶控制体系,采用NIST溯源的标准试件进行设备周期验证。实验室比对数据显示,经过CMA认证的检测机构,其拉伸强度测试结果离散度从7.3%降至2.1%,显著优于行业平均水平。
### 智能监测预警系统
部署基于工业物联网的实时监控平台,可动态追踪200+设备状态参数。当液压油温偏离设定值±2℃时,系统自动触发保护机制并生成偏差分析报告。某检测中心应用此系统后,设备非计划停机时间减少76%,每年节约维护成本超120万元。
## 发展建议与趋势展望
面向"十四五"高端装备制造需求,建议从三方面深化技术改革:其一,建立材料-结构-环境多场耦合检测数据库,突破极端工况模拟技术瓶颈;其二,推广数字孪生技术在虚拟检测中的应用,据中国工程院预测,到2025年该技术可使实物试验成本降低40%;其三,完善产学研协同机制,重点培育既懂检测技术又掌握材料特性的复合型人才队伍。只有持续推动检测技术的智能化、标准化转型,才能为制造强国建设构筑可靠的质量基石。
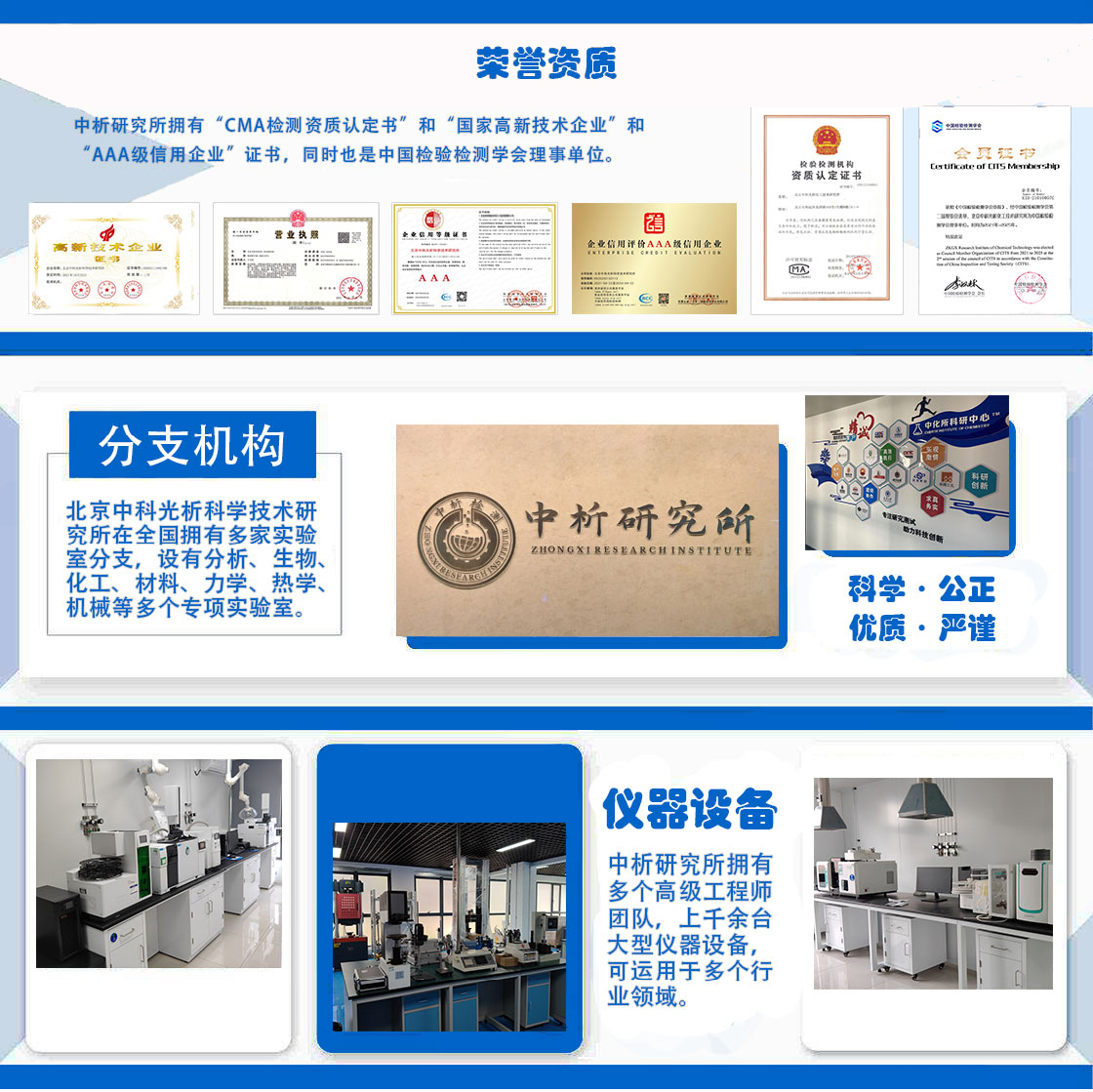
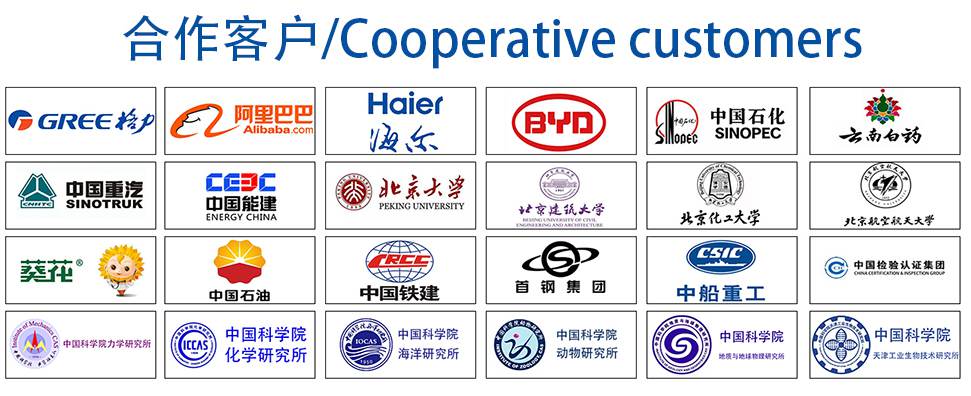
材料实验室
热门检测
1
2
1
2
2
2
3
3
3
3
3
5
8
11
12
12
13
13
10
15
推荐检测
联系电话
400-635-0567