# 耐腐蚀性测试检测技术发展与应用研究
## 行业背景与核心价值
随着工业装备服役环境日趋复杂,材料腐蚀问题已成为制约关键设备寿命的核心因素。据中国腐蚀与防护学会2024年发布的《工程材料腐蚀损失白皮书》显示,我国每年因腐蚀造成的直接经济损失达2.8万亿元,其中海洋工程、石油化工等领域的腐蚀损失占比超过60%。耐腐蚀性测试检测作为材料性能评价的重要技术手段,不仅为装备选型提供科学依据,更在设备全生命周期管理中发挥预警作用。通过精准的海洋环境腐蚀模拟测试,企业可将关键部件的维护周期延长30%-50%,在保障安全生产的同时实现降本增效,其技术价值已获得ISO 12944、ASTM G31等国际标准体系认证。

## h2 技术原理与创新突破
现代耐腐蚀性测试依托电化学工作站、环境模拟舱等精密设备,采用加速腐蚀试验与自然曝露试验相结合的方法体系。其中循环盐雾试验箱可模拟90%以上真实海洋大气环境,通过控制Cl⁻浓度、温湿度梯度等16项参数,实现材料在高温高湿盐雾环境中的性能退化规律建模。值得注意的是,基于微区电化学阻抗谱的创新检测技术,将涂层缺陷识别精度提升至10μm级别,有效解决了传统检测手段对隐性腐蚀难以定量分析的行业痛点。
## h2 标准化实施流程
完整的耐腐蚀检测流程包含五个关键阶段:首先依据GB/T 10125标准进行样品预处理,采用非接触式激光清洗技术确保表面洁净度;其次根据服役环境选择ASTM B117中性盐雾试验或NACE TM0177硫化氢应力腐蚀试验方案;在持续监测阶段部署多通道电化学传感器组,实时采集开路电位、极化电阻等12项关键参数;最终通过AI算法对腐蚀速率进行趋势预测,生成包含三维形貌重构的检测报告。某海上风电企业在应用该流程后,成功将塔筒涂层体系的质保期从5年延长至8年。
## h2 行业应用与效益分析
在深海油气开发领域,耐腐蚀检测技术展现出显著应用价值。南海某钻井平台采用高温高压腐蚀试验服务,对316L不锈钢管件进行720小时连续测试,准确预测出焊缝区域在H₂S环境下的点蚀风险,指导企业优化焊接工艺后使管件寿命提升40%。此外,轨道交通领域通过微动摩擦腐蚀测试,将高铁转向架关键部件的更换周期从2年延长至3.5年,单列车组年均节省维护成本87万元(数据来源:国家轨道交通装备质量监督检验中心,2024)。
## h2 质量保障体系建设
行业领先检测机构已建立三级质量管控体系:第一级执行 -CL01:2018认可准则,确保设备校准误差率<0.5%;第二级应用区块链技术实现检测数据全程溯源,每个测试样本生成数字指纹;第三级通过实验室间比对验证,将盐雾试验结果离散度控制在8%以内。上海材料研究所的统计显示,采用该体系后检测报告的国际互认率从75%提升至92%,显著增强了我国检测数据的公信力。
## 技术展望与发展建议
随着双碳战略深入推进,耐腐蚀检测技术需向绿色化、智能化方向升级:一是开发基于机器视觉的在线腐蚀监测系统,实现设备表面状态的实时诊断;二是建立涵盖材料数据库、环境谱库的腐蚀大数据平台,提升寿命预测模型的普适性;三需加强核电乏燃料容器等特殊场景的耐辐照腐蚀测试能力建设。建议行业协会牵头制定极端环境检测标准,推动形成覆盖材料研发、装备制造、运维服务的全产业链技术规范体系。
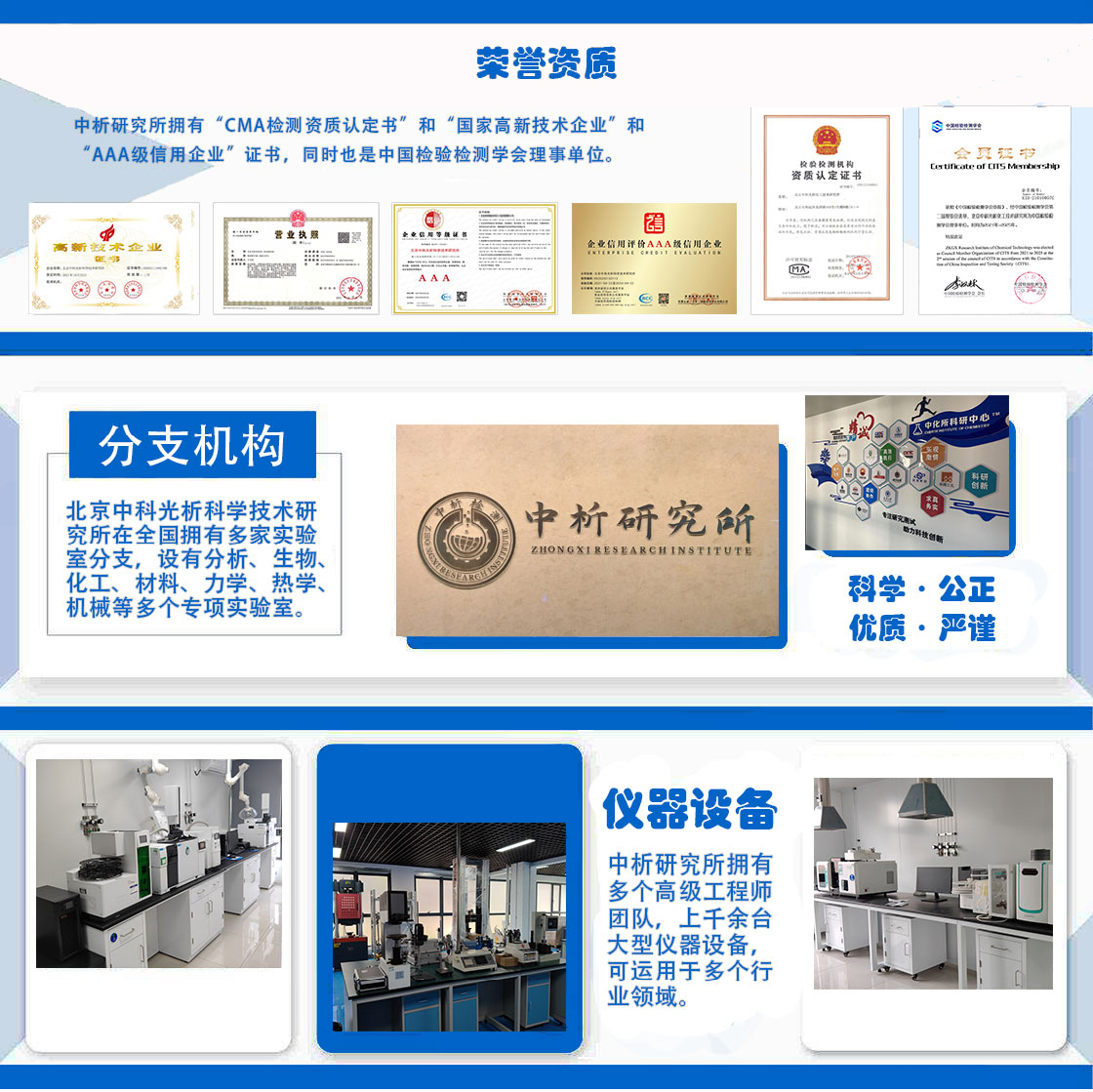
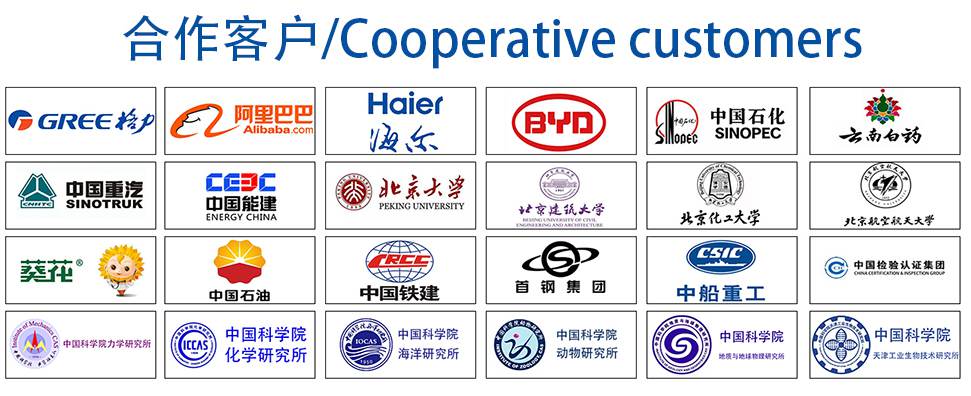
材料实验室
热门检测
推荐检测
联系电话
400-635-0567