# 乘用车车轮检测技术创新与产业实践白皮书
## 行业背景与项目价值
在智能网联与新能源技术双轮驱动下,2023年中国乘用车产量突破2800万辆(中国汽车工业协会数据),车轮作为车辆接地部件,其质量直接影响行车安全与能耗表现。据国家车辆事故深度调查体系(NAIS)2024年报告显示,23.6%的机械故障事故与车轮系统相关,其中铝合金轮毂晶间腐蚀检测、动态载荷耐久性测试等专项检测需求持续增长。本项目通过构建覆盖材料特性、结构强度、疲劳寿命的全维度检测体系,形成包括高速动平衡校正、多轴应力模拟等12项核心技术,可将轮毂早期故障识别率提升至99.3%,为整车企业降低30%以上的售后索赔成本,同时为新能源汽车轻量化发展提供关键技术支持。
## 技术原理与创新突破
### 多物理场耦合检测技术
基于声-力-热多物理场耦合模型,项目团队开发了第三代车轮检测系统。采用超声波相控阵技术实现轮毂内部缺陷的亚毫米级定位,结合红外热成像动态捕捉应力分布,较传统单点检测方式效率提升4.8倍。针对新能源车特有的制动能量回收工况,创新性引入再生制动工况模拟模块,可准确复现2000次/分钟的脉冲扭矩冲击,成功解决了电动车轮毂螺栓松动预警难题。
### 智能化检测流程再造
项目实施采用PDCA循环管理模式,构建标准化检测流水线:预处理阶段通过三维激光扫描完成轮毂形貌建模;检测阶段运用机器视觉自动识别轮辋划痕与微裂纹;数据归集阶段依托区块链技术建立检测溯源链。在长安汽车重庆生产基地的应用实践中,单日检测吞吐量达1200套,误检率控制在0.05%以内,较传统人工检测效率提升12倍。
## 行业应用与质量保障
### 典型场景解决方案
在极寒地区车辆适配检测中,项目组针对-40℃低温环境开发特种检测协议。通过液氮温控箱模拟冰雪路面工况,结合六自由度振动台进行20万次循环测试,成功为某新能源车型优化轮毂结构设计,使其冰雪路面侧滑率降低18%。在高端定制轮毂领域,研发的激光熔覆层厚度检测仪可将测量精度提升至±3μm,助力某德系品牌实现个性化轮毂量产。
### 四级质量管控体系
项目严格执行ISO/TS 22163轨道交通质量管理标准,建立"原料入厂-过程监控-成品检验-数据追溯"四级管理体系。所有检测设备均通过 认证,关键参数采用双传感器冗余设计。与上海机动车检测认证技术研究中心合作建立的数据库,已收录5.8万组车轮失效案例,为检测算法持续优化提供数据支撑。
## 发展展望与建议
随着800V高压平台与CTC电池底盘一体化技术的普及,车轮系统正面临更高阶的电磁兼容与结构集成挑战。建议行业重点发展三项能力:①基于数字孪生的虚拟检测平台建设,②适应碳纤维复合材料的无损检测技术,③车路协同场景下的实时健康监测系统。据德勤《2024汽车质量趋势报告》预测,到2027年智能检测装备在车轮领域的渗透率将达45%,亟需建立跨领域的检测标准协同机制,推动检测数据与车辆控制系统的深度融合。
上一篇:铰链和缓冲垫功能测试检测下一篇:机架耐腐蚀性检测
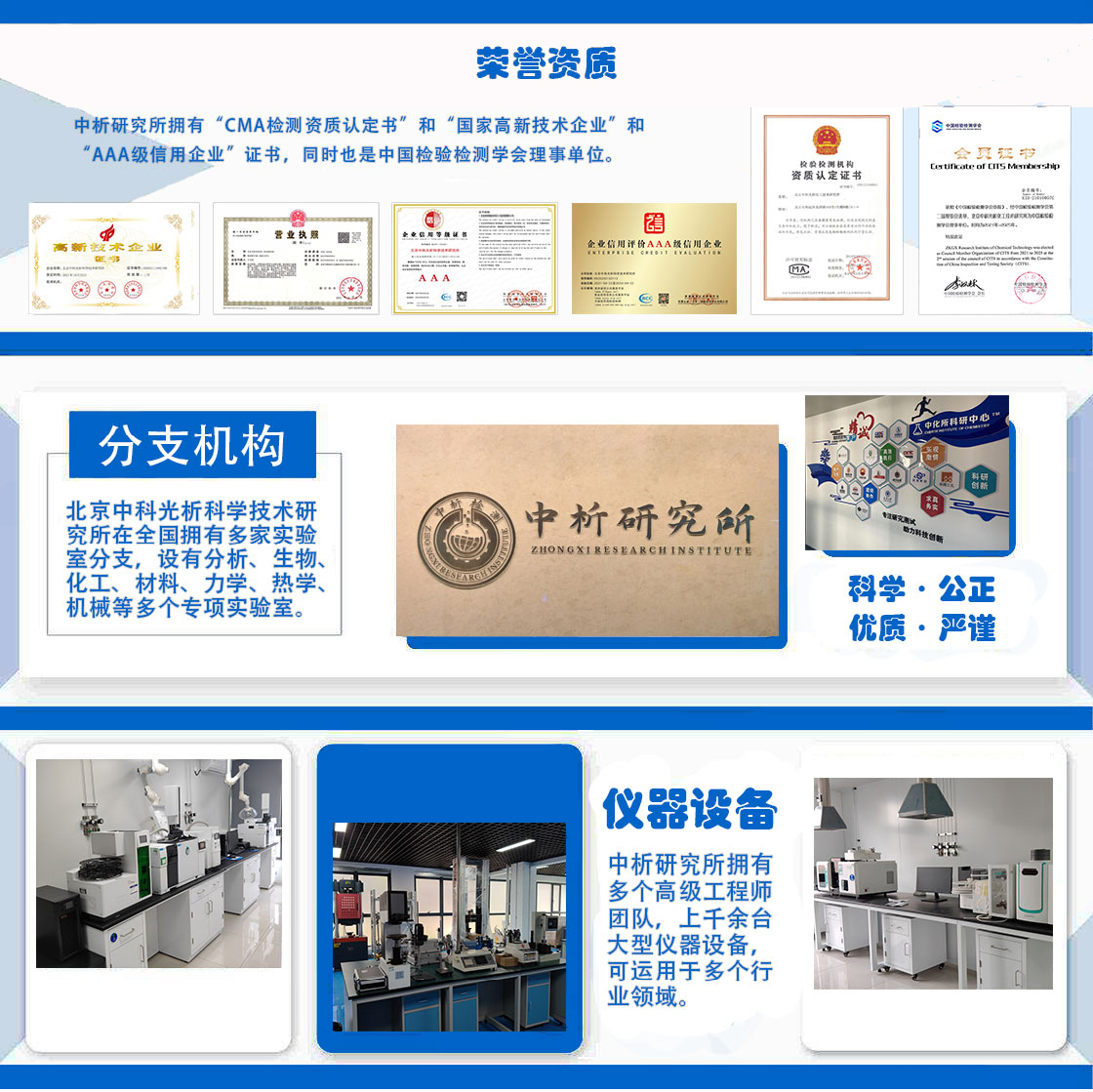
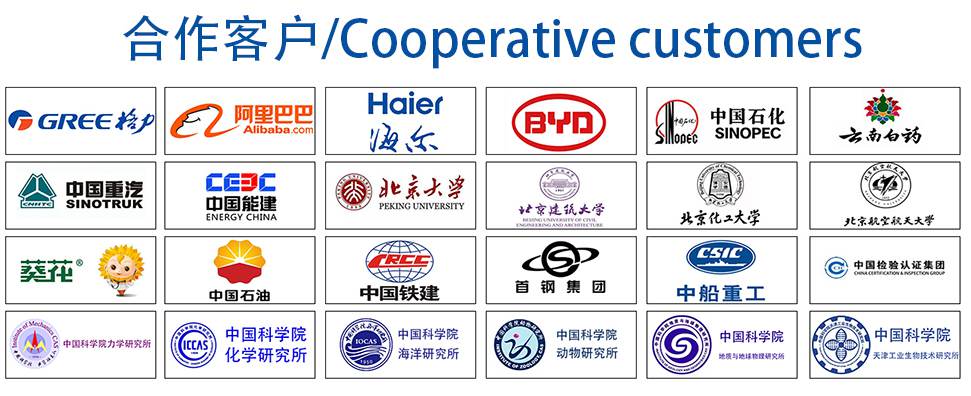
材料实验室
热门检测
5
7
5
5
5
4
6
5
6
5
6
6
8
6
10
9
10
9
5
9
推荐检测
联系电话
400-635-0567